Uniquely Australian bred corn hybrids developed with excellent trait packages
Pioneer® Brand corn hybrids are developed and tested in local conditions to ensure they represent superior products to what is currently available. Our hybrid corn varieties have something to offer farmers in all regions and cropping environments across Australia.
As with all our products, there’s always a Pioneer® Territory Sales Manager or Farm Services Consultant in your local area to help you choose the right hybrid corn seeds and provide on-farm backup and technical support.
We’re committed to providing helpful management advice and support to assist local farmers in making optimum profit from our products.
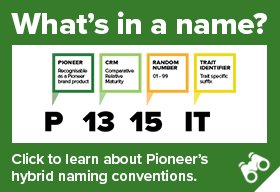
View or download our 2025-26 Summer Crop guide below.
{"data":{"hybrids":{"data":[{"id":79,"type":"hybrid","attributes":{"id":79,"region_id":null,"name":"P7524","content":"<p><img src=\"\/asset\/2035.png\" alt=\"P7524 - Segments and CRM.png\" width=\"274\" height=\"120\" \/> <img src=\"\/asset\/2036.png\" alt=\"P7524 - Maturity category.png\" width=\"162\" height=\"100\" \/><\/p>\n<h2>Stands and delivers tonnes of high-energy feed<\/h2>\n<p>P 7524 is the quickest option on the market with flexibility for silage and grain.<\/p>\n<p>An ultra short-season, silage and coastal grain specialist, P7524 is recognised as a reliable corn hybrid producing impressive silage yields with outstanding energy and whole plant digestibility.<\/p>\n<p>While combining very good early vigour with a tall growth habit, P7524 has also given very high dry-matter yields of good starch content.<\/p>\n<p>P7524 suits growers seeking to produce a large quantity of early-to-mature silage.<\/p>\n<p>Pioneer's P7524 hybrid corn is ideal for <strong>southern Victoria<\/strong> and <strong>Tasmania<\/strong>.<\/p>\n<p><img class=\"float-md-left mr-md-3 mb-3 mb-md-0\" src=\"\/asset\/1181.jpeg\" alt=\"600px-P7524-corn.jpg\" width=\"400\" height=\"\" \/><\/p>\n<p style=\"font-size: 16px;\">Discuss planting options with a <span style=\"font-weight: 400;\"><a title=\"Our team\" href=\"\/around-the-seed\/our-team\">Pioneer Brand Seeds representative<\/a> <\/span>near you.<\/p>\n<p style=\"font-size: 16px;\">Alternatively, register with us (below) to stay informed of field days in your region, affording you an opportunity to see for yourself the outstanding results of Pioneer's ultra short-season P7524 hybrid corn.<\/p>\n<p> <\/p>\n<p> <\/p>","content2":"<h3 style=\"color: #212529; font-family: proxima-nova, sans-serif;\">KEY FEATURES<\/h3>\n<ul>\n<li>Very tall plant with dependable root and stalk strength<\/li>\n<li>High levels of staygreen and toughness in drought conditions<\/li>\n<li>Delivers impressive yields of quality silage in the coolest maize growing regions<\/li>\n<\/ul>\n<p><img src=\"\/asset\/2037.png\" alt=\"P7524 - Growing regions recommendations.png\" width=\"338\" height=\"499\" \/><\/p>","image":{"id":2256,"parent_id":2033,"name":"PIO25015-007 Corn A4 P7524 MOCKUP.png","description":null,"storage":"assets","size":1125153,"extension":"png","mime_type":"image\/png","width":1731,"height":1487,"keywords":null,"usage":{"corn_hybrids.79":"P7524"},"created_at":"2025-07-02T22:42:40.000000Z","updated_at":"2025-07-02T22:42:52.000000Z","readonly":null,"value":null,"_meta":null,"node_path":[{"id":1362,"name":"Hybrid icons","parent_id":null},{"id":2033,"name":"CORN P7524","parent_id":1362},{"id":2256,"name":"PIO25015-007 Corn A4 P7524 MOCKUP.png","parent_id":2033}],"link":"\/asset\/2256.png","readable_size":"1.07 MB","secured":false,"secured_token":"eyJ0eXAiOiJKV1QiLCJhbGciOiJIUzI1NiJ9.eyJzdG9yYWdlcyI6WyJzZWN1cmVfYXNzZXRzIl0sImZpbGUiOjIyNTZ9.IueJbgJNjXsY17OsMtqhKThlb2whckrX0kWtkLWZJe4","full_path":"1362\/2033\/2256"},"custom_bag_image":null,"graph_image":null,"map_image":null,"new":0,"position":22,"plantheight":null,"type":"corn","title":"P7524","name_id":"p7524","meta_keywords":"yield, starch content, hybrid, corn, reliable, stalk, vigour, short season, P7524","meta_description":"Our ultra short-season, silage, and coastal grain specialist corn hybrid is known for its impressive yields and good starch content. This hybrid is reliable and delivers exceptional results. Learn more about its characteristics and benefits.","tolerancetrait":null,"producttype":null,"maturity":"Short Season","phenology":null,"blacklegroup":null,"grainoilcontent":null,"plantvigour":null,"cropstandability":null,"shattertolerance":null,"graintestweight":null,"blacklegrating":null,"blacklegresistancegrouping":null,"performertype":null,"crmnumber":null,"crmposition":null,"graintoyieldmaturity":null,"droughttolerance":null,"stalkstrength":null,"rootstrength":null,"staygreen":null,"huskcover":null,"northernleafblight":null,"commonrust":null,"cobrot":null,"harvestdaystart":null,"harvestdayend":null,"silageyieldmaturity":null,"drylandadaptability":null,"wholeplantdigestibility":null,"agronomy_traits":{"grain_yield_for_maturity":"7","husk_cover":"6","plant_height":"8","cob_rot_resistance":"7","dryland_adaptability":"7","northern_leaf_blight":"4","silage_yield_for_maturity":"8","staygreen":"7","whole_plant_digestibility":"8"},"disease_traits":[],"characteristics":[],"recommendations":[],"crm":"75","heading":"P7524 Corn Hybrid","corn_traits":null,"crop":null,"fully_researched_and_proven":null,"improved_fermentation":null,"aerobic_stability":null,"improved_fibre_digestibility":null,"sub_heading":null,"best":null,"intro":"Stands and delivers tonnes of high-energy feed.","tech_notes":2039,"trait_ratings_disclaimer":null,"usage":"[\"Grain\",\"Silage\"]","purpose":null,"genetic":null,"search":"p7524","keywords":null,"content_id":789,"usage_display":"Grain \/ Silage","bag_image":null},"meta":{"priority":"position","priority_order":"asc","active":1,"created_at":"2023-09-27 12:26:11","updated_at":"2025-07-03 10:42:52"},"schema":{"collectionType":"hybrids","attributes":{"region_id":{"name":"region_id","type":"int","isRequired":false,"keyType":"","length":"10","default":null},"name":{"name":"name","type":"string","isRequired":false,"keyType":"","default":"","length":"255"},"content":{"type":"text"},"content2":{"name":"content2","type":"text","isRequired":false,"keyType":"","default":null},"image":{"name":"image","type":"asset","isRequired":false,"keyType":"","length":"11","default":null,"extensions":["jpeg","jpg","png","svg"],"upload_dir":null,"upload_storage":null},"custom_bag_image":{"name":"custom_bag_image","type":"asset","isRequired":false,"keyType":"","length":"11","default":null,"extensions":["jpeg","jpg","png","svg"],"upload_dir":null,"upload_storage":null},"graph_image":{"name":"graph_image","type":"asset","isRequired":false,"keyType":"","length":"11","default":null,"extensions":["jpeg","jpg","png","svg"],"upload_dir":null,"upload_storage":null},"map_image":{"name":"map_image","type":"int","isRequired":false,"keyType":"","length":"11","default":null},"new":{"name":"new","type":"tinyint","isRequired":false,"keyType":"","length":"1","default":null},"position":{"name":"position","type":"int","isRequired":false,"keyType":"","length":"11","default":null},"plantheight":{"name":"plantheight","type":"int","isRequired":false,"keyType":"","length":"11","default":null},"type":{"name":"type","type":"string","isRequired":false,"keyType":"","default":"","length":"255"},"title":{"name":"title","type":"string","isRequired":false,"keyType":"","default":"","length":"255"},"name_id":{"name":"name_id","type":"string","isRequired":false,"keyType":"","default":"","length":"255"},"meta_keywords":{"name":"meta_keywords","type":"text","isRequired":false,"keyType":"","default":null},"meta_description":{"name":"meta_description","type":"text","isRequired":false,"keyType":"","default":null},"tolerancetrait":{"name":"tolerancetrait","type":"string","isRequired":false,"keyType":"","default":"","length":"255"},"producttype":{"name":"producttype","type":"string","isRequired":false,"keyType":"","default":"","length":"255"},"maturity":{"name":"maturity","type":"string","isRequired":false,"keyType":"","default":"","length":"30"},"phenology":{"name":"phenology","type":"string","isRequired":false,"keyType":"","default":"","length":"30"},"blacklegroup":{"name":"blacklegroup","type":"string","isRequired":false,"keyType":"","default":"","length":"255"},"grainoilcontent":{"name":"grainoilcontent","type":"int","isRequired":false,"keyType":"","length":"11","default":null},"plantvigour":{"name":"plantvigour","type":"int","isRequired":false,"keyType":"","length":"11","default":null},"cropstandability":{"name":"cropstandability","type":"int","isRequired":false,"keyType":"","length":"11","default":null},"shattertolerance":{"name":"shattertolerance","type":"int","isRequired":false,"keyType":"","length":"11","default":null},"graintestweight":{"name":"graintestweight","type":"string","isRequired":false,"keyType":"","default":"","length":"11"},"blacklegrating":{"name":"blacklegrating","type":"string","isRequired":false,"keyType":"","default":"","length":"255"},"blacklegresistancegrouping":{"name":"blacklegresistancegrouping","type":"string","isRequired":false,"keyType":"","default":"","length":"255"},"performertype":{"name":"performertype","type":"enum","isRequired":false,"keyType":"","default":null,"length":"255","values":["Elite","Proven"]},"crmnumber":{"name":"crmnumber","type":"int","isRequired":false,"keyType":"","length":"11","default":null},"crmposition":{"name":"crmposition","type":"string","isRequired":false,"keyType":"","default":"","length":"255"},"graintoyieldmaturity":{"name":"graintoyieldmaturity","type":"string","isRequired":false,"keyType":"","default":"","length":"255"},"droughttolerance":{"name":"droughttolerance","type":"string","isRequired":false,"keyType":"","default":"","length":"255"},"stalkstrength":{"name":"stalkstrength","type":"string","isRequired":false,"keyType":"","default":"","length":"255"},"rootstrength":{"name":"rootstrength","type":"string","isRequired":false,"keyType":"","default":"","length":"255"},"staygreen":{"name":"staygreen","type":"string","isRequired":false,"keyType":"","default":"","length":"255"},"huskcover":{"name":"huskcover","type":"string","isRequired":false,"keyType":"","default":"","length":"255"},"northernleafblight":{"name":"northernleafblight","type":"string","isRequired":false,"keyType":"","default":"","length":"255"},"commonrust":{"name":"commonrust","type":"string","isRequired":false,"keyType":"","default":"","length":"255"},"cobrot":{"name":"cobrot","type":"string","isRequired":false,"keyType":"","default":"","length":"255"},"harvestdaystart":{"name":"harvestdaystart","type":"int","isRequired":false,"keyType":"","length":"11","default":null},"harvestdayend":{"name":"harvestdayend","type":"int","isRequired":false,"keyType":"","length":"11","default":null},"silageyieldmaturity":{"name":"silageyieldmaturity","type":"string","isRequired":false,"keyType":"","default":"","length":"255"},"drylandadaptability":{"name":"drylandadaptability","type":"string","isRequired":false,"keyType":"","default":"","length":"255"},"wholeplantdigestibility":{"name":"wholeplantdigestibility","type":"string","isRequired":false,"keyType":"","default":"","length":"255"},"agronomy_traits":{"name":"agronomy_traits","type":"object","isRequired":false,"keyType":"","default":null,"fields":[]},"disease_traits":{"name":"disease_traits","type":"text","isRequired":false,"keyType":"","default":null},"characteristics":{"name":"characteristics","type":"text","isRequired":false,"keyType":"","default":null},"recommendations":{"name":"recommendations","type":"text","isRequired":false,"keyType":"","default":null},"crm":{"name":"crm","type":"string","isRequired":false,"keyType":"","default":"","length":"255"},"heading":{"name":"heading","type":"string","isRequired":false,"keyType":"","default":"","length":"255"},"corn_traits":{"name":"corn_traits","type":"text","isRequired":false,"keyType":"","default":null},"crop":{"name":"crop","type":"string","isRequired":false,"keyType":"","default":"","length":"255"},"fully_researched_and_proven":{"name":"fully_researched_and_proven","type":"int","isRequired":false,"keyType":"","length":"11","default":null},"improved_fermentation":{"name":"improved_fermentation","type":"int","isRequired":false,"keyType":"","length":"11","default":null},"aerobic_stability":{"name":"aerobic_stability","type":"int","isRequired":false,"keyType":"","length":"11","default":null},"improved_fibre_digestibility":{"name":"improved_fibre_digestibility","type":"int","isRequired":false,"keyType":"","length":"11","default":null},"sub_heading":{"name":"sub_heading","type":"string","isRequired":false,"keyType":"","default":"","length":"255"},"best":{"name":"best","type":"string","isRequired":false,"keyType":"","default":"","length":"255"},"intro":{"name":"intro","type":"string","isRequired":false,"keyType":"","default":"","length":"255"},"tech_notes":{"name":"tech_notes","type":"int","isRequired":false,"keyType":"","length":"11","default":null},"trait_ratings_disclaimer":{"name":"trait_ratings_disclaimer","type":"string","isRequired":false,"keyType":"","default":"","length":"255"},"usage":{"name":"usage","type":"string","isRequired":false,"keyType":"","default":"","length":"511"},"purpose":{"name":"purpose","type":"string","isRequired":false,"keyType":"","default":"","length":"255"},"genetic":{"name":"genetic","type":"string","isRequired":false,"keyType":"","default":"","length":"255"},"search":{"name":"search","type":"text","isRequired":false,"keyType":"MUL","default":null},"keywords":{"name":"keywords","type":"text","isRequired":false,"keyType":"","default":null},"usage_display":{"name":"usage_display","type":"string"},"bag_image":{"name":"bag_image","type":"string"}},"relationships":{"files":{"label":null,"type":"HasMany","class":"HybridFile"},"panels":{"label":null,"type":"HasMany","class":"Panel","refs":"\/panels\/_ref_"},"resource":{"label":null,"type":"HasOne","class":"Resource"},"attached_panels":{"label":null,"type":"BelongsToMany","class":"AttachedPanel","refs":"\/attached_panels\/_ref_"}}},"included":[],"label":"P7524"},{"id":64,"type":"hybrid","attributes":{"id":64,"region_id":null,"name":"P8500","content":"<p><img src=\"\/asset\/2028.png\" alt=\"P8500 - Segments and CRM.png\" width=\"264\" height=\"108\" \/> <img src=\"\/asset\/2030.png\" alt=\"P8500 - Maturity category.png\" width=\"187\" height=\"116\" \/><\/p>\n<h2>Yield leader with looks to match.<\/h2>\n<p>In southern regions, corn growers want a quick-maturing hybrid that can be harvested for either grain or silage.<\/p>\n<p>Pioneer's P8500 hybrid is an excellent option for both harvest objectives.<\/p>\n<p>The corn has high grain yield (CRM 85 ) and the sort of defensive traits growers expect.<\/p>\n<p>When combined with its digestibility and dryland adaptability, you can understand why the P8500 is such a popular choice for corn growers in southern regions. such as in the western Districts, Gippsland and Tasmania.<\/p>\n<p style=\"margin-bottom: 1.5rem; font-size: 16px;\">Reduce the guess work and discuss on-farm options with one of our Pioneer Seeds <a title=\"Contact a Pioneer representative\" href=\"\/contact-us\" target=\"_blank\" rel=\"noopener\"><span style=\"font-weight: 600;\">farm services consultants.<\/span><\/a> They have the knowledge and tools you need to minimise risk and maximise yield.<\/p>\n<p style=\"margin-bottom: 1.5rem; font-size: 16px;\">Alternatively, register with us (below) to stay informed of field days in your region, affording you an opportunity to see for yourself the impressive results of this quick maturing hybrid.<\/p>","content2":"<h3>KEY FEATURES<\/h3>\n<ul>\n<li>Tall hybrid and an industry leader for silage yield in its maturity<\/li>\n<li>Solid drought tolerance providing flexibility in double cropping programs<\/li>\n<li>Excellent feed quality combines with high silage yields, maximising energy when fed out<\/li>\n<\/ul>\n<p><img src=\"\/asset\/2029.png\" alt=\"P8500 - Growing region recommendations.png\" width=\"310\" height=\"454\" \/><\/p>","image":{"id":2257,"parent_id":2026,"name":"PIO25015-007 Corn A4 P8500 MOCKUP.png","description":null,"storage":"assets","size":1127948,"extension":"png","mime_type":"image\/png","width":1731,"height":1487,"keywords":null,"usage":{"corn_hybrids.64":"P8500"},"created_at":"2025-07-02T22:44:10.000000Z","updated_at":"2025-07-02T22:44:18.000000Z","readonly":null,"value":null,"_meta":null,"node_path":[{"id":1362,"name":"Hybrid icons","parent_id":null},{"id":2026,"name":"CORN P8500","parent_id":1362},{"id":2257,"name":"PIO25015-007 Corn A4 P8500 MOCKUP.png","parent_id":2026}],"link":"\/asset\/2257.png","readable_size":"1.08 MB","secured":false,"secured_token":"eyJ0eXAiOiJKV1QiLCJhbGciOiJIUzI1NiJ9.eyJzdG9yYWdlcyI6WyJzZWN1cmVfYXNzZXRzIl0sImZpbGUiOjIyNTd9._SUMr5XJpHebWylAtvt-kXpZAFdMKGY2XmWB3Kv2t3E","full_path":"1362\/2026\/2257"},"custom_bag_image":null,"graph_image":null,"map_image":null,"new":0,"position":24,"plantheight":null,"type":"corn","title":"P8500","name_id":"p8500","meta_keywords":"corn, hybrid, yield, Tasmania, silage, double, seed, Australian,","meta_description":"Looking for ultra quick maturing hybrid corn varieties for high yield and silage quality? Check out the best options for southern coastal and Tasmania farmers, including double cropping strategies.","tolerancetrait":null,"producttype":null,"maturity":"Short Season","phenology":null,"blacklegroup":null,"grainoilcontent":null,"plantvigour":null,"cropstandability":null,"shattertolerance":null,"graintestweight":null,"blacklegrating":null,"blacklegresistancegrouping":null,"performertype":null,"crmnumber":null,"crmposition":null,"graintoyieldmaturity":null,"droughttolerance":null,"stalkstrength":null,"rootstrength":null,"staygreen":null,"huskcover":null,"northernleafblight":null,"commonrust":null,"cobrot":null,"harvestdaystart":null,"harvestdayend":null,"silageyieldmaturity":null,"drylandadaptability":null,"wholeplantdigestibility":null,"agronomy_traits":{"grain_yield_for_maturity":"7","husk_cover":"6","plant_height":"8","cob_rot_resistance":"8","dryland_adaptability":"8","northern_leaf_blight":"5","silage_yield_for_maturity":"9","staygreen":"7","whole_plant_digestibility":"7"},"disease_traits":[],"characteristics":[],"recommendations":[],"crm":"85","heading":"P8500 Corn Hybrid","corn_traits":null,"crop":null,"fully_researched_and_proven":null,"improved_fermentation":null,"aerobic_stability":null,"improved_fibre_digestibility":null,"sub_heading":null,"best":null,"intro":"Yield leader with looks to match.","tech_notes":2032,"trait_ratings_disclaimer":null,"usage":"[\"Grain\",\"Silage\"]","purpose":null,"genetic":null,"search":"p8500","keywords":null,"content_id":412,"usage_display":"Grain \/ Silage","bag_image":null},"meta":{"priority":"position","priority_order":"asc","active":1,"created_at":"2021-07-12 13:18:15","updated_at":"2025-07-03 10:44:18"},"schema":{"collectionType":"hybrids","attributes":{"region_id":{"name":"region_id","type":"int","isRequired":false,"keyType":"","length":"10","default":null},"name":{"name":"name","type":"string","isRequired":false,"keyType":"","default":"","length":"255"},"content":{"type":"text"},"content2":{"name":"content2","type":"text","isRequired":false,"keyType":"","default":null},"image":{"name":"image","type":"asset","isRequired":false,"keyType":"","length":"11","default":null,"extensions":["jpeg","jpg","png","svg"],"upload_dir":null,"upload_storage":null},"custom_bag_image":{"name":"custom_bag_image","type":"asset","isRequired":false,"keyType":"","length":"11","default":null,"extensions":["jpeg","jpg","png","svg"],"upload_dir":null,"upload_storage":null},"graph_image":{"name":"graph_image","type":"asset","isRequired":false,"keyType":"","length":"11","default":null,"extensions":["jpeg","jpg","png","svg"],"upload_dir":null,"upload_storage":null},"map_image":{"name":"map_image","type":"int","isRequired":false,"keyType":"","length":"11","default":null},"new":{"name":"new","type":"tinyint","isRequired":false,"keyType":"","length":"1","default":null},"position":{"name":"position","type":"int","isRequired":false,"keyType":"","length":"11","default":null},"plantheight":{"name":"plantheight","type":"int","isRequired":false,"keyType":"","length":"11","default":null},"type":{"name":"type","type":"string","isRequired":false,"keyType":"","default":"","length":"255"},"title":{"name":"title","type":"string","isRequired":false,"keyType":"","default":"","length":"255"},"name_id":{"name":"name_id","type":"string","isRequired":false,"keyType":"","default":"","length":"255"},"meta_keywords":{"name":"meta_keywords","type":"text","isRequired":false,"keyType":"","default":null},"meta_description":{"name":"meta_description","type":"text","isRequired":false,"keyType":"","default":null},"tolerancetrait":{"name":"tolerancetrait","type":"string","isRequired":false,"keyType":"","default":"","length":"255"},"producttype":{"name":"producttype","type":"string","isRequired":false,"keyType":"","default":"","length":"255"},"maturity":{"name":"maturity","type":"string","isRequired":false,"keyType":"","default":"","length":"30"},"phenology":{"name":"phenology","type":"string","isRequired":false,"keyType":"","default":"","length":"30"},"blacklegroup":{"name":"blacklegroup","type":"string","isRequired":false,"keyType":"","default":"","length":"255"},"grainoilcontent":{"name":"grainoilcontent","type":"int","isRequired":false,"keyType":"","length":"11","default":null},"plantvigour":{"name":"plantvigour","type":"int","isRequired":false,"keyType":"","length":"11","default":null},"cropstandability":{"name":"cropstandability","type":"int","isRequired":false,"keyType":"","length":"11","default":null},"shattertolerance":{"name":"shattertolerance","type":"int","isRequired":false,"keyType":"","length":"11","default":null},"graintestweight":{"name":"graintestweight","type":"string","isRequired":false,"keyType":"","default":"","length":"11"},"blacklegrating":{"name":"blacklegrating","type":"string","isRequired":false,"keyType":"","default":"","length":"255"},"blacklegresistancegrouping":{"name":"blacklegresistancegrouping","type":"string","isRequired":false,"keyType":"","default":"","length":"255"},"performertype":{"name":"performertype","type":"enum","isRequired":false,"keyType":"","default":null,"length":"255","values":["Elite","Proven"]},"crmnumber":{"name":"crmnumber","type":"int","isRequired":false,"keyType":"","length":"11","default":null},"crmposition":{"name":"crmposition","type":"string","isRequired":false,"keyType":"","default":"","length":"255"},"graintoyieldmaturity":{"name":"graintoyieldmaturity","type":"string","isRequired":false,"keyType":"","default":"","length":"255"},"droughttolerance":{"name":"droughttolerance","type":"string","isRequired":false,"keyType":"","default":"","length":"255"},"stalkstrength":{"name":"stalkstrength","type":"string","isRequired":false,"keyType":"","default":"","length":"255"},"rootstrength":{"name":"rootstrength","type":"string","isRequired":false,"keyType":"","default":"","length":"255"},"staygreen":{"name":"staygreen","type":"string","isRequired":false,"keyType":"","default":"","length":"255"},"huskcover":{"name":"huskcover","type":"string","isRequired":false,"keyType":"","default":"","length":"255"},"northernleafblight":{"name":"northernleafblight","type":"string","isRequired":false,"keyType":"","default":"","length":"255"},"commonrust":{"name":"commonrust","type":"string","isRequired":false,"keyType":"","default":"","length":"255"},"cobrot":{"name":"cobrot","type":"string","isRequired":false,"keyType":"","default":"","length":"255"},"harvestdaystart":{"name":"harvestdaystart","type":"int","isRequired":false,"keyType":"","length":"11","default":null},"harvestdayend":{"name":"harvestdayend","type":"int","isRequired":false,"keyType":"","length":"11","default":null},"silageyieldmaturity":{"name":"silageyieldmaturity","type":"string","isRequired":false,"keyType":"","default":"","length":"255"},"drylandadaptability":{"name":"drylandadaptability","type":"string","isRequired":false,"keyType":"","default":"","length":"255"},"wholeplantdigestibility":{"name":"wholeplantdigestibility","type":"string","isRequired":false,"keyType":"","default":"","length":"255"},"agronomy_traits":{"name":"agronomy_traits","type":"object","isRequired":false,"keyType":"","default":null,"fields":[]},"disease_traits":{"name":"disease_traits","type":"text","isRequired":false,"keyType":"","default":null},"characteristics":{"name":"characteristics","type":"text","isRequired":false,"keyType":"","default":null},"recommendations":{"name":"recommendations","type":"text","isRequired":false,"keyType":"","default":null},"crm":{"name":"crm","type":"string","isRequired":false,"keyType":"","default":"","length":"255"},"heading":{"name":"heading","type":"string","isRequired":false,"keyType":"","default":"","length":"255"},"corn_traits":{"name":"corn_traits","type":"text","isRequired":false,"keyType":"","default":null},"crop":{"name":"crop","type":"string","isRequired":false,"keyType":"","default":"","length":"255"},"fully_researched_and_proven":{"name":"fully_researched_and_proven","type":"int","isRequired":false,"keyType":"","length":"11","default":null},"improved_fermentation":{"name":"improved_fermentation","type":"int","isRequired":false,"keyType":"","length":"11","default":null},"aerobic_stability":{"name":"aerobic_stability","type":"int","isRequired":false,"keyType":"","length":"11","default":null},"improved_fibre_digestibility":{"name":"improved_fibre_digestibility","type":"int","isRequired":false,"keyType":"","length":"11","default":null},"sub_heading":{"name":"sub_heading","type":"string","isRequired":false,"keyType":"","default":"","length":"255"},"best":{"name":"best","type":"string","isRequired":false,"keyType":"","default":"","length":"255"},"intro":{"name":"intro","type":"string","isRequired":false,"keyType":"","default":"","length":"255"},"tech_notes":{"name":"tech_notes","type":"int","isRequired":false,"keyType":"","length":"11","default":null},"trait_ratings_disclaimer":{"name":"trait_ratings_disclaimer","type":"string","isRequired":false,"keyType":"","default":"","length":"255"},"usage":{"name":"usage","type":"string","isRequired":false,"keyType":"","default":"","length":"511"},"purpose":{"name":"purpose","type":"string","isRequired":false,"keyType":"","default":"","length":"255"},"genetic":{"name":"genetic","type":"string","isRequired":false,"keyType":"","default":"","length":"255"},"search":{"name":"search","type":"text","isRequired":false,"keyType":"MUL","default":null},"keywords":{"name":"keywords","type":"text","isRequired":false,"keyType":"","default":null},"usage_display":{"name":"usage_display","type":"string"},"bag_image":{"name":"bag_image","type":"string"}},"relationships":{"files":{"label":null,"type":"HasMany","class":"HybridFile"},"panels":{"label":null,"type":"HasMany","class":"Panel","refs":"\/panels\/_ref_"},"resource":{"label":null,"type":"HasOne","class":"Resource"},"attached_panels":{"label":null,"type":"BelongsToMany","class":"AttachedPanel","refs":"\/attached_panels\/_ref_"}}},"included":[],"label":"P8500"},{"id":88,"type":"hybrid","attributes":{"id":88,"region_id":null,"name":"P92575","content":"<p><img src=\"\/asset\/2023.png\" alt=\"P92575 - Segments and CRM.png\" width=\"254\" height=\"104\" \/> <img src=\"\/asset\/2021.png\" alt=\"P92575 - Maturity category.png\" width=\"183\" height=\"112\" \/><\/p>\n<h2>Solid, balanced hybrid, with top-of-the-line foliar health.<\/h2>\n<p>P92575 is the 'go to' hybrid for silage yield and quick grain opportunities. Tall structure partnered with excellent standability gives silage and grain growers flexibility in cool environments. P92575 produces large cobs and drives top end yield for maturity.<\/p>","content2":"<h3>KEY FEATURES<\/h3>\n<ul>\n<li>Competitive silage yields compared to P9127, which it replaces<\/li>\n<li>Moderately tall with strong agronomics, superior root and stalk strength<\/li>\n<li>Combines excellent drought tolerance, staygreen, Northern Leaf Blight and Rust resistances to deliver high and stable silage yields<\/li>\n<li>Late season staygreen and plant health delivers a wide harvest window and silage with exceptional digestibility and energy<\/li>\n<\/ul>\n<p><img src=\"\/asset\/2024.png\" alt=\"P92575 - Growing region recommendations.png\" width=\"238\" height=\"366\" \/><\/p>","image":{"id":2258,"parent_id":2019,"name":"PIO25015-007 Corn A4 P92575 MOCKUP.png","description":null,"storage":"assets","size":1125686,"extension":"png","mime_type":"image\/png","width":1731,"height":1487,"keywords":null,"usage":{"corn_hybrids.88":"P92575"},"created_at":"2025-07-02T22:45:01.000000Z","updated_at":"2025-07-02T22:45:10.000000Z","readonly":null,"value":null,"_meta":null,"node_path":[{"id":1362,"name":"Hybrid icons","parent_id":null},{"id":2019,"name":"CORN P92575","parent_id":1362},{"id":2258,"name":"PIO25015-007 Corn A4 P92575 MOCKUP.png","parent_id":2019}],"link":"\/asset\/2258.png","readable_size":"1.07 MB","secured":false,"secured_token":"eyJ0eXAiOiJKV1QiLCJhbGciOiJIUzI1NiJ9.eyJzdG9yYWdlcyI6WyJzZWN1cmVfYXNzZXRzIl0sImZpbGUiOjIyNTh9.Rk30yqvX6vPdK-aeEo1IIJQjfh9qnZL666sCfmFb3YI","full_path":"1362\/2019\/2258"},"custom_bag_image":null,"graph_image":null,"map_image":null,"new":0,"position":25,"plantheight":null,"type":"corn","title":"P92575","name_id":"P92575","meta_keywords":null,"meta_description":null,"tolerancetrait":null,"producttype":null,"maturity":"Short Season","phenology":null,"blacklegroup":null,"grainoilcontent":null,"plantvigour":null,"cropstandability":null,"shattertolerance":null,"graintestweight":null,"blacklegrating":null,"blacklegresistancegrouping":null,"performertype":null,"crmnumber":null,"crmposition":null,"graintoyieldmaturity":null,"droughttolerance":null,"stalkstrength":null,"rootstrength":null,"staygreen":null,"huskcover":null,"northernleafblight":null,"commonrust":null,"cobrot":null,"harvestdaystart":null,"harvestdayend":null,"silageyieldmaturity":null,"drylandadaptability":null,"wholeplantdigestibility":null,"agronomy_traits":{"grain_yield_for_maturity":"9","husk_cover":"5","plant_height":"8","cob_rot_resistance":"8","dryland_adaptability":"8","northern_leaf_blight":"8","silage_yield_for_maturity":"9","staygreen":"9","whole_plant_digestibility":"7"},"disease_traits":[],"characteristics":[],"recommendations":[],"crm":"92","heading":"P92575 Corn Hybrid","corn_traits":null,"crop":null,"fully_researched_and_proven":null,"improved_fermentation":null,"aerobic_stability":null,"improved_fibre_digestibility":null,"sub_heading":null,"best":null,"intro":"Solid, balanced hybrid, with top-of-the-line foliar health","tech_notes":2025,"trait_ratings_disclaimer":null,"usage":"[\"Grain\",\"Silage\"]","purpose":null,"genetic":null,"search":"p92575","keywords":null,"content_id":892,"usage_display":"Grain \/ Silage","bag_image":null},"meta":{"priority":"position","priority_order":"asc","active":1,"created_at":"2024-07-14 17:54:21","updated_at":"2025-07-03 10:45:10"},"schema":{"collectionType":"hybrids","attributes":{"region_id":{"name":"region_id","type":"int","isRequired":false,"keyType":"","length":"10","default":null},"name":{"name":"name","type":"string","isRequired":false,"keyType":"","default":"","length":"255"},"content":{"type":"text"},"content2":{"name":"content2","type":"text","isRequired":false,"keyType":"","default":null},"image":{"name":"image","type":"asset","isRequired":false,"keyType":"","length":"11","default":null,"extensions":["jpeg","jpg","png","svg"],"upload_dir":null,"upload_storage":null},"custom_bag_image":{"name":"custom_bag_image","type":"asset","isRequired":false,"keyType":"","length":"11","default":null,"extensions":["jpeg","jpg","png","svg"],"upload_dir":null,"upload_storage":null},"graph_image":{"name":"graph_image","type":"asset","isRequired":false,"keyType":"","length":"11","default":null,"extensions":["jpeg","jpg","png","svg"],"upload_dir":null,"upload_storage":null},"map_image":{"name":"map_image","type":"int","isRequired":false,"keyType":"","length":"11","default":null},"new":{"name":"new","type":"tinyint","isRequired":false,"keyType":"","length":"1","default":null},"position":{"name":"position","type":"int","isRequired":false,"keyType":"","length":"11","default":null},"plantheight":{"name":"plantheight","type":"int","isRequired":false,"keyType":"","length":"11","default":null},"type":{"name":"type","type":"string","isRequired":false,"keyType":"","default":"","length":"255"},"title":{"name":"title","type":"string","isRequired":false,"keyType":"","default":"","length":"255"},"name_id":{"name":"name_id","type":"string","isRequired":false,"keyType":"","default":"","length":"255"},"meta_keywords":{"name":"meta_keywords","type":"text","isRequired":false,"keyType":"","default":null},"meta_description":{"name":"meta_description","type":"text","isRequired":false,"keyType":"","default":null},"tolerancetrait":{"name":"tolerancetrait","type":"string","isRequired":false,"keyType":"","default":"","length":"255"},"producttype":{"name":"producttype","type":"string","isRequired":false,"keyType":"","default":"","length":"255"},"maturity":{"name":"maturity","type":"string","isRequired":false,"keyType":"","default":"","length":"30"},"phenology":{"name":"phenology","type":"string","isRequired":false,"keyType":"","default":"","length":"30"},"blacklegroup":{"name":"blacklegroup","type":"string","isRequired":false,"keyType":"","default":"","length":"255"},"grainoilcontent":{"name":"grainoilcontent","type":"int","isRequired":false,"keyType":"","length":"11","default":null},"plantvigour":{"name":"plantvigour","type":"int","isRequired":false,"keyType":"","length":"11","default":null},"cropstandability":{"name":"cropstandability","type":"int","isRequired":false,"keyType":"","length":"11","default":null},"shattertolerance":{"name":"shattertolerance","type":"int","isRequired":false,"keyType":"","length":"11","default":null},"graintestweight":{"name":"graintestweight","type":"string","isRequired":false,"keyType":"","default":"","length":"11"},"blacklegrating":{"name":"blacklegrating","type":"string","isRequired":false,"keyType":"","default":"","length":"255"},"blacklegresistancegrouping":{"name":"blacklegresistancegrouping","type":"string","isRequired":false,"keyType":"","default":"","length":"255"},"performertype":{"name":"performertype","type":"enum","isRequired":false,"keyType":"","default":null,"length":"255","values":["Elite","Proven"]},"crmnumber":{"name":"crmnumber","type":"int","isRequired":false,"keyType":"","length":"11","default":null},"crmposition":{"name":"crmposition","type":"string","isRequired":false,"keyType":"","default":"","length":"255"},"graintoyieldmaturity":{"name":"graintoyieldmaturity","type":"string","isRequired":false,"keyType":"","default":"","length":"255"},"droughttolerance":{"name":"droughttolerance","type":"string","isRequired":false,"keyType":"","default":"","length":"255"},"stalkstrength":{"name":"stalkstrength","type":"string","isRequired":false,"keyType":"","default":"","length":"255"},"rootstrength":{"name":"rootstrength","type":"string","isRequired":false,"keyType":"","default":"","length":"255"},"staygreen":{"name":"staygreen","type":"string","isRequired":false,"keyType":"","default":"","length":"255"},"huskcover":{"name":"huskcover","type":"string","isRequired":false,"keyType":"","default":"","length":"255"},"northernleafblight":{"name":"northernleafblight","type":"string","isRequired":false,"keyType":"","default":"","length":"255"},"commonrust":{"name":"commonrust","type":"string","isRequired":false,"keyType":"","default":"","length":"255"},"cobrot":{"name":"cobrot","type":"string","isRequired":false,"keyType":"","default":"","length":"255"},"harvestdaystart":{"name":"harvestdaystart","type":"int","isRequired":false,"keyType":"","length":"11","default":null},"harvestdayend":{"name":"harvestdayend","type":"int","isRequired":false,"keyType":"","length":"11","default":null},"silageyieldmaturity":{"name":"silageyieldmaturity","type":"string","isRequired":false,"keyType":"","default":"","length":"255"},"drylandadaptability":{"name":"drylandadaptability","type":"string","isRequired":false,"keyType":"","default":"","length":"255"},"wholeplantdigestibility":{"name":"wholeplantdigestibility","type":"string","isRequired":false,"keyType":"","default":"","length":"255"},"agronomy_traits":{"name":"agronomy_traits","type":"object","isRequired":false,"keyType":"","default":null,"fields":[]},"disease_traits":{"name":"disease_traits","type":"text","isRequired":false,"keyType":"","default":null},"characteristics":{"name":"characteristics","type":"text","isRequired":false,"keyType":"","default":null},"recommendations":{"name":"recommendations","type":"text","isRequired":false,"keyType":"","default":null},"crm":{"name":"crm","type":"string","isRequired":false,"keyType":"","default":"","length":"255"},"heading":{"name":"heading","type":"string","isRequired":false,"keyType":"","default":"","length":"255"},"corn_traits":{"name":"corn_traits","type":"text","isRequired":false,"keyType":"","default":null},"crop":{"name":"crop","type":"string","isRequired":false,"keyType":"","default":"","length":"255"},"fully_researched_and_proven":{"name":"fully_researched_and_proven","type":"int","isRequired":false,"keyType":"","length":"11","default":null},"improved_fermentation":{"name":"improved_fermentation","type":"int","isRequired":false,"keyType":"","length":"11","default":null},"aerobic_stability":{"name":"aerobic_stability","type":"int","isRequired":false,"keyType":"","length":"11","default":null},"improved_fibre_digestibility":{"name":"improved_fibre_digestibility","type":"int","isRequired":false,"keyType":"","length":"11","default":null},"sub_heading":{"name":"sub_heading","type":"string","isRequired":false,"keyType":"","default":"","length":"255"},"best":{"name":"best","type":"string","isRequired":false,"keyType":"","default":"","length":"255"},"intro":{"name":"intro","type":"string","isRequired":false,"keyType":"","default":"","length":"255"},"tech_notes":{"name":"tech_notes","type":"int","isRequired":false,"keyType":"","length":"11","default":null},"trait_ratings_disclaimer":{"name":"trait_ratings_disclaimer","type":"string","isRequired":false,"keyType":"","default":"","length":"255"},"usage":{"name":"usage","type":"string","isRequired":false,"keyType":"","default":"","length":"511"},"purpose":{"name":"purpose","type":"string","isRequired":false,"keyType":"","default":"","length":"255"},"genetic":{"name":"genetic","type":"string","isRequired":false,"keyType":"","default":"","length":"255"},"search":{"name":"search","type":"text","isRequired":false,"keyType":"MUL","default":null},"keywords":{"name":"keywords","type":"text","isRequired":false,"keyType":"","default":null},"usage_display":{"name":"usage_display","type":"string"},"bag_image":{"name":"bag_image","type":"string"}},"relationships":{"files":{"label":null,"type":"HasMany","class":"HybridFile"},"panels":{"label":null,"type":"HasMany","class":"Panel","refs":"\/panels\/_ref_"},"resource":{"label":null,"type":"HasOne","class":"Resource"},"attached_panels":{"label":null,"type":"BelongsToMany","class":"AttachedPanel","refs":"\/attached_panels\/_ref_"}}},"included":[],"label":"P92575"},{"id":87,"type":"hybrid","attributes":{"id":87,"region_id":null,"name":"P9978","content":"<p><img src=\"\/asset\/2015.png\" alt=\"P9978 - Segments and CRM.png\" width=\"266\" height=\"109\" \/> <img src=\"\/asset\/2014.png\" alt=\"P9978 - Maturity category.png\" width=\"161\" height=\"98\" \/><\/p>\n<h2>Very productive. Very stable. Very defensive.<\/h2>\n<p>P9978 sets the new standard in grain and silage yield for maturity. All growers will reap the rewards of the excellent defensive traits, standability, and reliability of yield across seasons. Dryland growers can rely on the drought tolerance of this hybrid to ensure safe harvest of their silage or grain. <\/p>","content2":"<h3>KEY FEATURES<\/h3>\n<ul>\n<li>A moderately tall plant with low ear placement, strong roots strength, superior drought tolerance, staygreen and Northern Leaf Blight resistance<\/li>\n<li>Delivers exceptional silage yields, in this maturity, with excellent feed quality<\/li>\n<li>Key maturity for maximising silage yield across a broad range of environments<\/li>\n<\/ul>\n<p><img src=\"\/asset\/2017.png\" alt=\"P9978 - Growing region recommendations.png\" width=\"276\" height=\"424\" \/><\/p>","image":{"id":2259,"parent_id":2012,"name":"PIO25015-007 Corn A4 P9978 MOCKUP.png","description":null,"storage":"assets","size":1091839,"extension":"png","mime_type":"image\/png","width":1731,"height":1487,"keywords":null,"usage":{"corn_hybrids.87":"P9978"},"created_at":"2025-07-02T22:46:10.000000Z","updated_at":"2025-07-02T22:46:16.000000Z","readonly":null,"value":null,"_meta":null,"node_path":[{"id":1362,"name":"Hybrid icons","parent_id":null},{"id":2012,"name":"CORN P9978","parent_id":1362},{"id":2259,"name":"PIO25015-007 Corn A4 P9978 MOCKUP.png","parent_id":2012}],"link":"\/asset\/2259.png","readable_size":"1.04 MB","secured":false,"secured_token":"eyJ0eXAiOiJKV1QiLCJhbGciOiJIUzI1NiJ9.eyJzdG9yYWdlcyI6WyJzZWN1cmVfYXNzZXRzIl0sImZpbGUiOjIyNTl9.BP_q2p9HutbQ1tobldTGyIgUB-zN0PN7iIPhalf5nAM","full_path":"1362\/2012\/2259"},"custom_bag_image":null,"graph_image":null,"map_image":null,"new":0,"position":27,"plantheight":null,"type":"corn","title":"P9978","name_id":"P9978","meta_keywords":null,"meta_description":null,"tolerancetrait":null,"producttype":null,"maturity":"Short Season","phenology":null,"blacklegroup":null,"grainoilcontent":null,"plantvigour":null,"cropstandability":null,"shattertolerance":null,"graintestweight":null,"blacklegrating":null,"blacklegresistancegrouping":null,"performertype":null,"crmnumber":null,"crmposition":null,"graintoyieldmaturity":null,"droughttolerance":null,"stalkstrength":null,"rootstrength":null,"staygreen":null,"huskcover":null,"northernleafblight":null,"commonrust":null,"cobrot":null,"harvestdaystart":null,"harvestdayend":null,"silageyieldmaturity":null,"drylandadaptability":null,"wholeplantdigestibility":null,"agronomy_traits":{"grain_yield_for_maturity":"9","husk_cover":"6","plant_height":"8","cob_rot_resistance":"8","dryland_adaptability":"8","northern_leaf_blight":"7","silage_yield_for_maturity":"9","staygreen":"9","whole_plant_digestibility":"7"},"disease_traits":[],"characteristics":[],"recommendations":[],"crm":"99","heading":"P9978 Corn Hybrid","corn_traits":null,"crop":null,"fully_researched_and_proven":null,"improved_fermentation":null,"aerobic_stability":null,"improved_fibre_digestibility":null,"sub_heading":null,"best":null,"intro":"Sets the new standard in grain and silage yield for maturity.","tech_notes":2018,"trait_ratings_disclaimer":null,"usage":"[\"Grain\",\"Silage\"]","purpose":null,"genetic":null,"search":"p9978","keywords":null,"content_id":891,"usage_display":"Grain \/ Silage","bag_image":null},"meta":{"priority":"position","priority_order":"asc","active":1,"created_at":"2024-07-14 17:43:17","updated_at":"2025-07-03 10:46:16"},"schema":{"collectionType":"hybrids","attributes":{"region_id":{"name":"region_id","type":"int","isRequired":false,"keyType":"","length":"10","default":null},"name":{"name":"name","type":"string","isRequired":false,"keyType":"","default":"","length":"255"},"content":{"type":"text"},"content2":{"name":"content2","type":"text","isRequired":false,"keyType":"","default":null},"image":{"name":"image","type":"asset","isRequired":false,"keyType":"","length":"11","default":null,"extensions":["jpeg","jpg","png","svg"],"upload_dir":null,"upload_storage":null},"custom_bag_image":{"name":"custom_bag_image","type":"asset","isRequired":false,"keyType":"","length":"11","default":null,"extensions":["jpeg","jpg","png","svg"],"upload_dir":null,"upload_storage":null},"graph_image":{"name":"graph_image","type":"asset","isRequired":false,"keyType":"","length":"11","default":null,"extensions":["jpeg","jpg","png","svg"],"upload_dir":null,"upload_storage":null},"map_image":{"name":"map_image","type":"int","isRequired":false,"keyType":"","length":"11","default":null},"new":{"name":"new","type":"tinyint","isRequired":false,"keyType":"","length":"1","default":null},"position":{"name":"position","type":"int","isRequired":false,"keyType":"","length":"11","default":null},"plantheight":{"name":"plantheight","type":"int","isRequired":false,"keyType":"","length":"11","default":null},"type":{"name":"type","type":"string","isRequired":false,"keyType":"","default":"","length":"255"},"title":{"name":"title","type":"string","isRequired":false,"keyType":"","default":"","length":"255"},"name_id":{"name":"name_id","type":"string","isRequired":false,"keyType":"","default":"","length":"255"},"meta_keywords":{"name":"meta_keywords","type":"text","isRequired":false,"keyType":"","default":null},"meta_description":{"name":"meta_description","type":"text","isRequired":false,"keyType":"","default":null},"tolerancetrait":{"name":"tolerancetrait","type":"string","isRequired":false,"keyType":"","default":"","length":"255"},"producttype":{"name":"producttype","type":"string","isRequired":false,"keyType":"","default":"","length":"255"},"maturity":{"name":"maturity","type":"string","isRequired":false,"keyType":"","default":"","length":"30"},"phenology":{"name":"phenology","type":"string","isRequired":false,"keyType":"","default":"","length":"30"},"blacklegroup":{"name":"blacklegroup","type":"string","isRequired":false,"keyType":"","default":"","length":"255"},"grainoilcontent":{"name":"grainoilcontent","type":"int","isRequired":false,"keyType":"","length":"11","default":null},"plantvigour":{"name":"plantvigour","type":"int","isRequired":false,"keyType":"","length":"11","default":null},"cropstandability":{"name":"cropstandability","type":"int","isRequired":false,"keyType":"","length":"11","default":null},"shattertolerance":{"name":"shattertolerance","type":"int","isRequired":false,"keyType":"","length":"11","default":null},"graintestweight":{"name":"graintestweight","type":"string","isRequired":false,"keyType":"","default":"","length":"11"},"blacklegrating":{"name":"blacklegrating","type":"string","isRequired":false,"keyType":"","default":"","length":"255"},"blacklegresistancegrouping":{"name":"blacklegresistancegrouping","type":"string","isRequired":false,"keyType":"","default":"","length":"255"},"performertype":{"name":"performertype","type":"enum","isRequired":false,"keyType":"","default":null,"length":"255","values":["Elite","Proven"]},"crmnumber":{"name":"crmnumber","type":"int","isRequired":false,"keyType":"","length":"11","default":null},"crmposition":{"name":"crmposition","type":"string","isRequired":false,"keyType":"","default":"","length":"255"},"graintoyieldmaturity":{"name":"graintoyieldmaturity","type":"string","isRequired":false,"keyType":"","default":"","length":"255"},"droughttolerance":{"name":"droughttolerance","type":"string","isRequired":false,"keyType":"","default":"","length":"255"},"stalkstrength":{"name":"stalkstrength","type":"string","isRequired":false,"keyType":"","default":"","length":"255"},"rootstrength":{"name":"rootstrength","type":"string","isRequired":false,"keyType":"","default":"","length":"255"},"staygreen":{"name":"staygreen","type":"string","isRequired":false,"keyType":"","default":"","length":"255"},"huskcover":{"name":"huskcover","type":"string","isRequired":false,"keyType":"","default":"","length":"255"},"northernleafblight":{"name":"northernleafblight","type":"string","isRequired":false,"keyType":"","default":"","length":"255"},"commonrust":{"name":"commonrust","type":"string","isRequired":false,"keyType":"","default":"","length":"255"},"cobrot":{"name":"cobrot","type":"string","isRequired":false,"keyType":"","default":"","length":"255"},"harvestdaystart":{"name":"harvestdaystart","type":"int","isRequired":false,"keyType":"","length":"11","default":null},"harvestdayend":{"name":"harvestdayend","type":"int","isRequired":false,"keyType":"","length":"11","default":null},"silageyieldmaturity":{"name":"silageyieldmaturity","type":"string","isRequired":false,"keyType":"","default":"","length":"255"},"drylandadaptability":{"name":"drylandadaptability","type":"string","isRequired":false,"keyType":"","default":"","length":"255"},"wholeplantdigestibility":{"name":"wholeplantdigestibility","type":"string","isRequired":false,"keyType":"","default":"","length":"255"},"agronomy_traits":{"name":"agronomy_traits","type":"object","isRequired":false,"keyType":"","default":null,"fields":[]},"disease_traits":{"name":"disease_traits","type":"text","isRequired":false,"keyType":"","default":null},"characteristics":{"name":"characteristics","type":"text","isRequired":false,"keyType":"","default":null},"recommendations":{"name":"recommendations","type":"text","isRequired":false,"keyType":"","default":null},"crm":{"name":"crm","type":"string","isRequired":false,"keyType":"","default":"","length":"255"},"heading":{"name":"heading","type":"string","isRequired":false,"keyType":"","default":"","length":"255"},"corn_traits":{"name":"corn_traits","type":"text","isRequired":false,"keyType":"","default":null},"crop":{"name":"crop","type":"string","isRequired":false,"keyType":"","default":"","length":"255"},"fully_researched_and_proven":{"name":"fully_researched_and_proven","type":"int","isRequired":false,"keyType":"","length":"11","default":null},"improved_fermentation":{"name":"improved_fermentation","type":"int","isRequired":false,"keyType":"","length":"11","default":null},"aerobic_stability":{"name":"aerobic_stability","type":"int","isRequired":false,"keyType":"","length":"11","default":null},"improved_fibre_digestibility":{"name":"improved_fibre_digestibility","type":"int","isRequired":false,"keyType":"","length":"11","default":null},"sub_heading":{"name":"sub_heading","type":"string","isRequired":false,"keyType":"","default":"","length":"255"},"best":{"name":"best","type":"string","isRequired":false,"keyType":"","default":"","length":"255"},"intro":{"name":"intro","type":"string","isRequired":false,"keyType":"","default":"","length":"255"},"tech_notes":{"name":"tech_notes","type":"int","isRequired":false,"keyType":"","length":"11","default":null},"trait_ratings_disclaimer":{"name":"trait_ratings_disclaimer","type":"string","isRequired":false,"keyType":"","default":"","length":"255"},"usage":{"name":"usage","type":"string","isRequired":false,"keyType":"","default":"","length":"511"},"purpose":{"name":"purpose","type":"string","isRequired":false,"keyType":"","default":"","length":"255"},"genetic":{"name":"genetic","type":"string","isRequired":false,"keyType":"","default":"","length":"255"},"search":{"name":"search","type":"text","isRequired":false,"keyType":"MUL","default":null},"keywords":{"name":"keywords","type":"text","isRequired":false,"keyType":"","default":null},"usage_display":{"name":"usage_display","type":"string"},"bag_image":{"name":"bag_image","type":"string"}},"relationships":{"files":{"label":null,"type":"HasMany","class":"HybridFile"},"panels":{"label":null,"type":"HasMany","class":"Panel","refs":"\/panels\/_ref_"},"resource":{"label":null,"type":"HasOne","class":"Resource"},"attached_panels":{"label":null,"type":"BelongsToMany","class":"AttachedPanel","refs":"\/attached_panels\/_ref_"}}},"included":[],"label":"P9978"},{"id":92,"type":"hybrid","attributes":{"id":92,"region_id":null,"name":"P07003 BMR","content":"<p><img src=\"\/asset\/2045.png\" alt=\"P07003 BMR - Segments and CRM.png\" width=\"194\" height=\"113\" \/> <img src=\"\/asset\/2042.png\" alt=\"P07003 BMR - Maturing category.png\" width=\"193\" height=\"117\" \/> <\/p>\n<h2>Solid hybrid with unmatched silage quality.<\/h2>\n<p>P07003 BMR is a new hybrid for the 2025-26 season. The BMR trait increases digestibility with lower lignin to match well-rounded agronomics. Recommended to plant with P9978, and P0937 depending on maturity requirements.<\/p>","content2":"<h3>KEY FEATURES<\/h3>\n<ul>\n<li>Great option for high producing dairies with the ability to feed during peak energy requirements<\/li>\n<li>Produces silage with superior digestibility and energy content<\/li>\n<li>Sound standability with solid root and stalk strength<\/li>\n<li>Consider planting P0937 if cool wet conditions are present around sowing<\/li>\n<\/ul>\n<p><img src=\"\/asset\/2044.png\" alt=\"P07003 BMR - Growing region recommendations.png\" width=\"238\" height=\"424\" \/><\/p>","image":{"id":2260,"parent_id":2040,"name":"PIO25015-007 Corn A4 P07003 BMR MOCKUP.png","description":null,"storage":"assets","size":1055042,"extension":"png","mime_type":"image\/png","width":1731,"height":1487,"keywords":null,"usage":{"corn_hybrids.92":"P07003 BMR"},"created_at":"2025-07-02T22:46:47.000000Z","updated_at":"2025-07-02T22:46:54.000000Z","readonly":null,"value":null,"_meta":null,"node_path":[{"id":1362,"name":"Hybrid icons","parent_id":null},{"id":2040,"name":"CORN P07003 BMR","parent_id":1362},{"id":2260,"name":"PIO25015-007 Corn A4 P07003 BMR MOCKUP.png","parent_id":2040}],"link":"\/asset\/2260.png","readable_size":"1.01 MB","secured":false,"secured_token":"eyJ0eXAiOiJKV1QiLCJhbGciOiJIUzI1NiJ9.eyJzdG9yYWdlcyI6WyJzZWN1cmVfYXNzZXRzIl0sImZpbGUiOjIyNjB9.Enag8iSEBYDCIEIodE1Ud1UWzyBsyYkBpXPMwwdsLh0","full_path":"1362\/2040\/2260"},"custom_bag_image":null,"graph_image":null,"map_image":null,"new":1,"position":28,"plantheight":null,"type":"corn","title":"P07003 BMR","name_id":"p-07003-bmr","meta_keywords":null,"meta_description":null,"tolerancetrait":null,"producttype":null,"maturity":"Mid Season","phenology":null,"blacklegroup":null,"grainoilcontent":null,"plantvigour":null,"cropstandability":null,"shattertolerance":null,"graintestweight":null,"blacklegrating":null,"blacklegresistancegrouping":null,"performertype":null,"crmnumber":null,"crmposition":null,"graintoyieldmaturity":null,"droughttolerance":null,"stalkstrength":null,"rootstrength":null,"staygreen":null,"huskcover":null,"northernleafblight":null,"commonrust":null,"cobrot":null,"harvestdaystart":null,"harvestdayend":null,"silageyieldmaturity":null,"drylandadaptability":null,"wholeplantdigestibility":null,"agronomy_traits":{"grain_yield_for_maturity":null,"husk_cover":"8","plant_height":"8","cob_rot_resistance":null,"dryland_adaptability":"-1","northern_leaf_blight":"6","silage_yield_for_maturity":"7","staygreen":"8","whole_plant_digestibility":"9"},"disease_traits":[],"characteristics":[],"recommendations":[],"crm":"107","heading":"P07003 BMR Corn Hybrid","corn_traits":null,"crop":null,"fully_researched_and_proven":null,"improved_fermentation":null,"aerobic_stability":null,"improved_fibre_digestibility":null,"sub_heading":null,"best":null,"intro":"Solid hybrid with unmatched silage quality.","tech_notes":2046,"trait_ratings_disclaimer":null,"usage":"[\"Silage\"]","purpose":null,"genetic":null,"search":"p07003 bmr","keywords":null,"content_id":1014,"usage_display":"Silage","bag_image":null},"meta":{"priority":"position","priority_order":"asc","active":1,"created_at":"2025-07-01 15:06:10","updated_at":"2025-07-03 10:46:54"},"schema":{"collectionType":"hybrids","attributes":{"region_id":{"name":"region_id","type":"int","isRequired":false,"keyType":"","length":"10","default":null},"name":{"name":"name","type":"string","isRequired":false,"keyType":"","default":"","length":"255"},"content":{"type":"text"},"content2":{"name":"content2","type":"text","isRequired":false,"keyType":"","default":null},"image":{"name":"image","type":"asset","isRequired":false,"keyType":"","length":"11","default":null,"extensions":["jpeg","jpg","png","svg"],"upload_dir":null,"upload_storage":null},"custom_bag_image":{"name":"custom_bag_image","type":"asset","isRequired":false,"keyType":"","length":"11","default":null,"extensions":["jpeg","jpg","png","svg"],"upload_dir":null,"upload_storage":null},"graph_image":{"name":"graph_image","type":"asset","isRequired":false,"keyType":"","length":"11","default":null,"extensions":["jpeg","jpg","png","svg"],"upload_dir":null,"upload_storage":null},"map_image":{"name":"map_image","type":"int","isRequired":false,"keyType":"","length":"11","default":null},"new":{"name":"new","type":"tinyint","isRequired":false,"keyType":"","length":"1","default":null},"position":{"name":"position","type":"int","isRequired":false,"keyType":"","length":"11","default":null},"plantheight":{"name":"plantheight","type":"int","isRequired":false,"keyType":"","length":"11","default":null},"type":{"name":"type","type":"string","isRequired":false,"keyType":"","default":"","length":"255"},"title":{"name":"title","type":"string","isRequired":false,"keyType":"","default":"","length":"255"},"name_id":{"name":"name_id","type":"string","isRequired":false,"keyType":"","default":"","length":"255"},"meta_keywords":{"name":"meta_keywords","type":"text","isRequired":false,"keyType":"","default":null},"meta_description":{"name":"meta_description","type":"text","isRequired":false,"keyType":"","default":null},"tolerancetrait":{"name":"tolerancetrait","type":"string","isRequired":false,"keyType":"","default":"","length":"255"},"producttype":{"name":"producttype","type":"string","isRequired":false,"keyType":"","default":"","length":"255"},"maturity":{"name":"maturity","type":"string","isRequired":false,"keyType":"","default":"","length":"30"},"phenology":{"name":"phenology","type":"string","isRequired":false,"keyType":"","default":"","length":"30"},"blacklegroup":{"name":"blacklegroup","type":"string","isRequired":false,"keyType":"","default":"","length":"255"},"grainoilcontent":{"name":"grainoilcontent","type":"int","isRequired":false,"keyType":"","length":"11","default":null},"plantvigour":{"name":"plantvigour","type":"int","isRequired":false,"keyType":"","length":"11","default":null},"cropstandability":{"name":"cropstandability","type":"int","isRequired":false,"keyType":"","length":"11","default":null},"shattertolerance":{"name":"shattertolerance","type":"int","isRequired":false,"keyType":"","length":"11","default":null},"graintestweight":{"name":"graintestweight","type":"string","isRequired":false,"keyType":"","default":"","length":"11"},"blacklegrating":{"name":"blacklegrating","type":"string","isRequired":false,"keyType":"","default":"","length":"255"},"blacklegresistancegrouping":{"name":"blacklegresistancegrouping","type":"string","isRequired":false,"keyType":"","default":"","length":"255"},"performertype":{"name":"performertype","type":"enum","isRequired":false,"keyType":"","default":null,"length":"255","values":["Elite","Proven"]},"crmnumber":{"name":"crmnumber","type":"int","isRequired":false,"keyType":"","length":"11","default":null},"crmposition":{"name":"crmposition","type":"string","isRequired":false,"keyType":"","default":"","length":"255"},"graintoyieldmaturity":{"name":"graintoyieldmaturity","type":"string","isRequired":false,"keyType":"","default":"","length":"255"},"droughttolerance":{"name":"droughttolerance","type":"string","isRequired":false,"keyType":"","default":"","length":"255"},"stalkstrength":{"name":"stalkstrength","type":"string","isRequired":false,"keyType":"","default":"","length":"255"},"rootstrength":{"name":"rootstrength","type":"string","isRequired":false,"keyType":"","default":"","length":"255"},"staygreen":{"name":"staygreen","type":"string","isRequired":false,"keyType":"","default":"","length":"255"},"huskcover":{"name":"huskcover","type":"string","isRequired":false,"keyType":"","default":"","length":"255"},"northernleafblight":{"name":"northernleafblight","type":"string","isRequired":false,"keyType":"","default":"","length":"255"},"commonrust":{"name":"commonrust","type":"string","isRequired":false,"keyType":"","default":"","length":"255"},"cobrot":{"name":"cobrot","type":"string","isRequired":false,"keyType":"","default":"","length":"255"},"harvestdaystart":{"name":"harvestdaystart","type":"int","isRequired":false,"keyType":"","length":"11","default":null},"harvestdayend":{"name":"harvestdayend","type":"int","isRequired":false,"keyType":"","length":"11","default":null},"silageyieldmaturity":{"name":"silageyieldmaturity","type":"string","isRequired":false,"keyType":"","default":"","length":"255"},"drylandadaptability":{"name":"drylandadaptability","type":"string","isRequired":false,"keyType":"","default":"","length":"255"},"wholeplantdigestibility":{"name":"wholeplantdigestibility","type":"string","isRequired":false,"keyType":"","default":"","length":"255"},"agronomy_traits":{"name":"agronomy_traits","type":"object","isRequired":false,"keyType":"","default":null,"fields":[]},"disease_traits":{"name":"disease_traits","type":"text","isRequired":false,"keyType":"","default":null},"characteristics":{"name":"characteristics","type":"text","isRequired":false,"keyType":"","default":null},"recommendations":{"name":"recommendations","type":"text","isRequired":false,"keyType":"","default":null},"crm":{"name":"crm","type":"string","isRequired":false,"keyType":"","default":"","length":"255"},"heading":{"name":"heading","type":"string","isRequired":false,"keyType":"","default":"","length":"255"},"corn_traits":{"name":"corn_traits","type":"text","isRequired":false,"keyType":"","default":null},"crop":{"name":"crop","type":"string","isRequired":false,"keyType":"","default":"","length":"255"},"fully_researched_and_proven":{"name":"fully_researched_and_proven","type":"int","isRequired":false,"keyType":"","length":"11","default":null},"improved_fermentation":{"name":"improved_fermentation","type":"int","isRequired":false,"keyType":"","length":"11","default":null},"aerobic_stability":{"name":"aerobic_stability","type":"int","isRequired":false,"keyType":"","length":"11","default":null},"improved_fibre_digestibility":{"name":"improved_fibre_digestibility","type":"int","isRequired":false,"keyType":"","length":"11","default":null},"sub_heading":{"name":"sub_heading","type":"string","isRequired":false,"keyType":"","default":"","length":"255"},"best":{"name":"best","type":"string","isRequired":false,"keyType":"","default":"","length":"255"},"intro":{"name":"intro","type":"string","isRequired":false,"keyType":"","default":"","length":"255"},"tech_notes":{"name":"tech_notes","type":"int","isRequired":false,"keyType":"","length":"11","default":null},"trait_ratings_disclaimer":{"name":"trait_ratings_disclaimer","type":"string","isRequired":false,"keyType":"","default":"","length":"255"},"usage":{"name":"usage","type":"string","isRequired":false,"keyType":"","default":"","length":"511"},"purpose":{"name":"purpose","type":"string","isRequired":false,"keyType":"","default":"","length":"255"},"genetic":{"name":"genetic","type":"string","isRequired":false,"keyType":"","default":"","length":"255"},"search":{"name":"search","type":"text","isRequired":false,"keyType":"MUL","default":null},"keywords":{"name":"keywords","type":"text","isRequired":false,"keyType":"","default":null},"usage_display":{"name":"usage_display","type":"string"},"bag_image":{"name":"bag_image","type":"string"}},"relationships":{"files":{"label":null,"type":"HasMany","class":"HybridFile"},"panels":{"label":null,"type":"HasMany","class":"Panel","refs":"\/panels\/_ref_"},"resource":{"label":null,"type":"HasOne","class":"Resource"},"attached_panels":{"label":null,"type":"BelongsToMany","class":"AttachedPanel","refs":"\/attached_panels\/_ref_"}}},"included":[],"label":"P07003 BMR"},{"id":70,"type":"hybrid","attributes":{"id":70,"region_id":null,"name":"P0937","content":"<p><img src=\"\/asset\/2009.png\" alt=\"P0937 - Segments and CRM.png\" width=\"269\" height=\"110\" \/> <img src=\"\/asset\/2008.png\" alt=\"P0937 - Maturity category.png\" width=\"214\" height=\"130\" \/><\/p>\n<h2>Next generation hybrid in a great maturity.<\/h2>\n<p>P0937 corn combines superior dryland, northern leaf blight and rust trait ratings that contribute to season long plant health. It is a widely adapted corn hybrid that delivers a step-change increase in grain yield performance in this maturity.<\/p>\n<p>Our crop scientists use world-leading plant genomics to trial and test all hybrids in Australia before they're released and categorised.<\/p>\n<p>Pioneer Brand Seeds is confident this corn has the features that will appeal to Australian growers, ranging from its high-yield potential to excellent defensive traits for a mid-season corn hybrid.<\/p>\n<p>If you're looking to produce silage from P0937, be sure to use a <a title=\"Pioneer silage supplies\" href=\"\/our-products\/silage-supplies\"><strong>Pioneer inoculant<\/strong><\/a> that suits your needs and preserves the nutrient value.<\/p>\n<p>The ensiling process can cause dry matter and nutrient losses depending on the type and number of acid-producing bacteria in your pasture or crop.<\/p>\n<p>Pioneer® brand \u200bproduct \u200binoculants give you the right bacteria in ideal numbers for a fast, efficient fermentation. They lock-in nutrients and dry matter so your livestock can produce more milk or meat from every tonne of pasture or crop you ensile.<\/p>\n<p>Discuss your unique planting or silage requirements with one of our Pioneer Brand Seeds <a title=\"Contact us\" href=\"\/around-the-seed\/our-team\" target=\"_blank\" rel=\"noopener\"><strong>farm services consultants.<\/strong><\/a> They have the knowledge and tools you need to minimise risk and maximise yield.<\/p>\n<p>Or register with us (below) to stay informed of field days in your region, where you can come along and see the impressive results of this mid-season hybrid corn standing in the paddock.<\/p>","content2":"<h3>KEY FEATURES<\/h3>\n<ul>\n<li>Widely adapted, stable yet high yielding hybrid for silage and grain<\/li>\n<li>Solid Northern Leaf Blight and Rust resistances will be attractive to growers in high-risk situations<\/li>\n<li>Excellent early vigour and emergence when sown early<\/li>\n<\/ul>\n<p><img src=\"\/asset\/2010.png\" alt=\"P0937 - Growing region recommendations.png\" width=\"335\" height=\"472\" \/><\/p>","image":{"id":2261,"parent_id":2005,"name":"PIO25015-007 Corn A4 P0937 MOCKUP.png","description":null,"storage":"assets","size":1085119,"extension":"png","mime_type":"image\/png","width":1731,"height":1487,"keywords":null,"usage":{"corn_hybrids.70":"P0937"},"created_at":"2025-07-02T22:47:42.000000Z","updated_at":"2025-07-02T22:47:50.000000Z","readonly":null,"value":null,"_meta":null,"node_path":[{"id":1362,"name":"Hybrid icons","parent_id":null},{"id":2005,"name":"CORN P0937","parent_id":1362},{"id":2261,"name":"PIO25015-007 Corn A4 P0937 MOCKUP.png","parent_id":2005}],"link":"\/asset\/2261.png","readable_size":"1.03 MB","secured":false,"secured_token":"eyJ0eXAiOiJKV1QiLCJhbGciOiJIUzI1NiJ9.eyJzdG9yYWdlcyI6WyJzZWN1cmVfYXNzZXRzIl0sImZpbGUiOjIyNjF9.Et5vjZKxNbcGktvKyiNU9ynhqjbmJ598EKt_WODXJ6E","full_path":"1362\/2005\/2261"},"custom_bag_image":null,"graph_image":null,"map_image":null,"new":0,"position":29,"plantheight":null,"type":"corn","title":"P0937","name_id":"p0937","meta_keywords":"vigour, corn, low, ear, erect, standability, husk, seed, Australian, dryland, irrigated","meta_description":"Hybrid corn with early growth and low ear placement results in high-yield and improved standability. Learn more about this type of corn, with its sound husk cover and sturdy stalks.","tolerancetrait":null,"producttype":null,"maturity":"Mid Season","phenology":null,"blacklegroup":null,"grainoilcontent":null,"plantvigour":null,"cropstandability":null,"shattertolerance":null,"graintestweight":null,"blacklegrating":null,"blacklegresistancegrouping":null,"performertype":null,"crmnumber":null,"crmposition":null,"graintoyieldmaturity":null,"droughttolerance":null,"stalkstrength":null,"rootstrength":null,"staygreen":null,"huskcover":null,"northernleafblight":null,"commonrust":null,"cobrot":null,"harvestdaystart":null,"harvestdayend":null,"silageyieldmaturity":null,"drylandadaptability":null,"wholeplantdigestibility":null,"agronomy_traits":{"grain_yield_for_maturity":"9","husk_cover":"5","plant_height":"8","cob_rot_resistance":"8","dryland_adaptability":"7","northern_leaf_blight":"7","silage_yield_for_maturity":"8","staygreen":"7","whole_plant_digestibility":"8"},"disease_traits":[],"characteristics":[],"recommendations":[],"crm":"109","heading":"P0937 Corn Hybrid","corn_traits":null,"crop":null,"fully_researched_and_proven":null,"improved_fermentation":null,"aerobic_stability":null,"improved_fibre_digestibility":null,"sub_heading":null,"best":null,"intro":"Next generation hybrid in a great maturity.","tech_notes":2011,"trait_ratings_disclaimer":null,"usage":"[\"Dual Purpose\"]","purpose":null,"genetic":null,"search":"p0937","keywords":null,"content_id":553,"usage_display":"Dual Purpose","bag_image":null},"meta":{"priority":"position","priority_order":"asc","active":1,"created_at":"2022-07-07 18:25:09","updated_at":"2025-07-03 10:47:50"},"schema":{"collectionType":"hybrids","attributes":{"region_id":{"name":"region_id","type":"int","isRequired":false,"keyType":"","length":"10","default":null},"name":{"name":"name","type":"string","isRequired":false,"keyType":"","default":"","length":"255"},"content":{"type":"text"},"content2":{"name":"content2","type":"text","isRequired":false,"keyType":"","default":null},"image":{"name":"image","type":"asset","isRequired":false,"keyType":"","length":"11","default":null,"extensions":["jpeg","jpg","png","svg"],"upload_dir":null,"upload_storage":null},"custom_bag_image":{"name":"custom_bag_image","type":"asset","isRequired":false,"keyType":"","length":"11","default":null,"extensions":["jpeg","jpg","png","svg"],"upload_dir":null,"upload_storage":null},"graph_image":{"name":"graph_image","type":"asset","isRequired":false,"keyType":"","length":"11","default":null,"extensions":["jpeg","jpg","png","svg"],"upload_dir":null,"upload_storage":null},"map_image":{"name":"map_image","type":"int","isRequired":false,"keyType":"","length":"11","default":null},"new":{"name":"new","type":"tinyint","isRequired":false,"keyType":"","length":"1","default":null},"position":{"name":"position","type":"int","isRequired":false,"keyType":"","length":"11","default":null},"plantheight":{"name":"plantheight","type":"int","isRequired":false,"keyType":"","length":"11","default":null},"type":{"name":"type","type":"string","isRequired":false,"keyType":"","default":"","length":"255"},"title":{"name":"title","type":"string","isRequired":false,"keyType":"","default":"","length":"255"},"name_id":{"name":"name_id","type":"string","isRequired":false,"keyType":"","default":"","length":"255"},"meta_keywords":{"name":"meta_keywords","type":"text","isRequired":false,"keyType":"","default":null},"meta_description":{"name":"meta_description","type":"text","isRequired":false,"keyType":"","default":null},"tolerancetrait":{"name":"tolerancetrait","type":"string","isRequired":false,"keyType":"","default":"","length":"255"},"producttype":{"name":"producttype","type":"string","isRequired":false,"keyType":"","default":"","length":"255"},"maturity":{"name":"maturity","type":"string","isRequired":false,"keyType":"","default":"","length":"30"},"phenology":{"name":"phenology","type":"string","isRequired":false,"keyType":"","default":"","length":"30"},"blacklegroup":{"name":"blacklegroup","type":"string","isRequired":false,"keyType":"","default":"","length":"255"},"grainoilcontent":{"name":"grainoilcontent","type":"int","isRequired":false,"keyType":"","length":"11","default":null},"plantvigour":{"name":"plantvigour","type":"int","isRequired":false,"keyType":"","length":"11","default":null},"cropstandability":{"name":"cropstandability","type":"int","isRequired":false,"keyType":"","length":"11","default":null},"shattertolerance":{"name":"shattertolerance","type":"int","isRequired":false,"keyType":"","length":"11","default":null},"graintestweight":{"name":"graintestweight","type":"string","isRequired":false,"keyType":"","default":"","length":"11"},"blacklegrating":{"name":"blacklegrating","type":"string","isRequired":false,"keyType":"","default":"","length":"255"},"blacklegresistancegrouping":{"name":"blacklegresistancegrouping","type":"string","isRequired":false,"keyType":"","default":"","length":"255"},"performertype":{"name":"performertype","type":"enum","isRequired":false,"keyType":"","default":null,"length":"255","values":["Elite","Proven"]},"crmnumber":{"name":"crmnumber","type":"int","isRequired":false,"keyType":"","length":"11","default":null},"crmposition":{"name":"crmposition","type":"string","isRequired":false,"keyType":"","default":"","length":"255"},"graintoyieldmaturity":{"name":"graintoyieldmaturity","type":"string","isRequired":false,"keyType":"","default":"","length":"255"},"droughttolerance":{"name":"droughttolerance","type":"string","isRequired":false,"keyType":"","default":"","length":"255"},"stalkstrength":{"name":"stalkstrength","type":"string","isRequired":false,"keyType":"","default":"","length":"255"},"rootstrength":{"name":"rootstrength","type":"string","isRequired":false,"keyType":"","default":"","length":"255"},"staygreen":{"name":"staygreen","type":"string","isRequired":false,"keyType":"","default":"","length":"255"},"huskcover":{"name":"huskcover","type":"string","isRequired":false,"keyType":"","default":"","length":"255"},"northernleafblight":{"name":"northernleafblight","type":"string","isRequired":false,"keyType":"","default":"","length":"255"},"commonrust":{"name":"commonrust","type":"string","isRequired":false,"keyType":"","default":"","length":"255"},"cobrot":{"name":"cobrot","type":"string","isRequired":false,"keyType":"","default":"","length":"255"},"harvestdaystart":{"name":"harvestdaystart","type":"int","isRequired":false,"keyType":"","length":"11","default":null},"harvestdayend":{"name":"harvestdayend","type":"int","isRequired":false,"keyType":"","length":"11","default":null},"silageyieldmaturity":{"name":"silageyieldmaturity","type":"string","isRequired":false,"keyType":"","default":"","length":"255"},"drylandadaptability":{"name":"drylandadaptability","type":"string","isRequired":false,"keyType":"","default":"","length":"255"},"wholeplantdigestibility":{"name":"wholeplantdigestibility","type":"string","isRequired":false,"keyType":"","default":"","length":"255"},"agronomy_traits":{"name":"agronomy_traits","type":"object","isRequired":false,"keyType":"","default":null,"fields":[]},"disease_traits":{"name":"disease_traits","type":"text","isRequired":false,"keyType":"","default":null},"characteristics":{"name":"characteristics","type":"text","isRequired":false,"keyType":"","default":null},"recommendations":{"name":"recommendations","type":"text","isRequired":false,"keyType":"","default":null},"crm":{"name":"crm","type":"string","isRequired":false,"keyType":"","default":"","length":"255"},"heading":{"name":"heading","type":"string","isRequired":false,"keyType":"","default":"","length":"255"},"corn_traits":{"name":"corn_traits","type":"text","isRequired":false,"keyType":"","default":null},"crop":{"name":"crop","type":"string","isRequired":false,"keyType":"","default":"","length":"255"},"fully_researched_and_proven":{"name":"fully_researched_and_proven","type":"int","isRequired":false,"keyType":"","length":"11","default":null},"improved_fermentation":{"name":"improved_fermentation","type":"int","isRequired":false,"keyType":"","length":"11","default":null},"aerobic_stability":{"name":"aerobic_stability","type":"int","isRequired":false,"keyType":"","length":"11","default":null},"improved_fibre_digestibility":{"name":"improved_fibre_digestibility","type":"int","isRequired":false,"keyType":"","length":"11","default":null},"sub_heading":{"name":"sub_heading","type":"string","isRequired":false,"keyType":"","default":"","length":"255"},"best":{"name":"best","type":"string","isRequired":false,"keyType":"","default":"","length":"255"},"intro":{"name":"intro","type":"string","isRequired":false,"keyType":"","default":"","length":"255"},"tech_notes":{"name":"tech_notes","type":"int","isRequired":false,"keyType":"","length":"11","default":null},"trait_ratings_disclaimer":{"name":"trait_ratings_disclaimer","type":"string","isRequired":false,"keyType":"","default":"","length":"255"},"usage":{"name":"usage","type":"string","isRequired":false,"keyType":"","default":"","length":"511"},"purpose":{"name":"purpose","type":"string","isRequired":false,"keyType":"","default":"","length":"255"},"genetic":{"name":"genetic","type":"string","isRequired":false,"keyType":"","default":"","length":"255"},"search":{"name":"search","type":"text","isRequired":false,"keyType":"MUL","default":null},"keywords":{"name":"keywords","type":"text","isRequired":false,"keyType":"","default":null},"usage_display":{"name":"usage_display","type":"string"},"bag_image":{"name":"bag_image","type":"string"}},"relationships":{"files":{"label":null,"type":"HasMany","class":"HybridFile"},"panels":{"label":null,"type":"HasMany","class":"Panel","refs":"\/panels\/_ref_"},"resource":{"label":null,"type":"HasOne","class":"Resource"},"attached_panels":{"label":null,"type":"BelongsToMany","class":"AttachedPanel","refs":"\/attached_panels\/_ref_"}}},"included":[],"label":"P0937"},{"id":93,"type":"hybrid","attributes":{"id":93,"region_id":null,"name":"P13063 IT","content":"<p><img src=\"\/asset\/2052.png\" alt=\"P13063 IT - Segments and CRM.png\" width=\"255\" height=\"104\" \/> <img src=\"\/asset\/2048.png\" alt=\"P13063 IT - Maturity category.png\" width=\"176\" height=\"108\" \/><\/p>\n<h2>Newest genetics packed with yield, agronomics and herbicide tolerance.<\/h2>\n<p>P13063 IT is a great mid-maturing option for growers chasing reliability and flexibility. Replaces P1481 in the hybrid lineup. This new hybrid is a moderately tall hybrid with excellent standability.<\/p>","content2":"<h3>KEY FEATURES<\/h3>\n<ul>\n<li>Well suited to most environments with excellent yield for maturity and well-rounded agronomics<\/li>\n<li>Moderate staygreen helps get to harvest quickly in southern environments with a shorter season<\/li>\n<li>Imidazolinone herbicide tolerance for in crop management of difficult summer grasses<\/li>\n<li>Competitive silage yields with P1315 IT with greater standability<\/li>\n<\/ul>\n<p><img src=\"\/asset\/2050.png\" alt=\"P13063 IT - Growing region recommendations.png\" width=\"310\" height=\"491\" \/><\/p>","image":{"id":2255,"parent_id":2047,"name":"PIO25015-007 Corn A4 P13063 IT MOCKUP.png","description":null,"storage":"assets","size":1146600,"extension":"png","mime_type":"image\/png","width":1731,"height":1487,"keywords":null,"usage":{"corn_hybrids.93":"P13063 IT"},"created_at":"2025-07-02T05:38:54.000000Z","updated_at":"2025-07-02T05:39:05.000000Z","readonly":null,"value":null,"_meta":null,"node_path":[{"id":1362,"name":"Hybrid icons","parent_id":null},{"id":2047,"name":"CORN P13063 IT","parent_id":1362},{"id":2255,"name":"PIO25015-007 Corn A4 P13063 IT MOCKUP.png","parent_id":2047}],"link":"\/asset\/2255.png","readable_size":"1.09 MB","secured":false,"secured_token":"eyJ0eXAiOiJKV1QiLCJhbGciOiJIUzI1NiJ9.eyJzdG9yYWdlcyI6WyJzZWN1cmVfYXNzZXRzIl0sImZpbGUiOjIyNTV9.bZoBeeDJRCRBYXeXUH1eKQ0QPC-O-vpUf9aLEetVYbA","full_path":"1362\/2047\/2255"},"custom_bag_image":null,"graph_image":null,"map_image":null,"new":1,"position":30,"plantheight":null,"type":"corn","title":"P3063 IT","name_id":"p-3063-it","meta_keywords":null,"meta_description":null,"tolerancetrait":null,"producttype":null,"maturity":"Mid Season","phenology":null,"blacklegroup":null,"grainoilcontent":null,"plantvigour":null,"cropstandability":null,"shattertolerance":null,"graintestweight":null,"blacklegrating":null,"blacklegresistancegrouping":null,"performertype":null,"crmnumber":null,"crmposition":null,"graintoyieldmaturity":null,"droughttolerance":null,"stalkstrength":null,"rootstrength":null,"staygreen":null,"huskcover":null,"northernleafblight":null,"commonrust":null,"cobrot":null,"harvestdaystart":null,"harvestdayend":null,"silageyieldmaturity":null,"drylandadaptability":null,"wholeplantdigestibility":null,"agronomy_traits":{"grain_yield_for_maturity":"9","husk_cover":"7.5","plant_height":"8","cob_rot_resistance":"8","dryland_adaptability":"5","northern_leaf_blight":"8","silage_yield_for_maturity":"8","staygreen":"5","whole_plant_digestibility":"8"},"disease_traits":[],"characteristics":[],"recommendations":[],"crm":"113","heading":"P13063 IT Corn Hybrid","corn_traits":null,"crop":null,"fully_researched_and_proven":null,"improved_fermentation":null,"aerobic_stability":null,"improved_fibre_digestibility":null,"sub_heading":null,"best":null,"intro":"Newest genetics packed with yield, agronomics and herbicide tolerance.","tech_notes":2053,"trait_ratings_disclaimer":null,"usage":"[\"Grain\",\"Silage\"]","purpose":null,"genetic":null,"search":"p13063 kw_it","keywords":null,"content_id":1015,"usage_display":"Grain \/ Silage","bag_image":null},"meta":{"priority":"position","priority_order":"asc","active":1,"created_at":"2025-07-01 15:10:40","updated_at":"2025-07-02 17:39:05"},"schema":{"collectionType":"hybrids","attributes":{"region_id":{"name":"region_id","type":"int","isRequired":false,"keyType":"","length":"10","default":null},"name":{"name":"name","type":"string","isRequired":false,"keyType":"","default":"","length":"255"},"content":{"type":"text"},"content2":{"name":"content2","type":"text","isRequired":false,"keyType":"","default":null},"image":{"name":"image","type":"asset","isRequired":false,"keyType":"","length":"11","default":null,"extensions":["jpeg","jpg","png","svg"],"upload_dir":null,"upload_storage":null},"custom_bag_image":{"name":"custom_bag_image","type":"asset","isRequired":false,"keyType":"","length":"11","default":null,"extensions":["jpeg","jpg","png","svg"],"upload_dir":null,"upload_storage":null},"graph_image":{"name":"graph_image","type":"asset","isRequired":false,"keyType":"","length":"11","default":null,"extensions":["jpeg","jpg","png","svg"],"upload_dir":null,"upload_storage":null},"map_image":{"name":"map_image","type":"int","isRequired":false,"keyType":"","length":"11","default":null},"new":{"name":"new","type":"tinyint","isRequired":false,"keyType":"","length":"1","default":null},"position":{"name":"position","type":"int","isRequired":false,"keyType":"","length":"11","default":null},"plantheight":{"name":"plantheight","type":"int","isRequired":false,"keyType":"","length":"11","default":null},"type":{"name":"type","type":"string","isRequired":false,"keyType":"","default":"","length":"255"},"title":{"name":"title","type":"string","isRequired":false,"keyType":"","default":"","length":"255"},"name_id":{"name":"name_id","type":"string","isRequired":false,"keyType":"","default":"","length":"255"},"meta_keywords":{"name":"meta_keywords","type":"text","isRequired":false,"keyType":"","default":null},"meta_description":{"name":"meta_description","type":"text","isRequired":false,"keyType":"","default":null},"tolerancetrait":{"name":"tolerancetrait","type":"string","isRequired":false,"keyType":"","default":"","length":"255"},"producttype":{"name":"producttype","type":"string","isRequired":false,"keyType":"","default":"","length":"255"},"maturity":{"name":"maturity","type":"string","isRequired":false,"keyType":"","default":"","length":"30"},"phenology":{"name":"phenology","type":"string","isRequired":false,"keyType":"","default":"","length":"30"},"blacklegroup":{"name":"blacklegroup","type":"string","isRequired":false,"keyType":"","default":"","length":"255"},"grainoilcontent":{"name":"grainoilcontent","type":"int","isRequired":false,"keyType":"","length":"11","default":null},"plantvigour":{"name":"plantvigour","type":"int","isRequired":false,"keyType":"","length":"11","default":null},"cropstandability":{"name":"cropstandability","type":"int","isRequired":false,"keyType":"","length":"11","default":null},"shattertolerance":{"name":"shattertolerance","type":"int","isRequired":false,"keyType":"","length":"11","default":null},"graintestweight":{"name":"graintestweight","type":"string","isRequired":false,"keyType":"","default":"","length":"11"},"blacklegrating":{"name":"blacklegrating","type":"string","isRequired":false,"keyType":"","default":"","length":"255"},"blacklegresistancegrouping":{"name":"blacklegresistancegrouping","type":"string","isRequired":false,"keyType":"","default":"","length":"255"},"performertype":{"name":"performertype","type":"enum","isRequired":false,"keyType":"","default":null,"length":"255","values":["Elite","Proven"]},"crmnumber":{"name":"crmnumber","type":"int","isRequired":false,"keyType":"","length":"11","default":null},"crmposition":{"name":"crmposition","type":"string","isRequired":false,"keyType":"","default":"","length":"255"},"graintoyieldmaturity":{"name":"graintoyieldmaturity","type":"string","isRequired":false,"keyType":"","default":"","length":"255"},"droughttolerance":{"name":"droughttolerance","type":"string","isRequired":false,"keyType":"","default":"","length":"255"},"stalkstrength":{"name":"stalkstrength","type":"string","isRequired":false,"keyType":"","default":"","length":"255"},"rootstrength":{"name":"rootstrength","type":"string","isRequired":false,"keyType":"","default":"","length":"255"},"staygreen":{"name":"staygreen","type":"string","isRequired":false,"keyType":"","default":"","length":"255"},"huskcover":{"name":"huskcover","type":"string","isRequired":false,"keyType":"","default":"","length":"255"},"northernleafblight":{"name":"northernleafblight","type":"string","isRequired":false,"keyType":"","default":"","length":"255"},"commonrust":{"name":"commonrust","type":"string","isRequired":false,"keyType":"","default":"","length":"255"},"cobrot":{"name":"cobrot","type":"string","isRequired":false,"keyType":"","default":"","length":"255"},"harvestdaystart":{"name":"harvestdaystart","type":"int","isRequired":false,"keyType":"","length":"11","default":null},"harvestdayend":{"name":"harvestdayend","type":"int","isRequired":false,"keyType":"","length":"11","default":null},"silageyieldmaturity":{"name":"silageyieldmaturity","type":"string","isRequired":false,"keyType":"","default":"","length":"255"},"drylandadaptability":{"name":"drylandadaptability","type":"string","isRequired":false,"keyType":"","default":"","length":"255"},"wholeplantdigestibility":{"name":"wholeplantdigestibility","type":"string","isRequired":false,"keyType":"","default":"","length":"255"},"agronomy_traits":{"name":"agronomy_traits","type":"object","isRequired":false,"keyType":"","default":null,"fields":[]},"disease_traits":{"name":"disease_traits","type":"text","isRequired":false,"keyType":"","default":null},"characteristics":{"name":"characteristics","type":"text","isRequired":false,"keyType":"","default":null},"recommendations":{"name":"recommendations","type":"text","isRequired":false,"keyType":"","default":null},"crm":{"name":"crm","type":"string","isRequired":false,"keyType":"","default":"","length":"255"},"heading":{"name":"heading","type":"string","isRequired":false,"keyType":"","default":"","length":"255"},"corn_traits":{"name":"corn_traits","type":"text","isRequired":false,"keyType":"","default":null},"crop":{"name":"crop","type":"string","isRequired":false,"keyType":"","default":"","length":"255"},"fully_researched_and_proven":{"name":"fully_researched_and_proven","type":"int","isRequired":false,"keyType":"","length":"11","default":null},"improved_fermentation":{"name":"improved_fermentation","type":"int","isRequired":false,"keyType":"","length":"11","default":null},"aerobic_stability":{"name":"aerobic_stability","type":"int","isRequired":false,"keyType":"","length":"11","default":null},"improved_fibre_digestibility":{"name":"improved_fibre_digestibility","type":"int","isRequired":false,"keyType":"","length":"11","default":null},"sub_heading":{"name":"sub_heading","type":"string","isRequired":false,"keyType":"","default":"","length":"255"},"best":{"name":"best","type":"string","isRequired":false,"keyType":"","default":"","length":"255"},"intro":{"name":"intro","type":"string","isRequired":false,"keyType":"","default":"","length":"255"},"tech_notes":{"name":"tech_notes","type":"int","isRequired":false,"keyType":"","length":"11","default":null},"trait_ratings_disclaimer":{"name":"trait_ratings_disclaimer","type":"string","isRequired":false,"keyType":"","default":"","length":"255"},"usage":{"name":"usage","type":"string","isRequired":false,"keyType":"","default":"","length":"511"},"purpose":{"name":"purpose","type":"string","isRequired":false,"keyType":"","default":"","length":"255"},"genetic":{"name":"genetic","type":"string","isRequired":false,"keyType":"","default":"","length":"255"},"search":{"name":"search","type":"text","isRequired":false,"keyType":"MUL","default":null},"keywords":{"name":"keywords","type":"text","isRequired":false,"keyType":"","default":null},"usage_display":{"name":"usage_display","type":"string"},"bag_image":{"name":"bag_image","type":"string"}},"relationships":{"files":{"label":null,"type":"HasMany","class":"HybridFile"},"panels":{"label":null,"type":"HasMany","class":"Panel","refs":"\/panels\/_ref_"},"resource":{"label":null,"type":"HasOne","class":"Resource"},"attached_panels":{"label":null,"type":"BelongsToMany","class":"AttachedPanel","refs":"\/attached_panels\/_ref_"}}},"included":[],"label":"P13063 IT"},{"id":24,"type":"hybrid","attributes":{"id":24,"region_id":null,"name":"P1315 IT","content":"<p><img src=\"\/asset\/2002.png\" alt=\"P1315 IT - Segments and CRM.png\" width=\"257\" height=\"105\" \/> <img src=\"\/asset\/2000.png\" alt=\"P1315 IT - Maturity catergory.png\" width=\"176\" height=\"107\" \/> <\/p>\n<h2>Tall, trusted and consistent.<\/h2>\n<p>This high yielding mid-season multi-use corn hybrid is primarily suited to the processing market for human consumption. P1315-IT has the added benefit of imidazolinone tolerance for better weed control, and is also suitable for feed grain or silage uses.<\/p>\n<p>P1315-IT sets a new standard for mid-season processing corn hybrids as it's a truly versatile corn variety.<\/p>\n<p>When producing silage from P1315-IT hybrid corn, be sure to choose a <a title=\"Pioneer silage supplies link\" href=\"\/our-products\/silage-supplies\" target=\"_blank\" rel=\"noopener\"><strong>Pioneer inoculant <\/strong><\/a>that suits your needs and preserves the nutrient value of this top performer.<\/p>\n<p>The ensiling process can cause dry matter and nutrient losses depending on the type and number of acid-producing bacteria in your pasture or crop.<\/p>\n<p>Pioneer® brand \u200bproduct \u200binoculants ensure you have the right bacteria in right numbers for a fast, efficient fermentation. They lock-in nutrients and dry matter so your livestock can produce more milk or meat from every tonne of pasture or crop you ensile.<\/p>\n<p>Talk to your local Pioneer Brand Seeds <a title=\"Contact us page\" href=\"\/contact-us\" target=\"_blank\" rel=\"noopener\"><strong>farm services consultant<\/strong> <\/a>about your cropping or silage options.<\/p>\n<p>Or register with us (below) to stay informed of field days in your region, where you can see for yourself the excellent results you can expect for this mid-season hybrid.<\/p>\n<p> <\/p>","content2":"<h3>KEY FEATURES<\/h3>\n<ul>\n<li>Excellent staygreen for maximum silage quality<\/li>\n<li>Very high silage yields, delivers under irrigation and in dryland conditions<\/li>\n<li>Imidazolinone herbicide tolerance for in crop management of difficult summer grasses<\/li>\n<\/ul>\n<p><img src=\"\/asset\/2001.png\" alt=\"P1315 IT - Growing region recommendations.png\" width=\"301\" height=\"477\" \/><\/p>","image":{"id":2262,"parent_id":1998,"name":"PIO25015-007 Corn A4 P1315 IT MOCKUP.png","description":null,"storage":"assets","size":1161996,"extension":"png","mime_type":"image\/png","width":1731,"height":1487,"keywords":null,"usage":{"corn_hybrids.24":"P1315 IT"},"created_at":"2025-07-02T22:48:39.000000Z","updated_at":"2025-07-02T22:48:46.000000Z","readonly":null,"value":null,"_meta":null,"node_path":[{"id":1362,"name":"Hybrid icons","parent_id":null},{"id":1998,"name":"CORN P1315 IT","parent_id":1362},{"id":2262,"name":"PIO25015-007 Corn A4 P1315 IT MOCKUP.png","parent_id":1998}],"link":"\/asset\/2262.png","readable_size":"1.11 MB","secured":false,"secured_token":"eyJ0eXAiOiJKV1QiLCJhbGciOiJIUzI1NiJ9.eyJzdG9yYWdlcyI6WyJzZWN1cmVfYXNzZXRzIl0sImZpbGUiOjIyNjJ9.Py16TfR0nB4iuxubCJmyxl56M9_8HXvLDNGENpKWCHA","full_path":"1362\/1998\/2262"},"custom_bag_image":null,"graph_image":null,"map_image":null,"new":0,"position":31,"plantheight":null,"type":"corn","title":"P1315-IT","name_id":"p1315-it","meta_keywords":"corn, hybrid, vigour, strength, tolerance, Imidazolinone, dryland, irrigated, seed, Australian","meta_description":"Looking for a high-yielding hybrid corn that is suitable for processing, feed grain, or silage? Find out which hybrid has excellent vigor, strength and is resistant to Fusarium and Imidazolinone.","tolerancetrait":null,"producttype":null,"maturity":"Mid Season","phenology":null,"blacklegroup":null,"grainoilcontent":null,"plantvigour":null,"cropstandability":null,"shattertolerance":null,"graintestweight":null,"blacklegrating":null,"blacklegresistancegrouping":null,"performertype":null,"crmnumber":null,"crmposition":null,"graintoyieldmaturity":null,"droughttolerance":null,"stalkstrength":null,"rootstrength":null,"staygreen":null,"huskcover":null,"northernleafblight":null,"commonrust":null,"cobrot":null,"harvestdaystart":null,"harvestdayend":null,"silageyieldmaturity":null,"drylandadaptability":null,"wholeplantdigestibility":null,"agronomy_traits":{"grain_yield_for_maturity":"7","husk_cover":"8","plant_height":"9","cob_rot_resistance":"8","dryland_adaptability":"8","northern_leaf_blight":"7","silage_yield_for_maturity":"9","staygreen":"9","whole_plant_digestibility":"7"},"disease_traits":[],"characteristics":[],"recommendations":[],"crm":"113","heading":"P1315-IT Corn Hybrid","corn_traits":null,"crop":null,"fully_researched_and_proven":null,"improved_fermentation":null,"aerobic_stability":null,"improved_fibre_digestibility":null,"sub_heading":null,"best":null,"intro":"Tall, trusted and consistent.","tech_notes":2004,"trait_ratings_disclaimer":null,"usage":"[\"Dual Purpose\",\"Grain\",\"Silage\"]","purpose":null,"genetic":null,"search":"p1315 kw_it","keywords":null,"content_id":352,"usage_display":"Dual Purpose \/ Grain \/ Silage","bag_image":null},"meta":{"priority":"position","priority_order":"asc","active":1,"created_at":"2021-03-11 17:42:10","updated_at":"2025-07-03 10:48:46"},"schema":{"collectionType":"hybrids","attributes":{"region_id":{"name":"region_id","type":"int","isRequired":false,"keyType":"","length":"10","default":null},"name":{"name":"name","type":"string","isRequired":false,"keyType":"","default":"","length":"255"},"content":{"type":"text"},"content2":{"name":"content2","type":"text","isRequired":false,"keyType":"","default":null},"image":{"name":"image","type":"asset","isRequired":false,"keyType":"","length":"11","default":null,"extensions":["jpeg","jpg","png","svg"],"upload_dir":null,"upload_storage":null},"custom_bag_image":{"name":"custom_bag_image","type":"asset","isRequired":false,"keyType":"","length":"11","default":null,"extensions":["jpeg","jpg","png","svg"],"upload_dir":null,"upload_storage":null},"graph_image":{"name":"graph_image","type":"asset","isRequired":false,"keyType":"","length":"11","default":null,"extensions":["jpeg","jpg","png","svg"],"upload_dir":null,"upload_storage":null},"map_image":{"name":"map_image","type":"int","isRequired":false,"keyType":"","length":"11","default":null},"new":{"name":"new","type":"tinyint","isRequired":false,"keyType":"","length":"1","default":null},"position":{"name":"position","type":"int","isRequired":false,"keyType":"","length":"11","default":null},"plantheight":{"name":"plantheight","type":"int","isRequired":false,"keyType":"","length":"11","default":null},"type":{"name":"type","type":"string","isRequired":false,"keyType":"","default":"","length":"255"},"title":{"name":"title","type":"string","isRequired":false,"keyType":"","default":"","length":"255"},"name_id":{"name":"name_id","type":"string","isRequired":false,"keyType":"","default":"","length":"255"},"meta_keywords":{"name":"meta_keywords","type":"text","isRequired":false,"keyType":"","default":null},"meta_description":{"name":"meta_description","type":"text","isRequired":false,"keyType":"","default":null},"tolerancetrait":{"name":"tolerancetrait","type":"string","isRequired":false,"keyType":"","default":"","length":"255"},"producttype":{"name":"producttype","type":"string","isRequired":false,"keyType":"","default":"","length":"255"},"maturity":{"name":"maturity","type":"string","isRequired":false,"keyType":"","default":"","length":"30"},"phenology":{"name":"phenology","type":"string","isRequired":false,"keyType":"","default":"","length":"30"},"blacklegroup":{"name":"blacklegroup","type":"string","isRequired":false,"keyType":"","default":"","length":"255"},"grainoilcontent":{"name":"grainoilcontent","type":"int","isRequired":false,"keyType":"","length":"11","default":null},"plantvigour":{"name":"plantvigour","type":"int","isRequired":false,"keyType":"","length":"11","default":null},"cropstandability":{"name":"cropstandability","type":"int","isRequired":false,"keyType":"","length":"11","default":null},"shattertolerance":{"name":"shattertolerance","type":"int","isRequired":false,"keyType":"","length":"11","default":null},"graintestweight":{"name":"graintestweight","type":"string","isRequired":false,"keyType":"","default":"","length":"11"},"blacklegrating":{"name":"blacklegrating","type":"string","isRequired":false,"keyType":"","default":"","length":"255"},"blacklegresistancegrouping":{"name":"blacklegresistancegrouping","type":"string","isRequired":false,"keyType":"","default":"","length":"255"},"performertype":{"name":"performertype","type":"enum","isRequired":false,"keyType":"","default":null,"length":"255","values":["Elite","Proven"]},"crmnumber":{"name":"crmnumber","type":"int","isRequired":false,"keyType":"","length":"11","default":null},"crmposition":{"name":"crmposition","type":"string","isRequired":false,"keyType":"","default":"","length":"255"},"graintoyieldmaturity":{"name":"graintoyieldmaturity","type":"string","isRequired":false,"keyType":"","default":"","length":"255"},"droughttolerance":{"name":"droughttolerance","type":"string","isRequired":false,"keyType":"","default":"","length":"255"},"stalkstrength":{"name":"stalkstrength","type":"string","isRequired":false,"keyType":"","default":"","length":"255"},"rootstrength":{"name":"rootstrength","type":"string","isRequired":false,"keyType":"","default":"","length":"255"},"staygreen":{"name":"staygreen","type":"string","isRequired":false,"keyType":"","default":"","length":"255"},"huskcover":{"name":"huskcover","type":"string","isRequired":false,"keyType":"","default":"","length":"255"},"northernleafblight":{"name":"northernleafblight","type":"string","isRequired":false,"keyType":"","default":"","length":"255"},"commonrust":{"name":"commonrust","type":"string","isRequired":false,"keyType":"","default":"","length":"255"},"cobrot":{"name":"cobrot","type":"string","isRequired":false,"keyType":"","default":"","length":"255"},"harvestdaystart":{"name":"harvestdaystart","type":"int","isRequired":false,"keyType":"","length":"11","default":null},"harvestdayend":{"name":"harvestdayend","type":"int","isRequired":false,"keyType":"","length":"11","default":null},"silageyieldmaturity":{"name":"silageyieldmaturity","type":"string","isRequired":false,"keyType":"","default":"","length":"255"},"drylandadaptability":{"name":"drylandadaptability","type":"string","isRequired":false,"keyType":"","default":"","length":"255"},"wholeplantdigestibility":{"name":"wholeplantdigestibility","type":"string","isRequired":false,"keyType":"","default":"","length":"255"},"agronomy_traits":{"name":"agronomy_traits","type":"object","isRequired":false,"keyType":"","default":null,"fields":[]},"disease_traits":{"name":"disease_traits","type":"text","isRequired":false,"keyType":"","default":null},"characteristics":{"name":"characteristics","type":"text","isRequired":false,"keyType":"","default":null},"recommendations":{"name":"recommendations","type":"text","isRequired":false,"keyType":"","default":null},"crm":{"name":"crm","type":"string","isRequired":false,"keyType":"","default":"","length":"255"},"heading":{"name":"heading","type":"string","isRequired":false,"keyType":"","default":"","length":"255"},"corn_traits":{"name":"corn_traits","type":"text","isRequired":false,"keyType":"","default":null},"crop":{"name":"crop","type":"string","isRequired":false,"keyType":"","default":"","length":"255"},"fully_researched_and_proven":{"name":"fully_researched_and_proven","type":"int","isRequired":false,"keyType":"","length":"11","default":null},"improved_fermentation":{"name":"improved_fermentation","type":"int","isRequired":false,"keyType":"","length":"11","default":null},"aerobic_stability":{"name":"aerobic_stability","type":"int","isRequired":false,"keyType":"","length":"11","default":null},"improved_fibre_digestibility":{"name":"improved_fibre_digestibility","type":"int","isRequired":false,"keyType":"","length":"11","default":null},"sub_heading":{"name":"sub_heading","type":"string","isRequired":false,"keyType":"","default":"","length":"255"},"best":{"name":"best","type":"string","isRequired":false,"keyType":"","default":"","length":"255"},"intro":{"name":"intro","type":"string","isRequired":false,"keyType":"","default":"","length":"255"},"tech_notes":{"name":"tech_notes","type":"int","isRequired":false,"keyType":"","length":"11","default":null},"trait_ratings_disclaimer":{"name":"trait_ratings_disclaimer","type":"string","isRequired":false,"keyType":"","default":"","length":"255"},"usage":{"name":"usage","type":"string","isRequired":false,"keyType":"","default":"","length":"511"},"purpose":{"name":"purpose","type":"string","isRequired":false,"keyType":"","default":"","length":"255"},"genetic":{"name":"genetic","type":"string","isRequired":false,"keyType":"","default":"","length":"255"},"search":{"name":"search","type":"text","isRequired":false,"keyType":"MUL","default":null},"keywords":{"name":"keywords","type":"text","isRequired":false,"keyType":"","default":null},"usage_display":{"name":"usage_display","type":"string"},"bag_image":{"name":"bag_image","type":"string"}},"relationships":{"files":{"label":null,"type":"HasMany","class":"HybridFile"},"panels":{"label":null,"type":"HasMany","class":"Panel","refs":"\/panels\/_ref_"},"resource":{"label":null,"type":"HasOne","class":"Resource"},"attached_panels":{"label":null,"type":"BelongsToMany","class":"AttachedPanel","refs":"\/attached_panels\/_ref_"}}},"included":[],"label":"P1315 IT"},{"id":30,"type":"hybrid","attributes":{"id":30,"region_id":null,"name":"P1477W","content":"<p><img src=\"\/asset\/1995.png\" alt=\"P1477W - Segments and CRM.png\" width=\"304\" height=\"95\" \/> <img src=\"\/asset\/1994.png\" alt=\"P1477W - Maturity category.png\" width=\"177\" height=\"108\" \/><\/p>\n<h2>Market leader for white grain.<\/h2>\n<p>P1477W is a multi-purpose white grain corn hybrid, ideally suited to the processing market where white grain is required.<\/p>\n<ul style=\"list-style-type: square;\">\n<li>Pioneer's P1477W hybrid corn is also suited to the stock feed markets such as poultry and feedlots.<\/li>\n<li>It can also be used in silage production as <a title=\"Strike trials\" href=\"\/in-the-seed\/about-strike\"><strong>STRIKE trials <\/strong><\/a>have proven excellent feed quality from P1477W.<\/li>\n<\/ul>\n<p>Often considered the corn grower's premium white-grain hybrid, <span style=\"font-size: 1rem;\">P1477W stands tall and offers mid-season reliability, combined with a very good overall disease package against northern leaf blight, rust, eyespot and fusarium.<\/span><\/p>\n<p><img src=\"\/asset\/248.jpeg\" alt=\"p1477w-img-comp.jpg\" \/><\/p>\n<p style=\"margin-bottom: 1.5rem; font-size: 16px;\">Remember, if you plan to produce silage from P147W7, be sure to retain as much of the nutrient by complementing your feed with one of the <span style=\"font-weight: 600;\"><a title=\"Pioneer silage supplies link\" href=\"\/our-products\/silage-supplies\" target=\"_blank\" rel=\"noopener\">Pioneer inoculants<\/a> <\/span>designed for the task.<\/p>\n<p style=\"margin-bottom: 1.5rem; font-size: 16px;\">If you're thinking about growing white corn, we'd encourage you to discuss your on-farm options with one of our Pioneer Brand Seeds <a title=\"Contact a Pioneer representative\" href=\"\/contact-us\" target=\"_blank\" rel=\"noopener\"><span style=\"font-weight: 600;\">farm services consultants.<\/span><\/a> They have the knowledge and tools you need to minimise risk and maximise yield.<\/p>\n<p style=\"margin-bottom: 1.5rem; font-size: 16px;\">Alternatively, register with us (below) to stay informed of field days in your region, affording you an opportunity to see for yourself the impressive results of this mid-season white corn hybrid.<\/p>","content2":"<h3>KEY FEATURES<\/h3>\n<ul>\n<li>Superior grain quality, Australian standard for white grain<\/li>\n<li>Compact hybrid with great root and stalk strength<\/li>\n<li>Reliable Northern Leaf Blight resistance<\/li>\n<\/ul>\n<p><img src=\"\/asset\/1996.png\" alt=\"P1477W - Growing region recommendations.png\" width=\"279\" height=\"442\" \/><\/p>","image":{"id":2263,"parent_id":1991,"name":"PIO25015-007 Corn A4 P1477W MOCKUP.png","description":null,"storage":"assets","size":1167882,"extension":"png","mime_type":"image\/png","width":1731,"height":1487,"keywords":null,"usage":{"corn_hybrids.30":"P1477W"},"created_at":"2025-07-02T22:49:27.000000Z","updated_at":"2025-07-02T22:49:35.000000Z","readonly":null,"value":null,"_meta":null,"node_path":[{"id":1362,"name":"Hybrid icons","parent_id":null},{"id":1991,"name":"CORN P1477W","parent_id":1362},{"id":2263,"name":"PIO25015-007 Corn A4 P1477W MOCKUP.png","parent_id":1991}],"link":"\/asset\/2263.png","readable_size":"1.11 MB","secured":false,"secured_token":"eyJ0eXAiOiJKV1QiLCJhbGciOiJIUzI1NiJ9.eyJzdG9yYWdlcyI6WyJzZWN1cmVfYXNzZXRzIl0sImZpbGUiOjIyNjN9.fx04a5kwWEBR_u0zvbjbVbUwTu3bFcjQ7MOdbnTaqyk","full_path":"1362\/1991\/2263"},"custom_bag_image":null,"graph_image":null,"map_image":null,"new":0,"position":53,"plantheight":null,"type":"corn","title":"P1477W","name_id":"p1477w","meta_keywords":"corn, hybrid, processing, yield, white, grain, silage, seed, feed","meta_description":"P1477W is a highly versatile white grain corn hybrid that is ideal for both silage and processing. With high yield potential and exceptional performance in a range of conditions, P1477W is a top choice for farmers looking for a reliable and productive corn hybrid. Learn more about its features and benefits on this page.","tolerancetrait":null,"producttype":null,"maturity":"Mid Season","phenology":null,"blacklegroup":null,"grainoilcontent":null,"plantvigour":null,"cropstandability":null,"shattertolerance":null,"graintestweight":null,"blacklegrating":null,"blacklegresistancegrouping":null,"performertype":null,"crmnumber":null,"crmposition":null,"graintoyieldmaturity":null,"droughttolerance":null,"stalkstrength":null,"rootstrength":null,"staygreen":null,"huskcover":null,"northernleafblight":null,"commonrust":null,"cobrot":null,"harvestdaystart":null,"harvestdayend":null,"silageyieldmaturity":null,"drylandadaptability":null,"wholeplantdigestibility":null,"agronomy_traits":{"grain_yield_for_maturity":"9","husk_cover":"6","plant_height":"7","cob_rot_resistance":"6","dryland_adaptability":null,"northern_leaf_blight":"7","silage_yield_for_maturity":"9","staygreen":"7","whole_plant_digestibility":"6"},"disease_traits":[],"characteristics":[],"recommendations":[],"crm":"114","heading":"P1477W Corn Hybrid","corn_traits":null,"crop":null,"fully_researched_and_proven":null,"improved_fermentation":null,"aerobic_stability":null,"improved_fibre_digestibility":null,"sub_heading":null,"best":null,"intro":"Market leader for white grain.","tech_notes":1997,"trait_ratings_disclaimer":null,"usage":"[\"Specialty\"]","purpose":null,"genetic":null,"search":"p1477w","keywords":null,"content_id":358,"usage_display":"Specialty","bag_image":null},"meta":{"priority":"position","priority_order":"asc","active":1,"created_at":"2021-03-11 17:43:57","updated_at":"2025-07-03 10:49:35"},"schema":{"collectionType":"hybrids","attributes":{"region_id":{"name":"region_id","type":"int","isRequired":false,"keyType":"","length":"10","default":null},"name":{"name":"name","type":"string","isRequired":false,"keyType":"","default":"","length":"255"},"content":{"type":"text"},"content2":{"name":"content2","type":"text","isRequired":false,"keyType":"","default":null},"image":{"name":"image","type":"asset","isRequired":false,"keyType":"","length":"11","default":null,"extensions":["jpeg","jpg","png","svg"],"upload_dir":null,"upload_storage":null},"custom_bag_image":{"name":"custom_bag_image","type":"asset","isRequired":false,"keyType":"","length":"11","default":null,"extensions":["jpeg","jpg","png","svg"],"upload_dir":null,"upload_storage":null},"graph_image":{"name":"graph_image","type":"asset","isRequired":false,"keyType":"","length":"11","default":null,"extensions":["jpeg","jpg","png","svg"],"upload_dir":null,"upload_storage":null},"map_image":{"name":"map_image","type":"int","isRequired":false,"keyType":"","length":"11","default":null},"new":{"name":"new","type":"tinyint","isRequired":false,"keyType":"","length":"1","default":null},"position":{"name":"position","type":"int","isRequired":false,"keyType":"","length":"11","default":null},"plantheight":{"name":"plantheight","type":"int","isRequired":false,"keyType":"","length":"11","default":null},"type":{"name":"type","type":"string","isRequired":false,"keyType":"","default":"","length":"255"},"title":{"name":"title","type":"string","isRequired":false,"keyType":"","default":"","length":"255"},"name_id":{"name":"name_id","type":"string","isRequired":false,"keyType":"","default":"","length":"255"},"meta_keywords":{"name":"meta_keywords","type":"text","isRequired":false,"keyType":"","default":null},"meta_description":{"name":"meta_description","type":"text","isRequired":false,"keyType":"","default":null},"tolerancetrait":{"name":"tolerancetrait","type":"string","isRequired":false,"keyType":"","default":"","length":"255"},"producttype":{"name":"producttype","type":"string","isRequired":false,"keyType":"","default":"","length":"255"},"maturity":{"name":"maturity","type":"string","isRequired":false,"keyType":"","default":"","length":"30"},"phenology":{"name":"phenology","type":"string","isRequired":false,"keyType":"","default":"","length":"30"},"blacklegroup":{"name":"blacklegroup","type":"string","isRequired":false,"keyType":"","default":"","length":"255"},"grainoilcontent":{"name":"grainoilcontent","type":"int","isRequired":false,"keyType":"","length":"11","default":null},"plantvigour":{"name":"plantvigour","type":"int","isRequired":false,"keyType":"","length":"11","default":null},"cropstandability":{"name":"cropstandability","type":"int","isRequired":false,"keyType":"","length":"11","default":null},"shattertolerance":{"name":"shattertolerance","type":"int","isRequired":false,"keyType":"","length":"11","default":null},"graintestweight":{"name":"graintestweight","type":"string","isRequired":false,"keyType":"","default":"","length":"11"},"blacklegrating":{"name":"blacklegrating","type":"string","isRequired":false,"keyType":"","default":"","length":"255"},"blacklegresistancegrouping":{"name":"blacklegresistancegrouping","type":"string","isRequired":false,"keyType":"","default":"","length":"255"},"performertype":{"name":"performertype","type":"enum","isRequired":false,"keyType":"","default":null,"length":"255","values":["Elite","Proven"]},"crmnumber":{"name":"crmnumber","type":"int","isRequired":false,"keyType":"","length":"11","default":null},"crmposition":{"name":"crmposition","type":"string","isRequired":false,"keyType":"","default":"","length":"255"},"graintoyieldmaturity":{"name":"graintoyieldmaturity","type":"string","isRequired":false,"keyType":"","default":"","length":"255"},"droughttolerance":{"name":"droughttolerance","type":"string","isRequired":false,"keyType":"","default":"","length":"255"},"stalkstrength":{"name":"stalkstrength","type":"string","isRequired":false,"keyType":"","default":"","length":"255"},"rootstrength":{"name":"rootstrength","type":"string","isRequired":false,"keyType":"","default":"","length":"255"},"staygreen":{"name":"staygreen","type":"string","isRequired":false,"keyType":"","default":"","length":"255"},"huskcover":{"name":"huskcover","type":"string","isRequired":false,"keyType":"","default":"","length":"255"},"northernleafblight":{"name":"northernleafblight","type":"string","isRequired":false,"keyType":"","default":"","length":"255"},"commonrust":{"name":"commonrust","type":"string","isRequired":false,"keyType":"","default":"","length":"255"},"cobrot":{"name":"cobrot","type":"string","isRequired":false,"keyType":"","default":"","length":"255"},"harvestdaystart":{"name":"harvestdaystart","type":"int","isRequired":false,"keyType":"","length":"11","default":null},"harvestdayend":{"name":"harvestdayend","type":"int","isRequired":false,"keyType":"","length":"11","default":null},"silageyieldmaturity":{"name":"silageyieldmaturity","type":"string","isRequired":false,"keyType":"","default":"","length":"255"},"drylandadaptability":{"name":"drylandadaptability","type":"string","isRequired":false,"keyType":"","default":"","length":"255"},"wholeplantdigestibility":{"name":"wholeplantdigestibility","type":"string","isRequired":false,"keyType":"","default":"","length":"255"},"agronomy_traits":{"name":"agronomy_traits","type":"object","isRequired":false,"keyType":"","default":null,"fields":[]},"disease_traits":{"name":"disease_traits","type":"text","isRequired":false,"keyType":"","default":null},"characteristics":{"name":"characteristics","type":"text","isRequired":false,"keyType":"","default":null},"recommendations":{"name":"recommendations","type":"text","isRequired":false,"keyType":"","default":null},"crm":{"name":"crm","type":"string","isRequired":false,"keyType":"","default":"","length":"255"},"heading":{"name":"heading","type":"string","isRequired":false,"keyType":"","default":"","length":"255"},"corn_traits":{"name":"corn_traits","type":"text","isRequired":false,"keyType":"","default":null},"crop":{"name":"crop","type":"string","isRequired":false,"keyType":"","default":"","length":"255"},"fully_researched_and_proven":{"name":"fully_researched_and_proven","type":"int","isRequired":false,"keyType":"","length":"11","default":null},"improved_fermentation":{"name":"improved_fermentation","type":"int","isRequired":false,"keyType":"","length":"11","default":null},"aerobic_stability":{"name":"aerobic_stability","type":"int","isRequired":false,"keyType":"","length":"11","default":null},"improved_fibre_digestibility":{"name":"improved_fibre_digestibility","type":"int","isRequired":false,"keyType":"","length":"11","default":null},"sub_heading":{"name":"sub_heading","type":"string","isRequired":false,"keyType":"","default":"","length":"255"},"best":{"name":"best","type":"string","isRequired":false,"keyType":"","default":"","length":"255"},"intro":{"name":"intro","type":"string","isRequired":false,"keyType":"","default":"","length":"255"},"tech_notes":{"name":"tech_notes","type":"int","isRequired":false,"keyType":"","length":"11","default":null},"trait_ratings_disclaimer":{"name":"trait_ratings_disclaimer","type":"string","isRequired":false,"keyType":"","default":"","length":"255"},"usage":{"name":"usage","type":"string","isRequired":false,"keyType":"","default":"","length":"511"},"purpose":{"name":"purpose","type":"string","isRequired":false,"keyType":"","default":"","length":"255"},"genetic":{"name":"genetic","type":"string","isRequired":false,"keyType":"","default":"","length":"255"},"search":{"name":"search","type":"text","isRequired":false,"keyType":"MUL","default":null},"keywords":{"name":"keywords","type":"text","isRequired":false,"keyType":"","default":null},"usage_display":{"name":"usage_display","type":"string"},"bag_image":{"name":"bag_image","type":"string"}},"relationships":{"files":{"label":null,"type":"HasMany","class":"HybridFile"},"panels":{"label":null,"type":"HasMany","class":"Panel","refs":"\/panels\/_ref_"},"resource":{"label":null,"type":"HasOne","class":"Resource"},"attached_panels":{"label":null,"type":"BelongsToMany","class":"AttachedPanel","refs":"\/attached_panels\/_ref_"}}},"included":[],"label":"P1477W"},{"id":94,"type":"hybrid","attributes":{"id":94,"region_id":null,"name":"P15744 IT","content":"<p><img src=\"\/asset\/2057.png\" alt=\"P15744 IT - Segments and CRM.png\" width=\"244\" height=\"100\" \/> <img src=\"\/asset\/2056.png\" alt=\"P15744 IT - Maturity category.png\" width=\"160\" height=\"98\" \/> <\/p>\n<h2>Compact hybrid with top end yield potential.<\/h2>\n<p>Excellent drought tolerance drives high performance in dryland and irrigated systems.<\/p>\n<p>P15744 IT performs across dryland and irrigated situations. Replaces P1481 and a slightly longer maturity companion to P1315 IT in the hybrid lineup.<\/p>","content2":"<h3>KEY FEATURES<\/h3>\n<ul>\n<li>Impressive silage and grain yield for maturity across environments<\/li>\n<li>High Northern Leaf Blight resistance with superior root and stalk strength<\/li>\n<li>Sound husk cover protects the developing cob and moderate staygreen brings harvest forward in regions with a shorter season<\/li>\n<li>Imidazolinone herbicide tolerance provides options for in crop grass weed control<\/li>\n<\/ul>\n<p><img src=\"\/asset\/2058.png\" alt=\"P15744 IT - Growing region recommendations.png\" width=\"304\" height=\"442\" \/><\/p>","image":{"id":2264,"parent_id":2054,"name":"PIO25015-007 Corn A4 P15744 IT MOCKUP.png","description":null,"storage":"assets","size":1106034,"extension":"png","mime_type":"image\/png","width":1731,"height":1487,"keywords":null,"usage":{"corn_hybrids.94":"P15744 IT"},"created_at":"2025-07-02T22:54:22.000000Z","updated_at":"2025-07-02T22:54:29.000000Z","readonly":null,"value":null,"_meta":null,"node_path":[{"id":1362,"name":"Hybrid icons","parent_id":null},{"id":2054,"name":"CORN P15744 IT","parent_id":1362},{"id":2264,"name":"PIO25015-007 Corn A4 P15744 IT MOCKUP.png","parent_id":2054}],"link":"\/asset\/2264.png","readable_size":"1.05 MB","secured":false,"secured_token":"eyJ0eXAiOiJKV1QiLCJhbGciOiJIUzI1NiJ9.eyJzdG9yYWdlcyI6WyJzZWN1cmVfYXNzZXRzIl0sImZpbGUiOjIyNjR9.xOaT25O8Vs4ZSfYg9EpjfWpzQIVIoiYa9EH7sPSMBl4","full_path":"1362\/2054\/2264"},"custom_bag_image":null,"graph_image":null,"map_image":null,"new":1,"position":61,"plantheight":null,"type":"corn","title":"P15744 IT","name_id":"p-15744-it","meta_keywords":null,"meta_description":null,"tolerancetrait":null,"producttype":null,"maturity":"Mid Season","phenology":null,"blacklegroup":null,"grainoilcontent":null,"plantvigour":null,"cropstandability":null,"shattertolerance":null,"graintestweight":null,"blacklegrating":null,"blacklegresistancegrouping":null,"performertype":null,"crmnumber":null,"crmposition":null,"graintoyieldmaturity":null,"droughttolerance":null,"stalkstrength":null,"rootstrength":null,"staygreen":null,"huskcover":null,"northernleafblight":null,"commonrust":null,"cobrot":null,"harvestdaystart":null,"harvestdayend":null,"silageyieldmaturity":null,"drylandadaptability":null,"wholeplantdigestibility":null,"agronomy_traits":{"grain_yield_for_maturity":"9","husk_cover":"7.5","plant_height":"6","cob_rot_resistance":"8","dryland_adaptability":"6","northern_leaf_blight":"7","silage_yield_for_maturity":"8","staygreen":"8","whole_plant_digestibility":"8"},"disease_traits":[],"characteristics":[],"recommendations":[],"crm":"115","heading":"P15744 IT Corn Hybrid","corn_traits":null,"crop":null,"fully_researched_and_proven":null,"improved_fermentation":null,"aerobic_stability":null,"improved_fibre_digestibility":null,"sub_heading":null,"best":null,"intro":"Compact hybrid with top end yield potential.","tech_notes":2060,"trait_ratings_disclaimer":null,"usage":"[\"Grain\",\"Silage\"]","purpose":null,"genetic":null,"search":"p15744 kw_it","keywords":null,"content_id":1016,"usage_display":"Grain \/ Silage","bag_image":null},"meta":{"priority":"position","priority_order":"asc","active":1,"created_at":"2025-07-01 15:15:31","updated_at":"2025-07-03 10:54:29"},"schema":{"collectionType":"hybrids","attributes":{"region_id":{"name":"region_id","type":"int","isRequired":false,"keyType":"","length":"10","default":null},"name":{"name":"name","type":"string","isRequired":false,"keyType":"","default":"","length":"255"},"content":{"type":"text"},"content2":{"name":"content2","type":"text","isRequired":false,"keyType":"","default":null},"image":{"name":"image","type":"asset","isRequired":false,"keyType":"","length":"11","default":null,"extensions":["jpeg","jpg","png","svg"],"upload_dir":null,"upload_storage":null},"custom_bag_image":{"name":"custom_bag_image","type":"asset","isRequired":false,"keyType":"","length":"11","default":null,"extensions":["jpeg","jpg","png","svg"],"upload_dir":null,"upload_storage":null},"graph_image":{"name":"graph_image","type":"asset","isRequired":false,"keyType":"","length":"11","default":null,"extensions":["jpeg","jpg","png","svg"],"upload_dir":null,"upload_storage":null},"map_image":{"name":"map_image","type":"int","isRequired":false,"keyType":"","length":"11","default":null},"new":{"name":"new","type":"tinyint","isRequired":false,"keyType":"","length":"1","default":null},"position":{"name":"position","type":"int","isRequired":false,"keyType":"","length":"11","default":null},"plantheight":{"name":"plantheight","type":"int","isRequired":false,"keyType":"","length":"11","default":null},"type":{"name":"type","type":"string","isRequired":false,"keyType":"","default":"","length":"255"},"title":{"name":"title","type":"string","isRequired":false,"keyType":"","default":"","length":"255"},"name_id":{"name":"name_id","type":"string","isRequired":false,"keyType":"","default":"","length":"255"},"meta_keywords":{"name":"meta_keywords","type":"text","isRequired":false,"keyType":"","default":null},"meta_description":{"name":"meta_description","type":"text","isRequired":false,"keyType":"","default":null},"tolerancetrait":{"name":"tolerancetrait","type":"string","isRequired":false,"keyType":"","default":"","length":"255"},"producttype":{"name":"producttype","type":"string","isRequired":false,"keyType":"","default":"","length":"255"},"maturity":{"name":"maturity","type":"string","isRequired":false,"keyType":"","default":"","length":"30"},"phenology":{"name":"phenology","type":"string","isRequired":false,"keyType":"","default":"","length":"30"},"blacklegroup":{"name":"blacklegroup","type":"string","isRequired":false,"keyType":"","default":"","length":"255"},"grainoilcontent":{"name":"grainoilcontent","type":"int","isRequired":false,"keyType":"","length":"11","default":null},"plantvigour":{"name":"plantvigour","type":"int","isRequired":false,"keyType":"","length":"11","default":null},"cropstandability":{"name":"cropstandability","type":"int","isRequired":false,"keyType":"","length":"11","default":null},"shattertolerance":{"name":"shattertolerance","type":"int","isRequired":false,"keyType":"","length":"11","default":null},"graintestweight":{"name":"graintestweight","type":"string","isRequired":false,"keyType":"","default":"","length":"11"},"blacklegrating":{"name":"blacklegrating","type":"string","isRequired":false,"keyType":"","default":"","length":"255"},"blacklegresistancegrouping":{"name":"blacklegresistancegrouping","type":"string","isRequired":false,"keyType":"","default":"","length":"255"},"performertype":{"name":"performertype","type":"enum","isRequired":false,"keyType":"","default":null,"length":"255","values":["Elite","Proven"]},"crmnumber":{"name":"crmnumber","type":"int","isRequired":false,"keyType":"","length":"11","default":null},"crmposition":{"name":"crmposition","type":"string","isRequired":false,"keyType":"","default":"","length":"255"},"graintoyieldmaturity":{"name":"graintoyieldmaturity","type":"string","isRequired":false,"keyType":"","default":"","length":"255"},"droughttolerance":{"name":"droughttolerance","type":"string","isRequired":false,"keyType":"","default":"","length":"255"},"stalkstrength":{"name":"stalkstrength","type":"string","isRequired":false,"keyType":"","default":"","length":"255"},"rootstrength":{"name":"rootstrength","type":"string","isRequired":false,"keyType":"","default":"","length":"255"},"staygreen":{"name":"staygreen","type":"string","isRequired":false,"keyType":"","default":"","length":"255"},"huskcover":{"name":"huskcover","type":"string","isRequired":false,"keyType":"","default":"","length":"255"},"northernleafblight":{"name":"northernleafblight","type":"string","isRequired":false,"keyType":"","default":"","length":"255"},"commonrust":{"name":"commonrust","type":"string","isRequired":false,"keyType":"","default":"","length":"255"},"cobrot":{"name":"cobrot","type":"string","isRequired":false,"keyType":"","default":"","length":"255"},"harvestdaystart":{"name":"harvestdaystart","type":"int","isRequired":false,"keyType":"","length":"11","default":null},"harvestdayend":{"name":"harvestdayend","type":"int","isRequired":false,"keyType":"","length":"11","default":null},"silageyieldmaturity":{"name":"silageyieldmaturity","type":"string","isRequired":false,"keyType":"","default":"","length":"255"},"drylandadaptability":{"name":"drylandadaptability","type":"string","isRequired":false,"keyType":"","default":"","length":"255"},"wholeplantdigestibility":{"name":"wholeplantdigestibility","type":"string","isRequired":false,"keyType":"","default":"","length":"255"},"agronomy_traits":{"name":"agronomy_traits","type":"object","isRequired":false,"keyType":"","default":null,"fields":[]},"disease_traits":{"name":"disease_traits","type":"text","isRequired":false,"keyType":"","default":null},"characteristics":{"name":"characteristics","type":"text","isRequired":false,"keyType":"","default":null},"recommendations":{"name":"recommendations","type":"text","isRequired":false,"keyType":"","default":null},"crm":{"name":"crm","type":"string","isRequired":false,"keyType":"","default":"","length":"255"},"heading":{"name":"heading","type":"string","isRequired":false,"keyType":"","default":"","length":"255"},"corn_traits":{"name":"corn_traits","type":"text","isRequired":false,"keyType":"","default":null},"crop":{"name":"crop","type":"string","isRequired":false,"keyType":"","default":"","length":"255"},"fully_researched_and_proven":{"name":"fully_researched_and_proven","type":"int","isRequired":false,"keyType":"","length":"11","default":null},"improved_fermentation":{"name":"improved_fermentation","type":"int","isRequired":false,"keyType":"","length":"11","default":null},"aerobic_stability":{"name":"aerobic_stability","type":"int","isRequired":false,"keyType":"","length":"11","default":null},"improved_fibre_digestibility":{"name":"improved_fibre_digestibility","type":"int","isRequired":false,"keyType":"","length":"11","default":null},"sub_heading":{"name":"sub_heading","type":"string","isRequired":false,"keyType":"","default":"","length":"255"},"best":{"name":"best","type":"string","isRequired":false,"keyType":"","default":"","length":"255"},"intro":{"name":"intro","type":"string","isRequired":false,"keyType":"","default":"","length":"255"},"tech_notes":{"name":"tech_notes","type":"int","isRequired":false,"keyType":"","length":"11","default":null},"trait_ratings_disclaimer":{"name":"trait_ratings_disclaimer","type":"string","isRequired":false,"keyType":"","default":"","length":"255"},"usage":{"name":"usage","type":"string","isRequired":false,"keyType":"","default":"","length":"511"},"purpose":{"name":"purpose","type":"string","isRequired":false,"keyType":"","default":"","length":"255"},"genetic":{"name":"genetic","type":"string","isRequired":false,"keyType":"","default":"","length":"255"},"search":{"name":"search","type":"text","isRequired":false,"keyType":"MUL","default":null},"keywords":{"name":"keywords","type":"text","isRequired":false,"keyType":"","default":null},"usage_display":{"name":"usage_display","type":"string"},"bag_image":{"name":"bag_image","type":"string"}},"relationships":{"files":{"label":null,"type":"HasMany","class":"HybridFile"},"panels":{"label":null,"type":"HasMany","class":"Panel","refs":"\/panels\/_ref_"},"resource":{"label":null,"type":"HasOne","class":"Resource"},"attached_panels":{"label":null,"type":"BelongsToMany","class":"AttachedPanel","refs":"\/attached_panels\/_ref_"}}},"included":[],"label":"P15744 IT"},{"id":86,"type":"hybrid","attributes":{"id":86,"region_id":null,"name":"P1729","content":"<p><img src=\"\/asset\/1987.png\" alt=\"P1729 - Segments and CRM.png\" width=\"307\" height=\"96\" \/> <img src=\"\/asset\/1986.png\" alt=\"P1729 - Maturity category.png\" width=\"153\" height=\"93\" \/><\/p>\n<h2>Tall, all-rounder that won’t disappoint.<\/h2>\n<p>Well balanced, full season hybrid providing consistent and reliable yields with excellent agronomics.<\/p>\n<p>Pioneer Seeds extensive breeding and STRIKE trials have shown P1729 to be an exceptional performer in all dryland and irrigated environments that it was test in. P1729 further strength's Pioneer Seeds processing lineup of P1837 and P1756.<\/p>","content2":"<h3>KEY FEATURES<\/h3>\n<ul>\n<li>Excellent drought tolerance and standability, foliar health drives top grain and silage yields for its maturity<\/li>\n<li>High level performance from Northern Victoria to North QLD, NT & top end Western Australia<\/li>\n<li>Processing market grain quality gives flexibility of end use from silage, feed grain or processing<\/li>\n<\/ul>\n<p><img src=\"\/asset\/1988.png\" alt=\"P1729 - Growing region recommendations.png\" width=\"296\" height=\"490\" \/><\/p>","image":{"id":2265,"parent_id":1984,"name":"PIO25015-007 Corn A4 P1729 MOCKUP.png","description":null,"storage":"assets","size":1154160,"extension":"png","mime_type":"image\/png","width":1731,"height":1487,"keywords":null,"usage":{"corn_hybrids.86":"P1729"},"created_at":"2025-07-02T22:56:02.000000Z","updated_at":"2025-07-02T22:56:16.000000Z","readonly":null,"value":null,"_meta":null,"node_path":[{"id":1362,"name":"Hybrid icons","parent_id":null},{"id":1984,"name":"CORN P1729","parent_id":1362},{"id":2265,"name":"PIO25015-007 Corn A4 P1729 MOCKUP.png","parent_id":1984}],"link":"\/asset\/2265.png","readable_size":"1.10 MB","secured":false,"secured_token":"eyJ0eXAiOiJKV1QiLCJhbGciOiJIUzI1NiJ9.eyJzdG9yYWdlcyI6WyJzZWN1cmVfYXNzZXRzIl0sImZpbGUiOjIyNjV9.0c2z1koZ1IV1T_aWjN7nMXsou-jsrEiAoaiN64DBNv4","full_path":"1362\/1984\/2265"},"custom_bag_image":null,"graph_image":null,"map_image":null,"new":0,"position":62,"plantheight":null,"type":"corn","title":"P1729","name_id":"P1729","meta_keywords":null,"meta_description":null,"tolerancetrait":null,"producttype":null,"maturity":"Full Season","phenology":null,"blacklegroup":null,"grainoilcontent":null,"plantvigour":null,"cropstandability":null,"shattertolerance":null,"graintestweight":null,"blacklegrating":null,"blacklegresistancegrouping":null,"performertype":null,"crmnumber":null,"crmposition":null,"graintoyieldmaturity":null,"droughttolerance":null,"stalkstrength":null,"rootstrength":null,"staygreen":null,"huskcover":null,"northernleafblight":null,"commonrust":null,"cobrot":null,"harvestdaystart":null,"harvestdayend":null,"silageyieldmaturity":null,"drylandadaptability":null,"wholeplantdigestibility":null,"agronomy_traits":{"grain_yield_for_maturity":"8","husk_cover":"7","plant_height":"8","cob_rot_resistance":"8","dryland_adaptability":"8","northern_leaf_blight":"7","silage_yield_for_maturity":"8","staygreen":"7","whole_plant_digestibility":"7"},"disease_traits":[],"characteristics":[],"recommendations":[],"crm":"117","heading":"P1729 Corn Hybrid","corn_traits":null,"crop":null,"fully_researched_and_proven":null,"improved_fermentation":null,"aerobic_stability":null,"improved_fibre_digestibility":null,"sub_heading":null,"best":null,"intro":"Tall, all-rounder that won\u2019t disappoint.","tech_notes":1990,"trait_ratings_disclaimer":null,"usage":"[\"Dual Purpose\",\"Silage\"]","purpose":null,"genetic":null,"search":"p1729","keywords":null,"content_id":890,"usage_display":"Dual Purpose \/ Silage","bag_image":null},"meta":{"priority":"position","priority_order":"asc","active":1,"created_at":"2024-07-14 17:04:32","updated_at":"2025-07-03 10:56:16"},"schema":{"collectionType":"hybrids","attributes":{"region_id":{"name":"region_id","type":"int","isRequired":false,"keyType":"","length":"10","default":null},"name":{"name":"name","type":"string","isRequired":false,"keyType":"","default":"","length":"255"},"content":{"type":"text"},"content2":{"name":"content2","type":"text","isRequired":false,"keyType":"","default":null},"image":{"name":"image","type":"asset","isRequired":false,"keyType":"","length":"11","default":null,"extensions":["jpeg","jpg","png","svg"],"upload_dir":null,"upload_storage":null},"custom_bag_image":{"name":"custom_bag_image","type":"asset","isRequired":false,"keyType":"","length":"11","default":null,"extensions":["jpeg","jpg","png","svg"],"upload_dir":null,"upload_storage":null},"graph_image":{"name":"graph_image","type":"asset","isRequired":false,"keyType":"","length":"11","default":null,"extensions":["jpeg","jpg","png","svg"],"upload_dir":null,"upload_storage":null},"map_image":{"name":"map_image","type":"int","isRequired":false,"keyType":"","length":"11","default":null},"new":{"name":"new","type":"tinyint","isRequired":false,"keyType":"","length":"1","default":null},"position":{"name":"position","type":"int","isRequired":false,"keyType":"","length":"11","default":null},"plantheight":{"name":"plantheight","type":"int","isRequired":false,"keyType":"","length":"11","default":null},"type":{"name":"type","type":"string","isRequired":false,"keyType":"","default":"","length":"255"},"title":{"name":"title","type":"string","isRequired":false,"keyType":"","default":"","length":"255"},"name_id":{"name":"name_id","type":"string","isRequired":false,"keyType":"","default":"","length":"255"},"meta_keywords":{"name":"meta_keywords","type":"text","isRequired":false,"keyType":"","default":null},"meta_description":{"name":"meta_description","type":"text","isRequired":false,"keyType":"","default":null},"tolerancetrait":{"name":"tolerancetrait","type":"string","isRequired":false,"keyType":"","default":"","length":"255"},"producttype":{"name":"producttype","type":"string","isRequired":false,"keyType":"","default":"","length":"255"},"maturity":{"name":"maturity","type":"string","isRequired":false,"keyType":"","default":"","length":"30"},"phenology":{"name":"phenology","type":"string","isRequired":false,"keyType":"","default":"","length":"30"},"blacklegroup":{"name":"blacklegroup","type":"string","isRequired":false,"keyType":"","default":"","length":"255"},"grainoilcontent":{"name":"grainoilcontent","type":"int","isRequired":false,"keyType":"","length":"11","default":null},"plantvigour":{"name":"plantvigour","type":"int","isRequired":false,"keyType":"","length":"11","default":null},"cropstandability":{"name":"cropstandability","type":"int","isRequired":false,"keyType":"","length":"11","default":null},"shattertolerance":{"name":"shattertolerance","type":"int","isRequired":false,"keyType":"","length":"11","default":null},"graintestweight":{"name":"graintestweight","type":"string","isRequired":false,"keyType":"","default":"","length":"11"},"blacklegrating":{"name":"blacklegrating","type":"string","isRequired":false,"keyType":"","default":"","length":"255"},"blacklegresistancegrouping":{"name":"blacklegresistancegrouping","type":"string","isRequired":false,"keyType":"","default":"","length":"255"},"performertype":{"name":"performertype","type":"enum","isRequired":false,"keyType":"","default":null,"length":"255","values":["Elite","Proven"]},"crmnumber":{"name":"crmnumber","type":"int","isRequired":false,"keyType":"","length":"11","default":null},"crmposition":{"name":"crmposition","type":"string","isRequired":false,"keyType":"","default":"","length":"255"},"graintoyieldmaturity":{"name":"graintoyieldmaturity","type":"string","isRequired":false,"keyType":"","default":"","length":"255"},"droughttolerance":{"name":"droughttolerance","type":"string","isRequired":false,"keyType":"","default":"","length":"255"},"stalkstrength":{"name":"stalkstrength","type":"string","isRequired":false,"keyType":"","default":"","length":"255"},"rootstrength":{"name":"rootstrength","type":"string","isRequired":false,"keyType":"","default":"","length":"255"},"staygreen":{"name":"staygreen","type":"string","isRequired":false,"keyType":"","default":"","length":"255"},"huskcover":{"name":"huskcover","type":"string","isRequired":false,"keyType":"","default":"","length":"255"},"northernleafblight":{"name":"northernleafblight","type":"string","isRequired":false,"keyType":"","default":"","length":"255"},"commonrust":{"name":"commonrust","type":"string","isRequired":false,"keyType":"","default":"","length":"255"},"cobrot":{"name":"cobrot","type":"string","isRequired":false,"keyType":"","default":"","length":"255"},"harvestdaystart":{"name":"harvestdaystart","type":"int","isRequired":false,"keyType":"","length":"11","default":null},"harvestdayend":{"name":"harvestdayend","type":"int","isRequired":false,"keyType":"","length":"11","default":null},"silageyieldmaturity":{"name":"silageyieldmaturity","type":"string","isRequired":false,"keyType":"","default":"","length":"255"},"drylandadaptability":{"name":"drylandadaptability","type":"string","isRequired":false,"keyType":"","default":"","length":"255"},"wholeplantdigestibility":{"name":"wholeplantdigestibility","type":"string","isRequired":false,"keyType":"","default":"","length":"255"},"agronomy_traits":{"name":"agronomy_traits","type":"object","isRequired":false,"keyType":"","default":null,"fields":[]},"disease_traits":{"name":"disease_traits","type":"text","isRequired":false,"keyType":"","default":null},"characteristics":{"name":"characteristics","type":"text","isRequired":false,"keyType":"","default":null},"recommendations":{"name":"recommendations","type":"text","isRequired":false,"keyType":"","default":null},"crm":{"name":"crm","type":"string","isRequired":false,"keyType":"","default":"","length":"255"},"heading":{"name":"heading","type":"string","isRequired":false,"keyType":"","default":"","length":"255"},"corn_traits":{"name":"corn_traits","type":"text","isRequired":false,"keyType":"","default":null},"crop":{"name":"crop","type":"string","isRequired":false,"keyType":"","default":"","length":"255"},"fully_researched_and_proven":{"name":"fully_researched_and_proven","type":"int","isRequired":false,"keyType":"","length":"11","default":null},"improved_fermentation":{"name":"improved_fermentation","type":"int","isRequired":false,"keyType":"","length":"11","default":null},"aerobic_stability":{"name":"aerobic_stability","type":"int","isRequired":false,"keyType":"","length":"11","default":null},"improved_fibre_digestibility":{"name":"improved_fibre_digestibility","type":"int","isRequired":false,"keyType":"","length":"11","default":null},"sub_heading":{"name":"sub_heading","type":"string","isRequired":false,"keyType":"","default":"","length":"255"},"best":{"name":"best","type":"string","isRequired":false,"keyType":"","default":"","length":"255"},"intro":{"name":"intro","type":"string","isRequired":false,"keyType":"","default":"","length":"255"},"tech_notes":{"name":"tech_notes","type":"int","isRequired":false,"keyType":"","length":"11","default":null},"trait_ratings_disclaimer":{"name":"trait_ratings_disclaimer","type":"string","isRequired":false,"keyType":"","default":"","length":"255"},"usage":{"name":"usage","type":"string","isRequired":false,"keyType":"","default":"","length":"511"},"purpose":{"name":"purpose","type":"string","isRequired":false,"keyType":"","default":"","length":"255"},"genetic":{"name":"genetic","type":"string","isRequired":false,"keyType":"","default":"","length":"255"},"search":{"name":"search","type":"text","isRequired":false,"keyType":"MUL","default":null},"keywords":{"name":"keywords","type":"text","isRequired":false,"keyType":"","default":null},"usage_display":{"name":"usage_display","type":"string"},"bag_image":{"name":"bag_image","type":"string"}},"relationships":{"files":{"label":null,"type":"HasMany","class":"HybridFile"},"panels":{"label":null,"type":"HasMany","class":"Panel","refs":"\/panels\/_ref_"},"resource":{"label":null,"type":"HasOne","class":"Resource"},"attached_panels":{"label":null,"type":"BelongsToMany","class":"AttachedPanel","refs":"\/attached_panels\/_ref_"}}},"included":[],"label":"P1729"},{"id":23,"type":"hybrid","attributes":{"id":23,"region_id":null,"name":"P1756","content":"<p><img src=\"\/asset\/1979.png\" alt=\"P1756 - Segments and CRM.png\" width=\"291\" height=\"91\" \/> <img src=\"\/asset\/1980.png\" alt=\"P1756 - Maturity category.png\" width=\"157\" height=\"95\" \/><\/p>\n<h2>Well-known grain quality leader.<\/h2>\n<h2><span style=\"font-size: 1rem; font-weight: 500;\">Pioneer® P1756 <\/span><span style=\"font-size: 1rem;\">is a 117CRM corn hybrid uniquely bred in Australia for the Australian corn processing market and the Asian export markets.<\/span><\/h2>\n<p>P1756 exhibits excellent stalk strength and is suited to both dryland and irrigation areas.<\/p>\n<p><span style=\"color: inherit; font-family: inherit; font-size: 1.25rem; font-weight: bold;\">It can also be used as a feed grain and makes for high-quality silage.<\/span><\/p>\n<p>If you plan to produce silage from <span style=\"font-size: 1rem;\">P1756<\/span><span style=\"font-size: 1rem;\"> <\/span><span style=\"font-size: 1rem;\">corn, be sure to retain as much of the nutrient by complementing your feed with <\/span><span style=\"font-size: 1rem;\">one of the <a title=\"silage products\" href=\"\/our-products\/silage-supplies\" target=\"_blank\" rel=\"noopener\"><strong>Pioneer inoculants <\/strong><\/a>designed for the job.<\/span><\/p>\n<p>The type and number of acid-producing bacteria present in your pasture or crop will influence the amount of dry matter and nutrients you lose in the ensiling process.<\/p>\n<p>Pioneer® brand \u200bproduct \u200binoculants provide the right bacteria in ideal numbers for a fast, efficient fermentation. They help lock-in nutrients and dry matter so your livestock can produce more milk or meat from every tonne of pasture or crop you ensile.<\/p>\n<p>Discuss planting options with your local Pioneer Brand Seeds <span style=\"font-weight: 600;\"><a title=\"Contact a farm services consultant\" href=\"\/contact-us\" target=\"_blank\" rel=\"noopener\">farm services consultant<\/a><\/span>.<\/p>\n<p>Alternatively, register with us (below) to stay informed of field days in your region, affording you an opportunity to see for yourself the outstanding results of full-season P1756 hybrid corn.<\/p>","content2":"<h3>KEY FEATURES:<\/h3>\n<ul>\n<li>Superior husk cover and cob rot resistance, protecting grain quality as the crop matures<\/li>\n<li>Consistent, high performance in all full season growing environments<\/li>\n<li>Flexible end use with high grain yields, solid silage production and top quality processing grain<\/li>\n<\/ul>\n<p><img src=\"\/asset\/1981.png\" alt=\"P1756 - Growing region recommendations.png\" width=\"349\" height=\"507\" \/><\/p>","image":{"id":2266,"parent_id":1977,"name":"PIO25015-007 Corn A4 P1756 MOCKUP.png","description":null,"storage":"assets","size":1188967,"extension":"png","mime_type":"image\/png","width":1731,"height":1487,"keywords":null,"usage":{"corn_hybrids.23":"P1756"},"created_at":"2025-07-02T22:57:05.000000Z","updated_at":"2025-07-02T22:57:13.000000Z","readonly":null,"value":null,"_meta":null,"node_path":[{"id":1362,"name":"Hybrid icons","parent_id":null},{"id":1977,"name":"CORN P1756","parent_id":1362},{"id":2266,"name":"PIO25015-007 Corn A4 P1756 MOCKUP.png","parent_id":1977}],"link":"\/asset\/2266.png","readable_size":"1.13 MB","secured":false,"secured_token":"eyJ0eXAiOiJKV1QiLCJhbGciOiJIUzI1NiJ9.eyJzdG9yYWdlcyI6WyJzZWN1cmVfYXNzZXRzIl0sImZpbGUiOjIyNjZ9.4jAs0vsmXOTU5EhLXLHCzxOQcj3Motv5SVNk3rAprOA","full_path":"1362\/1977\/2266"},"custom_bag_image":null,"graph_image":null,"map_image":null,"new":0,"position":63,"plantheight":null,"type":"corn","title":"P1756","name_id":"p1756","meta_keywords":"corn, hybrid, vigour, hard, adaptability, yield, tolerance, processing, seed, Australia, yield","meta_description":"Discover a unique corn hybrid bred in Australia that boasts incredible vigour and adaptability, as well as excellent tolerance to various stress factors. This corn is specially developed for processing markets and offers significant yield advantages over other varieties.","tolerancetrait":null,"producttype":null,"maturity":"Full Season","phenology":null,"blacklegroup":null,"grainoilcontent":null,"plantvigour":null,"cropstandability":null,"shattertolerance":null,"graintestweight":null,"blacklegrating":null,"blacklegresistancegrouping":null,"performertype":null,"crmnumber":null,"crmposition":null,"graintoyieldmaturity":null,"droughttolerance":null,"stalkstrength":null,"rootstrength":null,"staygreen":null,"huskcover":null,"northernleafblight":null,"commonrust":null,"cobrot":null,"harvestdaystart":null,"harvestdayend":null,"silageyieldmaturity":null,"drylandadaptability":null,"wholeplantdigestibility":null,"agronomy_traits":{"grain_yield_for_maturity":"7","husk_cover":"7.5","plant_height":"7","cob_rot_resistance":"8","dryland_adaptability":"7","northern_leaf_blight":"7","silage_yield_for_maturity":"8","staygreen":"7","whole_plant_digestibility":"7"},"disease_traits":[],"characteristics":[],"recommendations":[],"crm":"117","heading":"P1756 Corn Hybrid","corn_traits":null,"crop":null,"fully_researched_and_proven":null,"improved_fermentation":null,"aerobic_stability":null,"improved_fibre_digestibility":null,"sub_heading":null,"best":null,"intro":"Well-known grain quality leader.","tech_notes":1983,"trait_ratings_disclaimer":null,"usage":"[\"Grain\",\"Silage\"]","purpose":null,"genetic":null,"search":"p1756","keywords":null,"content_id":351,"usage_display":"Grain \/ Silage","bag_image":null},"meta":{"priority":"position","priority_order":"asc","active":1,"created_at":"2021-03-11 17:41:58","updated_at":"2025-07-03 10:57:13"},"schema":{"collectionType":"hybrids","attributes":{"region_id":{"name":"region_id","type":"int","isRequired":false,"keyType":"","length":"10","default":null},"name":{"name":"name","type":"string","isRequired":false,"keyType":"","default":"","length":"255"},"content":{"type":"text"},"content2":{"name":"content2","type":"text","isRequired":false,"keyType":"","default":null},"image":{"name":"image","type":"asset","isRequired":false,"keyType":"","length":"11","default":null,"extensions":["jpeg","jpg","png","svg"],"upload_dir":null,"upload_storage":null},"custom_bag_image":{"name":"custom_bag_image","type":"asset","isRequired":false,"keyType":"","length":"11","default":null,"extensions":["jpeg","jpg","png","svg"],"upload_dir":null,"upload_storage":null},"graph_image":{"name":"graph_image","type":"asset","isRequired":false,"keyType":"","length":"11","default":null,"extensions":["jpeg","jpg","png","svg"],"upload_dir":null,"upload_storage":null},"map_image":{"name":"map_image","type":"int","isRequired":false,"keyType":"","length":"11","default":null},"new":{"name":"new","type":"tinyint","isRequired":false,"keyType":"","length":"1","default":null},"position":{"name":"position","type":"int","isRequired":false,"keyType":"","length":"11","default":null},"plantheight":{"name":"plantheight","type":"int","isRequired":false,"keyType":"","length":"11","default":null},"type":{"name":"type","type":"string","isRequired":false,"keyType":"","default":"","length":"255"},"title":{"name":"title","type":"string","isRequired":false,"keyType":"","default":"","length":"255"},"name_id":{"name":"name_id","type":"string","isRequired":false,"keyType":"","default":"","length":"255"},"meta_keywords":{"name":"meta_keywords","type":"text","isRequired":false,"keyType":"","default":null},"meta_description":{"name":"meta_description","type":"text","isRequired":false,"keyType":"","default":null},"tolerancetrait":{"name":"tolerancetrait","type":"string","isRequired":false,"keyType":"","default":"","length":"255"},"producttype":{"name":"producttype","type":"string","isRequired":false,"keyType":"","default":"","length":"255"},"maturity":{"name":"maturity","type":"string","isRequired":false,"keyType":"","default":"","length":"30"},"phenology":{"name":"phenology","type":"string","isRequired":false,"keyType":"","default":"","length":"30"},"blacklegroup":{"name":"blacklegroup","type":"string","isRequired":false,"keyType":"","default":"","length":"255"},"grainoilcontent":{"name":"grainoilcontent","type":"int","isRequired":false,"keyType":"","length":"11","default":null},"plantvigour":{"name":"plantvigour","type":"int","isRequired":false,"keyType":"","length":"11","default":null},"cropstandability":{"name":"cropstandability","type":"int","isRequired":false,"keyType":"","length":"11","default":null},"shattertolerance":{"name":"shattertolerance","type":"int","isRequired":false,"keyType":"","length":"11","default":null},"graintestweight":{"name":"graintestweight","type":"string","isRequired":false,"keyType":"","default":"","length":"11"},"blacklegrating":{"name":"blacklegrating","type":"string","isRequired":false,"keyType":"","default":"","length":"255"},"blacklegresistancegrouping":{"name":"blacklegresistancegrouping","type":"string","isRequired":false,"keyType":"","default":"","length":"255"},"performertype":{"name":"performertype","type":"enum","isRequired":false,"keyType":"","default":null,"length":"255","values":["Elite","Proven"]},"crmnumber":{"name":"crmnumber","type":"int","isRequired":false,"keyType":"","length":"11","default":null},"crmposition":{"name":"crmposition","type":"string","isRequired":false,"keyType":"","default":"","length":"255"},"graintoyieldmaturity":{"name":"graintoyieldmaturity","type":"string","isRequired":false,"keyType":"","default":"","length":"255"},"droughttolerance":{"name":"droughttolerance","type":"string","isRequired":false,"keyType":"","default":"","length":"255"},"stalkstrength":{"name":"stalkstrength","type":"string","isRequired":false,"keyType":"","default":"","length":"255"},"rootstrength":{"name":"rootstrength","type":"string","isRequired":false,"keyType":"","default":"","length":"255"},"staygreen":{"name":"staygreen","type":"string","isRequired":false,"keyType":"","default":"","length":"255"},"huskcover":{"name":"huskcover","type":"string","isRequired":false,"keyType":"","default":"","length":"255"},"northernleafblight":{"name":"northernleafblight","type":"string","isRequired":false,"keyType":"","default":"","length":"255"},"commonrust":{"name":"commonrust","type":"string","isRequired":false,"keyType":"","default":"","length":"255"},"cobrot":{"name":"cobrot","type":"string","isRequired":false,"keyType":"","default":"","length":"255"},"harvestdaystart":{"name":"harvestdaystart","type":"int","isRequired":false,"keyType":"","length":"11","default":null},"harvestdayend":{"name":"harvestdayend","type":"int","isRequired":false,"keyType":"","length":"11","default":null},"silageyieldmaturity":{"name":"silageyieldmaturity","type":"string","isRequired":false,"keyType":"","default":"","length":"255"},"drylandadaptability":{"name":"drylandadaptability","type":"string","isRequired":false,"keyType":"","default":"","length":"255"},"wholeplantdigestibility":{"name":"wholeplantdigestibility","type":"string","isRequired":false,"keyType":"","default":"","length":"255"},"agronomy_traits":{"name":"agronomy_traits","type":"object","isRequired":false,"keyType":"","default":null,"fields":[]},"disease_traits":{"name":"disease_traits","type":"text","isRequired":false,"keyType":"","default":null},"characteristics":{"name":"characteristics","type":"text","isRequired":false,"keyType":"","default":null},"recommendations":{"name":"recommendations","type":"text","isRequired":false,"keyType":"","default":null},"crm":{"name":"crm","type":"string","isRequired":false,"keyType":"","default":"","length":"255"},"heading":{"name":"heading","type":"string","isRequired":false,"keyType":"","default":"","length":"255"},"corn_traits":{"name":"corn_traits","type":"text","isRequired":false,"keyType":"","default":null},"crop":{"name":"crop","type":"string","isRequired":false,"keyType":"","default":"","length":"255"},"fully_researched_and_proven":{"name":"fully_researched_and_proven","type":"int","isRequired":false,"keyType":"","length":"11","default":null},"improved_fermentation":{"name":"improved_fermentation","type":"int","isRequired":false,"keyType":"","length":"11","default":null},"aerobic_stability":{"name":"aerobic_stability","type":"int","isRequired":false,"keyType":"","length":"11","default":null},"improved_fibre_digestibility":{"name":"improved_fibre_digestibility","type":"int","isRequired":false,"keyType":"","length":"11","default":null},"sub_heading":{"name":"sub_heading","type":"string","isRequired":false,"keyType":"","default":"","length":"255"},"best":{"name":"best","type":"string","isRequired":false,"keyType":"","default":"","length":"255"},"intro":{"name":"intro","type":"string","isRequired":false,"keyType":"","default":"","length":"255"},"tech_notes":{"name":"tech_notes","type":"int","isRequired":false,"keyType":"","length":"11","default":null},"trait_ratings_disclaimer":{"name":"trait_ratings_disclaimer","type":"string","isRequired":false,"keyType":"","default":"","length":"255"},"usage":{"name":"usage","type":"string","isRequired":false,"keyType":"","default":"","length":"511"},"purpose":{"name":"purpose","type":"string","isRequired":false,"keyType":"","default":"","length":"255"},"genetic":{"name":"genetic","type":"string","isRequired":false,"keyType":"","default":"","length":"255"},"search":{"name":"search","type":"text","isRequired":false,"keyType":"MUL","default":null},"keywords":{"name":"keywords","type":"text","isRequired":false,"keyType":"","default":null},"usage_display":{"name":"usage_display","type":"string"},"bag_image":{"name":"bag_image","type":"string"}},"relationships":{"files":{"label":null,"type":"HasMany","class":"HybridFile"},"panels":{"label":null,"type":"HasMany","class":"Panel","refs":"\/panels\/_ref_"},"resource":{"label":null,"type":"HasOne","class":"Resource"},"attached_panels":{"label":null,"type":"BelongsToMany","class":"AttachedPanel","refs":"\/attached_panels\/_ref_"}}},"included":[],"label":"P1756"},{"id":95,"type":"hybrid","attributes":{"id":95,"region_id":null,"name":"P17822 IT","content":"<p><img src=\"\/asset\/2064.png\" alt=\"P17822 IT - Segments and CRM.png\" width=\"281\" height=\"115\" \/> <img src=\"\/asset\/2063.png\" alt=\"P17822 IT - Maturity category.png\" width=\"176\" height=\"107\" \/><\/p>\n<h2>High yielding, full maturity behemoth.<\/h2>\n<p>Exceptional performance for silage and grain, breaking yield barriers.<\/p>\n<p>Outstanding new option to plant alongside P13036 IT, P15744 IT, and P2307 depending on maturity requirements.<\/p>","content2":"<h3>KEY FEATURES<\/h3>\n<ul>\n<li>Tall plant with excellent root and stalk strength, impressive staygreen and very high resistance to Northern Leaf Blight all combining for preferred silage appeal<\/li>\n<li>Produces great silage yields with maximum energy content<\/li>\n<li>Imidazolinone herbicide tolerance adds in crop flexibility to paddock selection and rotations<\/li>\n<\/ul>\n<p><img src=\"\/asset\/2066.png\" alt=\"P17822 IT - Growing region recommendations.png\" width=\"326\" height=\"463\" \/><\/p>","image":{"id":2267,"parent_id":2061,"name":"PIO25015-007 Corn A4 P17822 IT MOCKUP.png","description":null,"storage":"assets","size":1199657,"extension":"png","mime_type":"image\/png","width":1731,"height":1487,"keywords":null,"usage":{"corn_hybrids.95":"P17822 IT"},"created_at":"2025-07-02T22:58:32.000000Z","updated_at":"2025-07-02T22:58:39.000000Z","readonly":null,"value":null,"_meta":null,"node_path":[{"id":1362,"name":"Hybrid icons","parent_id":null},{"id":2061,"name":"CORN P17822 IT","parent_id":1362},{"id":2267,"name":"PIO25015-007 Corn A4 P17822 IT MOCKUP.png","parent_id":2061}],"link":"\/asset\/2267.png","readable_size":"1.14 MB","secured":false,"secured_token":"eyJ0eXAiOiJKV1QiLCJhbGciOiJIUzI1NiJ9.eyJzdG9yYWdlcyI6WyJzZWN1cmVfYXNzZXRzIl0sImZpbGUiOjIyNjd9.xpygN98Qw8LM-MykyTvdwX45z_HSDbNSBZqP7aBid1Q","full_path":"1362\/2061\/2267"},"custom_bag_image":null,"graph_image":null,"map_image":null,"new":1,"position":64,"plantheight":null,"type":"corn","title":"P17822 IT","name_id":"p-17822-it","meta_keywords":null,"meta_description":null,"tolerancetrait":null,"producttype":null,"maturity":"Full Season","phenology":null,"blacklegroup":null,"grainoilcontent":null,"plantvigour":null,"cropstandability":null,"shattertolerance":null,"graintestweight":null,"blacklegrating":null,"blacklegresistancegrouping":null,"performertype":null,"crmnumber":null,"crmposition":null,"graintoyieldmaturity":null,"droughttolerance":null,"stalkstrength":null,"rootstrength":null,"staygreen":null,"huskcover":null,"northernleafblight":null,"commonrust":null,"cobrot":null,"harvestdaystart":null,"harvestdayend":null,"silageyieldmaturity":null,"drylandadaptability":null,"wholeplantdigestibility":null,"agronomy_traits":{"grain_yield_for_maturity":"9","husk_cover":"7.5","plant_height":"8","cob_rot_resistance":"8","dryland_adaptability":"9","northern_leaf_blight":"8","silage_yield_for_maturity":"8","staygreen":"9","whole_plant_digestibility":"9"},"disease_traits":[],"characteristics":[],"recommendations":[],"crm":"117","heading":"P17822 IT Corn Hybrid","corn_traits":null,"crop":null,"fully_researched_and_proven":null,"improved_fermentation":null,"aerobic_stability":null,"improved_fibre_digestibility":null,"sub_heading":null,"best":null,"intro":"High yielding, full maturity behemoth.","tech_notes":2067,"trait_ratings_disclaimer":null,"usage":"[\"Grain\",\"Silage\"]","purpose":null,"genetic":null,"search":"p17822 kw_it","keywords":null,"content_id":1017,"usage_display":"Grain \/ Silage","bag_image":null},"meta":{"priority":"position","priority_order":"asc","active":1,"created_at":"2025-07-01 15:20:18","updated_at":"2025-07-03 10:58:39"},"schema":{"collectionType":"hybrids","attributes":{"region_id":{"name":"region_id","type":"int","isRequired":false,"keyType":"","length":"10","default":null},"name":{"name":"name","type":"string","isRequired":false,"keyType":"","default":"","length":"255"},"content":{"type":"text"},"content2":{"name":"content2","type":"text","isRequired":false,"keyType":"","default":null},"image":{"name":"image","type":"asset","isRequired":false,"keyType":"","length":"11","default":null,"extensions":["jpeg","jpg","png","svg"],"upload_dir":null,"upload_storage":null},"custom_bag_image":{"name":"custom_bag_image","type":"asset","isRequired":false,"keyType":"","length":"11","default":null,"extensions":["jpeg","jpg","png","svg"],"upload_dir":null,"upload_storage":null},"graph_image":{"name":"graph_image","type":"asset","isRequired":false,"keyType":"","length":"11","default":null,"extensions":["jpeg","jpg","png","svg"],"upload_dir":null,"upload_storage":null},"map_image":{"name":"map_image","type":"int","isRequired":false,"keyType":"","length":"11","default":null},"new":{"name":"new","type":"tinyint","isRequired":false,"keyType":"","length":"1","default":null},"position":{"name":"position","type":"int","isRequired":false,"keyType":"","length":"11","default":null},"plantheight":{"name":"plantheight","type":"int","isRequired":false,"keyType":"","length":"11","default":null},"type":{"name":"type","type":"string","isRequired":false,"keyType":"","default":"","length":"255"},"title":{"name":"title","type":"string","isRequired":false,"keyType":"","default":"","length":"255"},"name_id":{"name":"name_id","type":"string","isRequired":false,"keyType":"","default":"","length":"255"},"meta_keywords":{"name":"meta_keywords","type":"text","isRequired":false,"keyType":"","default":null},"meta_description":{"name":"meta_description","type":"text","isRequired":false,"keyType":"","default":null},"tolerancetrait":{"name":"tolerancetrait","type":"string","isRequired":false,"keyType":"","default":"","length":"255"},"producttype":{"name":"producttype","type":"string","isRequired":false,"keyType":"","default":"","length":"255"},"maturity":{"name":"maturity","type":"string","isRequired":false,"keyType":"","default":"","length":"30"},"phenology":{"name":"phenology","type":"string","isRequired":false,"keyType":"","default":"","length":"30"},"blacklegroup":{"name":"blacklegroup","type":"string","isRequired":false,"keyType":"","default":"","length":"255"},"grainoilcontent":{"name":"grainoilcontent","type":"int","isRequired":false,"keyType":"","length":"11","default":null},"plantvigour":{"name":"plantvigour","type":"int","isRequired":false,"keyType":"","length":"11","default":null},"cropstandability":{"name":"cropstandability","type":"int","isRequired":false,"keyType":"","length":"11","default":null},"shattertolerance":{"name":"shattertolerance","type":"int","isRequired":false,"keyType":"","length":"11","default":null},"graintestweight":{"name":"graintestweight","type":"string","isRequired":false,"keyType":"","default":"","length":"11"},"blacklegrating":{"name":"blacklegrating","type":"string","isRequired":false,"keyType":"","default":"","length":"255"},"blacklegresistancegrouping":{"name":"blacklegresistancegrouping","type":"string","isRequired":false,"keyType":"","default":"","length":"255"},"performertype":{"name":"performertype","type":"enum","isRequired":false,"keyType":"","default":null,"length":"255","values":["Elite","Proven"]},"crmnumber":{"name":"crmnumber","type":"int","isRequired":false,"keyType":"","length":"11","default":null},"crmposition":{"name":"crmposition","type":"string","isRequired":false,"keyType":"","default":"","length":"255"},"graintoyieldmaturity":{"name":"graintoyieldmaturity","type":"string","isRequired":false,"keyType":"","default":"","length":"255"},"droughttolerance":{"name":"droughttolerance","type":"string","isRequired":false,"keyType":"","default":"","length":"255"},"stalkstrength":{"name":"stalkstrength","type":"string","isRequired":false,"keyType":"","default":"","length":"255"},"rootstrength":{"name":"rootstrength","type":"string","isRequired":false,"keyType":"","default":"","length":"255"},"staygreen":{"name":"staygreen","type":"string","isRequired":false,"keyType":"","default":"","length":"255"},"huskcover":{"name":"huskcover","type":"string","isRequired":false,"keyType":"","default":"","length":"255"},"northernleafblight":{"name":"northernleafblight","type":"string","isRequired":false,"keyType":"","default":"","length":"255"},"commonrust":{"name":"commonrust","type":"string","isRequired":false,"keyType":"","default":"","length":"255"},"cobrot":{"name":"cobrot","type":"string","isRequired":false,"keyType":"","default":"","length":"255"},"harvestdaystart":{"name":"harvestdaystart","type":"int","isRequired":false,"keyType":"","length":"11","default":null},"harvestdayend":{"name":"harvestdayend","type":"int","isRequired":false,"keyType":"","length":"11","default":null},"silageyieldmaturity":{"name":"silageyieldmaturity","type":"string","isRequired":false,"keyType":"","default":"","length":"255"},"drylandadaptability":{"name":"drylandadaptability","type":"string","isRequired":false,"keyType":"","default":"","length":"255"},"wholeplantdigestibility":{"name":"wholeplantdigestibility","type":"string","isRequired":false,"keyType":"","default":"","length":"255"},"agronomy_traits":{"name":"agronomy_traits","type":"object","isRequired":false,"keyType":"","default":null,"fields":[]},"disease_traits":{"name":"disease_traits","type":"text","isRequired":false,"keyType":"","default":null},"characteristics":{"name":"characteristics","type":"text","isRequired":false,"keyType":"","default":null},"recommendations":{"name":"recommendations","type":"text","isRequired":false,"keyType":"","default":null},"crm":{"name":"crm","type":"string","isRequired":false,"keyType":"","default":"","length":"255"},"heading":{"name":"heading","type":"string","isRequired":false,"keyType":"","default":"","length":"255"},"corn_traits":{"name":"corn_traits","type":"text","isRequired":false,"keyType":"","default":null},"crop":{"name":"crop","type":"string","isRequired":false,"keyType":"","default":"","length":"255"},"fully_researched_and_proven":{"name":"fully_researched_and_proven","type":"int","isRequired":false,"keyType":"","length":"11","default":null},"improved_fermentation":{"name":"improved_fermentation","type":"int","isRequired":false,"keyType":"","length":"11","default":null},"aerobic_stability":{"name":"aerobic_stability","type":"int","isRequired":false,"keyType":"","length":"11","default":null},"improved_fibre_digestibility":{"name":"improved_fibre_digestibility","type":"int","isRequired":false,"keyType":"","length":"11","default":null},"sub_heading":{"name":"sub_heading","type":"string","isRequired":false,"keyType":"","default":"","length":"255"},"best":{"name":"best","type":"string","isRequired":false,"keyType":"","default":"","length":"255"},"intro":{"name":"intro","type":"string","isRequired":false,"keyType":"","default":"","length":"255"},"tech_notes":{"name":"tech_notes","type":"int","isRequired":false,"keyType":"","length":"11","default":null},"trait_ratings_disclaimer":{"name":"trait_ratings_disclaimer","type":"string","isRequired":false,"keyType":"","default":"","length":"255"},"usage":{"name":"usage","type":"string","isRequired":false,"keyType":"","default":"","length":"511"},"purpose":{"name":"purpose","type":"string","isRequired":false,"keyType":"","default":"","length":"255"},"genetic":{"name":"genetic","type":"string","isRequired":false,"keyType":"","default":"","length":"255"},"search":{"name":"search","type":"text","isRequired":false,"keyType":"MUL","default":null},"keywords":{"name":"keywords","type":"text","isRequired":false,"keyType":"","default":null},"usage_display":{"name":"usage_display","type":"string"},"bag_image":{"name":"bag_image","type":"string"}},"relationships":{"files":{"label":null,"type":"HasMany","class":"HybridFile"},"panels":{"label":null,"type":"HasMany","class":"Panel","refs":"\/panels\/_ref_"},"resource":{"label":null,"type":"HasOne","class":"Resource"},"attached_panels":{"label":null,"type":"BelongsToMany","class":"AttachedPanel","refs":"\/attached_panels\/_ref_"}}},"included":[],"label":"P17822 IT"},{"id":31,"type":"hybrid","attributes":{"id":31,"region_id":null,"name":"P1837","content":"<p><img src=\"\/asset\/1975.png\" alt=\"P1837 - Segments and CRM.png\" width=\"320\" height=\"100\" \/> <img src=\"\/asset\/1972.png\" alt=\"P1837 - Maturity category.png\" width=\"162\" height=\"99\" \/><\/p>\n<h2>Defensive, reliable, full-season competitor.<\/h2>\n<p>P1837 corn is an Australian bred high yielding 118 CRM processing, feed grain or silage corn hybrid.<\/p>\n<p>In Pioneer Seeds' national STRIKE testing program, P1837 has shown excellent grain yield being 5.6% higher than P1756.<\/p>\n<p>P1837 corn is a companion plant to <strong><a title=\"Pioneer 1756 corn\" href=\"\/our-products\/corn\/p1756\" target=\"_blank\" rel=\"noopener\">P1756 corn<\/a> <\/strong>and ideally suited to the Australian Processing Market.<\/p>\n<p>Perfect for grain or silage, <span style=\"font-size: 1rem;\">P1837 corn <\/span><span style=\"font-size: 1rem;\">grows well from southern NSW to northern Australia. <\/span><\/p>\n<p>Just as importantly, P1837 corn also scores highly in its resistance to northern leaf blight and fusarium.<\/p>\n<p><img src=\"\/asset\/231.jpeg\" alt=\"P1837_Corn-img-01.jpg\" \/><\/p>\n<p>Discuss planting options with a <strong><a title=\"Our team\" href=\"\/around-the-seed\/our-team\">Pioneer Brand Seeds representative<\/a> <\/strong>near you.<\/p>\n<p>Alternatively, register with us (below) to stay informed of field days in your region, affording you an opportunity to see for yourself the outstanding results of full-season P1837 hybrid corn.<\/p>","content2":"<h3>KEY FEATURES<\/h3>\n<ul>\n<li>Excellent drought tolerance and staygreen which support season long silage appeal<\/li>\n<li>Has better foliar health than P1756 while being slightly later in maturity<\/li>\n<li>This hybrid adapts well to a range of populations, suitable for dryland and irrigated situations<\/li>\n<\/ul>\n<p><img src=\"\/asset\/1974.png\" alt=\"P1837 - Growing region recommendations.png\" width=\"326\" height=\"398\" \/><\/p>","image":{"id":2268,"parent_id":1970,"name":"PIO25015-007 Corn A4 P1837 MOCKUP.png","description":null,"storage":"assets","size":1110335,"extension":"png","mime_type":"image\/png","width":1731,"height":1487,"keywords":null,"usage":{"corn_hybrids.31":"P1837"},"created_at":"2025-07-02T22:59:25.000000Z","updated_at":"2025-07-02T22:59:36.000000Z","readonly":null,"value":null,"_meta":null,"node_path":[{"id":1362,"name":"Hybrid icons","parent_id":null},{"id":1970,"name":"CORN P1837","parent_id":1362},{"id":2268,"name":"PIO25015-007 Corn A4 P1837 MOCKUP.png","parent_id":1970}],"link":"\/asset\/2268.png","readable_size":"1.06 MB","secured":false,"secured_token":"eyJ0eXAiOiJKV1QiLCJhbGciOiJIUzI1NiJ9.eyJzdG9yYWdlcyI6WyJzZWN1cmVfYXNzZXRzIl0sImZpbGUiOjIyNjh9.VvCDoCGlrYpIuJFQbrLIKcbjTNTSgeZVPmBnOkEc6ZY","full_path":"1362\/1970\/2268"},"custom_bag_image":null,"graph_image":null,"map_image":null,"new":0,"position":66,"plantheight":null,"type":"corn","title":"P1837","name_id":"p1837","meta_keywords":"corn, hybrid, vigour, hard, tall, silage, yield, tolerance, seed, Australia","meta_description":"Discover the characteristics of high-yielding processing corn hybrids that are vigorous, hard, tall, and have high tolerance to stress. Learn how to grow and harvest silage corn to maximise yield for feed production.","tolerancetrait":null,"producttype":null,"maturity":"Full Season","phenology":null,"blacklegroup":null,"grainoilcontent":null,"plantvigour":null,"cropstandability":null,"shattertolerance":null,"graintestweight":null,"blacklegrating":null,"blacklegresistancegrouping":null,"performertype":null,"crmnumber":null,"crmposition":null,"graintoyieldmaturity":null,"droughttolerance":null,"stalkstrength":null,"rootstrength":null,"staygreen":null,"huskcover":null,"northernleafblight":null,"commonrust":null,"cobrot":null,"harvestdaystart":null,"harvestdayend":null,"silageyieldmaturity":null,"drylandadaptability":null,"wholeplantdigestibility":null,"agronomy_traits":{"grain_yield_for_maturity":"8","husk_cover":"7.5","plant_height":"7","cob_rot_resistance":"8","dryland_adaptability":"8","northern_leaf_blight":"7","silage_yield_for_maturity":"8","staygreen":"8","whole_plant_digestibility":"7"},"disease_traits":[],"characteristics":[],"recommendations":[],"crm":"118","heading":"P1837 Corn Hybrid","corn_traits":null,"crop":null,"fully_researched_and_proven":null,"improved_fermentation":null,"aerobic_stability":null,"improved_fibre_digestibility":null,"sub_heading":null,"best":null,"intro":"Defensive, reliable, full-season competitor.","tech_notes":1976,"trait_ratings_disclaimer":null,"usage":"[\"Grain\",\"Silage\"]","purpose":null,"genetic":null,"search":"p1837","keywords":null,"content_id":350,"usage_display":"Grain \/ Silage","bag_image":null},"meta":{"priority":"position","priority_order":"asc","active":1,"created_at":"2021-03-11 17:44:32","updated_at":"2025-07-03 10:59:36"},"schema":{"collectionType":"hybrids","attributes":{"region_id":{"name":"region_id","type":"int","isRequired":false,"keyType":"","length":"10","default":null},"name":{"name":"name","type":"string","isRequired":false,"keyType":"","default":"","length":"255"},"content":{"type":"text"},"content2":{"name":"content2","type":"text","isRequired":false,"keyType":"","default":null},"image":{"name":"image","type":"asset","isRequired":false,"keyType":"","length":"11","default":null,"extensions":["jpeg","jpg","png","svg"],"upload_dir":null,"upload_storage":null},"custom_bag_image":{"name":"custom_bag_image","type":"asset","isRequired":false,"keyType":"","length":"11","default":null,"extensions":["jpeg","jpg","png","svg"],"upload_dir":null,"upload_storage":null},"graph_image":{"name":"graph_image","type":"asset","isRequired":false,"keyType":"","length":"11","default":null,"extensions":["jpeg","jpg","png","svg"],"upload_dir":null,"upload_storage":null},"map_image":{"name":"map_image","type":"int","isRequired":false,"keyType":"","length":"11","default":null},"new":{"name":"new","type":"tinyint","isRequired":false,"keyType":"","length":"1","default":null},"position":{"name":"position","type":"int","isRequired":false,"keyType":"","length":"11","default":null},"plantheight":{"name":"plantheight","type":"int","isRequired":false,"keyType":"","length":"11","default":null},"type":{"name":"type","type":"string","isRequired":false,"keyType":"","default":"","length":"255"},"title":{"name":"title","type":"string","isRequired":false,"keyType":"","default":"","length":"255"},"name_id":{"name":"name_id","type":"string","isRequired":false,"keyType":"","default":"","length":"255"},"meta_keywords":{"name":"meta_keywords","type":"text","isRequired":false,"keyType":"","default":null},"meta_description":{"name":"meta_description","type":"text","isRequired":false,"keyType":"","default":null},"tolerancetrait":{"name":"tolerancetrait","type":"string","isRequired":false,"keyType":"","default":"","length":"255"},"producttype":{"name":"producttype","type":"string","isRequired":false,"keyType":"","default":"","length":"255"},"maturity":{"name":"maturity","type":"string","isRequired":false,"keyType":"","default":"","length":"30"},"phenology":{"name":"phenology","type":"string","isRequired":false,"keyType":"","default":"","length":"30"},"blacklegroup":{"name":"blacklegroup","type":"string","isRequired":false,"keyType":"","default":"","length":"255"},"grainoilcontent":{"name":"grainoilcontent","type":"int","isRequired":false,"keyType":"","length":"11","default":null},"plantvigour":{"name":"plantvigour","type":"int","isRequired":false,"keyType":"","length":"11","default":null},"cropstandability":{"name":"cropstandability","type":"int","isRequired":false,"keyType":"","length":"11","default":null},"shattertolerance":{"name":"shattertolerance","type":"int","isRequired":false,"keyType":"","length":"11","default":null},"graintestweight":{"name":"graintestweight","type":"string","isRequired":false,"keyType":"","default":"","length":"11"},"blacklegrating":{"name":"blacklegrating","type":"string","isRequired":false,"keyType":"","default":"","length":"255"},"blacklegresistancegrouping":{"name":"blacklegresistancegrouping","type":"string","isRequired":false,"keyType":"","default":"","length":"255"},"performertype":{"name":"performertype","type":"enum","isRequired":false,"keyType":"","default":null,"length":"255","values":["Elite","Proven"]},"crmnumber":{"name":"crmnumber","type":"int","isRequired":false,"keyType":"","length":"11","default":null},"crmposition":{"name":"crmposition","type":"string","isRequired":false,"keyType":"","default":"","length":"255"},"graintoyieldmaturity":{"name":"graintoyieldmaturity","type":"string","isRequired":false,"keyType":"","default":"","length":"255"},"droughttolerance":{"name":"droughttolerance","type":"string","isRequired":false,"keyType":"","default":"","length":"255"},"stalkstrength":{"name":"stalkstrength","type":"string","isRequired":false,"keyType":"","default":"","length":"255"},"rootstrength":{"name":"rootstrength","type":"string","isRequired":false,"keyType":"","default":"","length":"255"},"staygreen":{"name":"staygreen","type":"string","isRequired":false,"keyType":"","default":"","length":"255"},"huskcover":{"name":"huskcover","type":"string","isRequired":false,"keyType":"","default":"","length":"255"},"northernleafblight":{"name":"northernleafblight","type":"string","isRequired":false,"keyType":"","default":"","length":"255"},"commonrust":{"name":"commonrust","type":"string","isRequired":false,"keyType":"","default":"","length":"255"},"cobrot":{"name":"cobrot","type":"string","isRequired":false,"keyType":"","default":"","length":"255"},"harvestdaystart":{"name":"harvestdaystart","type":"int","isRequired":false,"keyType":"","length":"11","default":null},"harvestdayend":{"name":"harvestdayend","type":"int","isRequired":false,"keyType":"","length":"11","default":null},"silageyieldmaturity":{"name":"silageyieldmaturity","type":"string","isRequired":false,"keyType":"","default":"","length":"255"},"drylandadaptability":{"name":"drylandadaptability","type":"string","isRequired":false,"keyType":"","default":"","length":"255"},"wholeplantdigestibility":{"name":"wholeplantdigestibility","type":"string","isRequired":false,"keyType":"","default":"","length":"255"},"agronomy_traits":{"name":"agronomy_traits","type":"object","isRequired":false,"keyType":"","default":null,"fields":[]},"disease_traits":{"name":"disease_traits","type":"text","isRequired":false,"keyType":"","default":null},"characteristics":{"name":"characteristics","type":"text","isRequired":false,"keyType":"","default":null},"recommendations":{"name":"recommendations","type":"text","isRequired":false,"keyType":"","default":null},"crm":{"name":"crm","type":"string","isRequired":false,"keyType":"","default":"","length":"255"},"heading":{"name":"heading","type":"string","isRequired":false,"keyType":"","default":"","length":"255"},"corn_traits":{"name":"corn_traits","type":"text","isRequired":false,"keyType":"","default":null},"crop":{"name":"crop","type":"string","isRequired":false,"keyType":"","default":"","length":"255"},"fully_researched_and_proven":{"name":"fully_researched_and_proven","type":"int","isRequired":false,"keyType":"","length":"11","default":null},"improved_fermentation":{"name":"improved_fermentation","type":"int","isRequired":false,"keyType":"","length":"11","default":null},"aerobic_stability":{"name":"aerobic_stability","type":"int","isRequired":false,"keyType":"","length":"11","default":null},"improved_fibre_digestibility":{"name":"improved_fibre_digestibility","type":"int","isRequired":false,"keyType":"","length":"11","default":null},"sub_heading":{"name":"sub_heading","type":"string","isRequired":false,"keyType":"","default":"","length":"255"},"best":{"name":"best","type":"string","isRequired":false,"keyType":"","default":"","length":"255"},"intro":{"name":"intro","type":"string","isRequired":false,"keyType":"","default":"","length":"255"},"tech_notes":{"name":"tech_notes","type":"int","isRequired":false,"keyType":"","length":"11","default":null},"trait_ratings_disclaimer":{"name":"trait_ratings_disclaimer","type":"string","isRequired":false,"keyType":"","default":"","length":"255"},"usage":{"name":"usage","type":"string","isRequired":false,"keyType":"","default":"","length":"511"},"purpose":{"name":"purpose","type":"string","isRequired":false,"keyType":"","default":"","length":"255"},"genetic":{"name":"genetic","type":"string","isRequired":false,"keyType":"","default":"","length":"255"},"search":{"name":"search","type":"text","isRequired":false,"keyType":"MUL","default":null},"keywords":{"name":"keywords","type":"text","isRequired":false,"keyType":"","default":null},"usage_display":{"name":"usage_display","type":"string"},"bag_image":{"name":"bag_image","type":"string"}},"relationships":{"files":{"label":null,"type":"HasMany","class":"HybridFile"},"panels":{"label":null,"type":"HasMany","class":"Panel","refs":"\/panels\/_ref_"},"resource":{"label":null,"type":"HasOne","class":"Resource"},"attached_panels":{"label":null,"type":"BelongsToMany","class":"AttachedPanel","refs":"\/attached_panels\/_ref_"}}},"included":[],"label":"P1837"},{"id":22,"type":"hybrid","attributes":{"id":22,"region_id":null,"name":"P2307","content":"<p><img src=\"\/asset\/1965.png\" alt=\"P2307 - Segments and CRM.png\" width=\"187\" height=\"82\" \/> <img src=\"\/asset\/1964.png\" alt=\"P2307 - Maturity category.png\" width=\"131\" height=\"80\" \/><\/p>\n<h2>Silage and coastal grain specialist.<\/h2>\n<p>P2307 is an excellent silage option for growers requiring reliable silage production in coastal and northern regions with high Northern Leaf Blight pressure.<\/p>","content2":"<h3>KEY FEATURES<\/h3>\n<ul>\n<li>A tall corn hybrid with excellent silage yield<\/li>\n<li>High tolerance to Northern Leaf Blight<\/li>\n<li>Exceptional late season plant health<\/li>\n<li>Suitable for all planting times<\/li>\n<li>Hard textured, flinty corn grain<\/li>\n<li>Ideal for coastal and northern regions as well as high yielding silage production areas<\/li>\n<\/ul>\n<p><img src=\"\/asset\/1967.png\" alt=\"P2307 - Growing region recommendations.png\" width=\"293\" height=\"422\" \/><\/p>","image":{"id":2269,"parent_id":1962,"name":"PIO25015-007 Corn A4 P2307 MOCKUP.png","description":null,"storage":"assets","size":1190966,"extension":"png","mime_type":"image\/png","width":1731,"height":1487,"keywords":null,"usage":{"corn_hybrids.22":"P2307"},"created_at":"2025-07-02T23:00:33.000000Z","updated_at":"2025-07-02T23:00:53.000000Z","readonly":null,"value":null,"_meta":null,"node_path":[{"id":1362,"name":"Hybrid icons","parent_id":null},{"id":1962,"name":"CORN P2307","parent_id":1362},{"id":2269,"name":"PIO25015-007 Corn A4 P2307 MOCKUP.png","parent_id":1962}],"link":"\/asset\/2269.png","readable_size":"1.14 MB","secured":false,"secured_token":"eyJ0eXAiOiJKV1QiLCJhbGciOiJIUzI1NiJ9.eyJzdG9yYWdlcyI6WyJzZWN1cmVfYXNzZXRzIl0sImZpbGUiOjIyNjl9.VDbb1OJUZttWSrG58BHqGcdD_7n5P3wey9OI-PDzW1c","full_path":"1362\/1962\/2269"},"custom_bag_image":null,"graph_image":null,"map_image":null,"new":0,"position":70,"plantheight":null,"type":"corn","title":"P2307","name_id":"p2307","meta_keywords":"corn, hybrid, vigour, hard, tall, silage, yield, tolerance, seed, wind","meta_description":"This exceptional late-season hybrid corn boasts hard, flinty grain and impressive vigour. It stands tall and produces high-yielding silage, with excellent resistance to disease and environmental stress. Learn more about its exceptional qualities and benefits.","tolerancetrait":null,"producttype":null,"maturity":"Full Season","phenology":null,"blacklegroup":null,"grainoilcontent":null,"plantvigour":null,"cropstandability":null,"shattertolerance":null,"graintestweight":null,"blacklegrating":null,"blacklegresistancegrouping":null,"performertype":null,"crmnumber":null,"crmposition":null,"graintoyieldmaturity":null,"droughttolerance":null,"stalkstrength":null,"rootstrength":null,"staygreen":null,"huskcover":null,"northernleafblight":null,"commonrust":null,"cobrot":null,"harvestdaystart":null,"harvestdayend":null,"silageyieldmaturity":null,"drylandadaptability":null,"wholeplantdigestibility":null,"agronomy_traits":{"grain_yield_for_maturity":"7","husk_cover":"8.5","plant_height":"9","cob_rot_resistance":"7","dryland_adaptability":"7","northern_leaf_blight":"9","silage_yield_for_maturity":"9","staygreen":"10","whole_plant_digestibility":"6"},"disease_traits":[],"characteristics":[],"recommendations":[],"crm":"123","heading":"P2307 Corn Hybrid","corn_traits":null,"crop":null,"fully_researched_and_proven":null,"improved_fermentation":null,"aerobic_stability":null,"improved_fibre_digestibility":null,"sub_heading":null,"best":null,"intro":"Full season silage and coastal grain specialist","tech_notes":1968,"trait_ratings_disclaimer":null,"usage":"[\"Grain\",\"Silage\"]","purpose":null,"genetic":null,"search":"p2307","keywords":null,"content_id":349,"usage_display":"Grain \/ Silage","bag_image":null},"meta":{"priority":"position","priority_order":"asc","active":1,"created_at":"2021-03-11 17:41:43","updated_at":"2025-07-03 11:00:53"},"schema":{"collectionType":"hybrids","attributes":{"region_id":{"name":"region_id","type":"int","isRequired":false,"keyType":"","length":"10","default":null},"name":{"name":"name","type":"string","isRequired":false,"keyType":"","default":"","length":"255"},"content":{"type":"text"},"content2":{"name":"content2","type":"text","isRequired":false,"keyType":"","default":null},"image":{"name":"image","type":"asset","isRequired":false,"keyType":"","length":"11","default":null,"extensions":["jpeg","jpg","png","svg"],"upload_dir":null,"upload_storage":null},"custom_bag_image":{"name":"custom_bag_image","type":"asset","isRequired":false,"keyType":"","length":"11","default":null,"extensions":["jpeg","jpg","png","svg"],"upload_dir":null,"upload_storage":null},"graph_image":{"name":"graph_image","type":"asset","isRequired":false,"keyType":"","length":"11","default":null,"extensions":["jpeg","jpg","png","svg"],"upload_dir":null,"upload_storage":null},"map_image":{"name":"map_image","type":"int","isRequired":false,"keyType":"","length":"11","default":null},"new":{"name":"new","type":"tinyint","isRequired":false,"keyType":"","length":"1","default":null},"position":{"name":"position","type":"int","isRequired":false,"keyType":"","length":"11","default":null},"plantheight":{"name":"plantheight","type":"int","isRequired":false,"keyType":"","length":"11","default":null},"type":{"name":"type","type":"string","isRequired":false,"keyType":"","default":"","length":"255"},"title":{"name":"title","type":"string","isRequired":false,"keyType":"","default":"","length":"255"},"name_id":{"name":"name_id","type":"string","isRequired":false,"keyType":"","default":"","length":"255"},"meta_keywords":{"name":"meta_keywords","type":"text","isRequired":false,"keyType":"","default":null},"meta_description":{"name":"meta_description","type":"text","isRequired":false,"keyType":"","default":null},"tolerancetrait":{"name":"tolerancetrait","type":"string","isRequired":false,"keyType":"","default":"","length":"255"},"producttype":{"name":"producttype","type":"string","isRequired":false,"keyType":"","default":"","length":"255"},"maturity":{"name":"maturity","type":"string","isRequired":false,"keyType":"","default":"","length":"30"},"phenology":{"name":"phenology","type":"string","isRequired":false,"keyType":"","default":"","length":"30"},"blacklegroup":{"name":"blacklegroup","type":"string","isRequired":false,"keyType":"","default":"","length":"255"},"grainoilcontent":{"name":"grainoilcontent","type":"int","isRequired":false,"keyType":"","length":"11","default":null},"plantvigour":{"name":"plantvigour","type":"int","isRequired":false,"keyType":"","length":"11","default":null},"cropstandability":{"name":"cropstandability","type":"int","isRequired":false,"keyType":"","length":"11","default":null},"shattertolerance":{"name":"shattertolerance","type":"int","isRequired":false,"keyType":"","length":"11","default":null},"graintestweight":{"name":"graintestweight","type":"string","isRequired":false,"keyType":"","default":"","length":"11"},"blacklegrating":{"name":"blacklegrating","type":"string","isRequired":false,"keyType":"","default":"","length":"255"},"blacklegresistancegrouping":{"name":"blacklegresistancegrouping","type":"string","isRequired":false,"keyType":"","default":"","length":"255"},"performertype":{"name":"performertype","type":"enum","isRequired":false,"keyType":"","default":null,"length":"255","values":["Elite","Proven"]},"crmnumber":{"name":"crmnumber","type":"int","isRequired":false,"keyType":"","length":"11","default":null},"crmposition":{"name":"crmposition","type":"string","isRequired":false,"keyType":"","default":"","length":"255"},"graintoyieldmaturity":{"name":"graintoyieldmaturity","type":"string","isRequired":false,"keyType":"","default":"","length":"255"},"droughttolerance":{"name":"droughttolerance","type":"string","isRequired":false,"keyType":"","default":"","length":"255"},"stalkstrength":{"name":"stalkstrength","type":"string","isRequired":false,"keyType":"","default":"","length":"255"},"rootstrength":{"name":"rootstrength","type":"string","isRequired":false,"keyType":"","default":"","length":"255"},"staygreen":{"name":"staygreen","type":"string","isRequired":false,"keyType":"","default":"","length":"255"},"huskcover":{"name":"huskcover","type":"string","isRequired":false,"keyType":"","default":"","length":"255"},"northernleafblight":{"name":"northernleafblight","type":"string","isRequired":false,"keyType":"","default":"","length":"255"},"commonrust":{"name":"commonrust","type":"string","isRequired":false,"keyType":"","default":"","length":"255"},"cobrot":{"name":"cobrot","type":"string","isRequired":false,"keyType":"","default":"","length":"255"},"harvestdaystart":{"name":"harvestdaystart","type":"int","isRequired":false,"keyType":"","length":"11","default":null},"harvestdayend":{"name":"harvestdayend","type":"int","isRequired":false,"keyType":"","length":"11","default":null},"silageyieldmaturity":{"name":"silageyieldmaturity","type":"string","isRequired":false,"keyType":"","default":"","length":"255"},"drylandadaptability":{"name":"drylandadaptability","type":"string","isRequired":false,"keyType":"","default":"","length":"255"},"wholeplantdigestibility":{"name":"wholeplantdigestibility","type":"string","isRequired":false,"keyType":"","default":"","length":"255"},"agronomy_traits":{"name":"agronomy_traits","type":"object","isRequired":false,"keyType":"","default":null,"fields":[]},"disease_traits":{"name":"disease_traits","type":"text","isRequired":false,"keyType":"","default":null},"characteristics":{"name":"characteristics","type":"text","isRequired":false,"keyType":"","default":null},"recommendations":{"name":"recommendations","type":"text","isRequired":false,"keyType":"","default":null},"crm":{"name":"crm","type":"string","isRequired":false,"keyType":"","default":"","length":"255"},"heading":{"name":"heading","type":"string","isRequired":false,"keyType":"","default":"","length":"255"},"corn_traits":{"name":"corn_traits","type":"text","isRequired":false,"keyType":"","default":null},"crop":{"name":"crop","type":"string","isRequired":false,"keyType":"","default":"","length":"255"},"fully_researched_and_proven":{"name":"fully_researched_and_proven","type":"int","isRequired":false,"keyType":"","length":"11","default":null},"improved_fermentation":{"name":"improved_fermentation","type":"int","isRequired":false,"keyType":"","length":"11","default":null},"aerobic_stability":{"name":"aerobic_stability","type":"int","isRequired":false,"keyType":"","length":"11","default":null},"improved_fibre_digestibility":{"name":"improved_fibre_digestibility","type":"int","isRequired":false,"keyType":"","length":"11","default":null},"sub_heading":{"name":"sub_heading","type":"string","isRequired":false,"keyType":"","default":"","length":"255"},"best":{"name":"best","type":"string","isRequired":false,"keyType":"","default":"","length":"255"},"intro":{"name":"intro","type":"string","isRequired":false,"keyType":"","default":"","length":"255"},"tech_notes":{"name":"tech_notes","type":"int","isRequired":false,"keyType":"","length":"11","default":null},"trait_ratings_disclaimer":{"name":"trait_ratings_disclaimer","type":"string","isRequired":false,"keyType":"","default":"","length":"255"},"usage":{"name":"usage","type":"string","isRequired":false,"keyType":"","default":"","length":"511"},"purpose":{"name":"purpose","type":"string","isRequired":false,"keyType":"","default":"","length":"255"},"genetic":{"name":"genetic","type":"string","isRequired":false,"keyType":"","default":"","length":"255"},"search":{"name":"search","type":"text","isRequired":false,"keyType":"MUL","default":null},"keywords":{"name":"keywords","type":"text","isRequired":false,"keyType":"","default":null},"usage_display":{"name":"usage_display","type":"string"},"bag_image":{"name":"bag_image","type":"string"}},"relationships":{"files":{"label":null,"type":"HasMany","class":"HybridFile"},"panels":{"label":null,"type":"HasMany","class":"Panel","refs":"\/panels\/_ref_"},"resource":{"label":null,"type":"HasOne","class":"Resource"},"attached_panels":{"label":null,"type":"BelongsToMany","class":"AttachedPanel","refs":"\/attached_panels\/_ref_"}}},"included":[],"label":"P2307"}]}},"config":{"path":"our-products\/corn","page":{"id":50,"parent_id":26,"image":707,"image_header":null,"name":"Corn","title":"Corn Hybrids","heading":"Trusted corn hybrids for quality grain and silage.","subheading":"Pioneer\u00ae Brand Canola hybrids","content_type":"default","name_id":"corn","path":"our-products\/corn","redirect_url":"\/our-products\/corn-hybrids","meta_description":"Pioneer\u00ae brand seeds has made a commitment to Australian farmers to deliver high yielding corn hybrids. Tested in local conditions, trials show outstanding corn yield, profitability and disease resistance. Learn more about Pioneer corn here.","meta_keywords":"Pioneer seeds, corn seeds, Australia, pioneer, corn, pioneer, corn hybrids, seed, maize, maize, hybrids, farming, corn farming, grow corn, P1481, P0937, P2307, P1837, P1756, P1467, P1315-IT, P1197, P9911, P9127, P8500, P1477W, P7524","meta_no_index":0,"open_in_new_tab":0,"homepage":0,"show_in_menu":1,"show_in_top_menu":0,"show_in_footer":1,"show_in_responsive_menu":1,"template":"hybrid","position":50,"active":1,"created_at":"2021-02-21T22:13:51.000000Z","updated_at":"2025-07-01T00:08:32.000000Z","content":"<p><\/p>","content2":"<p><\/p>","colour":"orange","intro":"Trusted corn hybrids for quality grain and silage.","hybrid_type":"corn","layout_id":null,"search":"corn trusted corn hybrids quality grain and silage ","keywords":null,"content_id":275,"images":[],"layout":null,"attached_panels":[{"id":166,"content_id":275,"name":"New text-3-column","type":"text-3-column","position":166,"active":1,"created_at":"2021-02-25T20:28:51.000000Z","updated_at":"2025-07-01T00:08:32.000000Z","title":null,"content":"<h2>Uniquely Australian bred corn hybrids developed with excellent trait packages<\/h2>","content_2":"<p>Pioneer® Brand corn hybrids are developed and tested in local conditions to ensure they represent superior products to what is currently available. Our hybrid corn varieties have something to offer farmers in all regions and cropping environments across Australia.<\/p>\n<p><span style=\"font-size: 1rem;\">As with all our products, there’s always a Pioneer® <strong><a title=\"contact the Pioneer team\" href=\"\/around-the-seed\/our-team\" target=\"_blank\" rel=\"noopener\">Territory Sales Manager or Farm Services Consultant<\/a><\/strong> in your local area to help you choose the right hybrid corn seeds and provide on-farm backup and technical support.<\/span><\/p>\n<p><span style=\"font-size: 1rem;\">We’re committed to providing helpful management advice and support to assist local farmers in making optimum profit from our products.<\/span><\/p>\n<p><a href=\"\/resource-centre\/corn-resources\/technical-insights-agronomy-info\/pioneer-corn-hybrid-naming-conventions\"><span style=\"font-size: 1rem;\"><img src=\"\/asset\/786.jpeg\" alt=\"naming-banner-corn.jpg\" width=\"252\" height=\"173\" \/><\/span><\/a><\/p>","content_3":"<p>View or download our 2025-26 Summer Crop guide below.<\/p>","file":{"id":1958,"parent_id":1362,"name":"PIO25026 Summer Brochure A5 MK16.pdf","description":null,"storage":"assets","size":6684505,"extension":"pdf","mime_type":"application\/pdf","width":null,"height":null,"keywords":null,"usage":{"panels.166":"New text-3-column"},"created_at":"2025-07-01T00:00:53.000000Z","updated_at":"2025-07-01T00:01:05.000000Z","readonly":null,"value":null,"_meta":null,"node_path":[{"id":1362,"name":"Hybrid icons","parent_id":null},{"id":1958,"name":"PIO25026 Summer Brochure A5 MK16.pdf","parent_id":1362}],"link":"\/asset\/1958.jpg","readable_size":"6.37 MB","secured":false,"secured_token":"eyJ0eXAiOiJKV1QiLCJhbGciOiJIUzI1NiJ9.eyJzdG9yYWdlcyI6WyJzZWN1cmVfYXNzZXRzIl0sImZpbGUiOjE5NTh9.N1z-zBF1C6j_0D2vDWxZL0y-skLkkX2fJVyKNs8YXIg","full_path":"1362\/1958"},"border_top":0,"border_bottom":0,"padding_top":1,"padding_bottom":0,"margin_top":0,"margin_bottom":0,"background":"white","pardot_campaign":null,"pivot":{"content_id":275,"panel_id":166,"active":1,"section":"before","position":17}}]},"filters":{"types":{"label":"Usage","field":"usage","values":["Silage","Grain","Specialty","Dual Purpose"]},"maturity":{"label":"Maturity","field":"maturity","values":["Full Season","Mid Season","Short Season"]}}}}